Polish Glass Fiber Reinforced Plastic Compression Molds,How to polish the glass fiber reinforced plastic compression mold? Glass Fiber Reinforced Plastic (GRP) compression molds play a critical role in the production of various components, providing the necessary shapes and textures to finished products. Achieving a high-quality finish on these molds is essential for ensuring the accurate replication of patterns and minimizing defects in the final GRP products. Polishing the molds is a crucial step in this process. Here’s a guide on how to effectively polish GRP compression molds:
Table of Contents
TogglePolish Glass Fiber Reinforced Plastic Compression Molds
1. Cleaning
Before starting the polishing process, ensure that the mold is thoroughly cleaned to remove any residue, debris, or release agents. Cleaning the mold’s surface helps achieve a consistent and even polish.
2. Inspection
Carefully inspect the mold’s surface for any defects, imperfections, or irregularities. Addressing these issues before polishing can prevent them from becoming more pronounced during the polishing process.
3. Selecting the Right Polishing Compound
Choose a polishing compound suitable for GRP materials. Depending on the level of surface imperfections, you may need to select a coarser or finer compound. Test a small area first to ensure that the chosen compound is effective and doesn’t cause damage.
4. Coarse Polishing
Begin with a coarse polishing compound and a polishing pad. Apply the compound to the pad and work it onto the mold’s surface using circular or back-and-forth motions. Apply moderate pressure, focusing on areas with visible imperfections. This step helps remove larger scratches, blemishes, and irregularities.
6. Fine Polishing
Move on to a fine-grit polishing compound to achieve a smoother finish. Fine polishing should help eliminate the finer scratches left by previous steps and bring out a higher level of shine.
7. Buffing
For the final touch, use a soft buffing pad with a polishing compound or wax. Buff the mold’s surface in circular motions to enhance its shine and smoothness.
8. Inspection and Touch-up
After the polishing process, thoroughly inspect the mold’s surface for any remaining imperfections or areas that need touch-up. Address these areas before proceeding to the next steps in the production process.
9. Maintenance
To maintain the polished finish, regularly clean the mold’s surface after each use to prevent residue buildup. Periodic light polishing can help restore the shine and smoothness as needed.
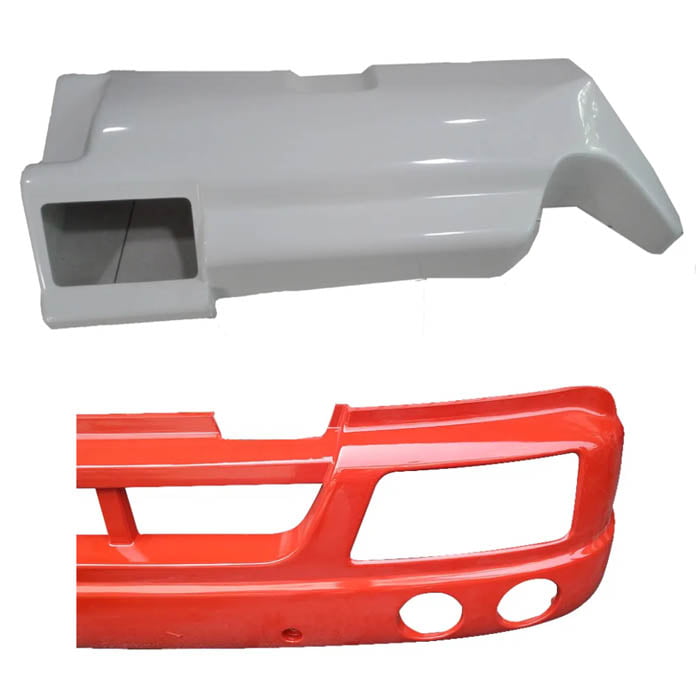
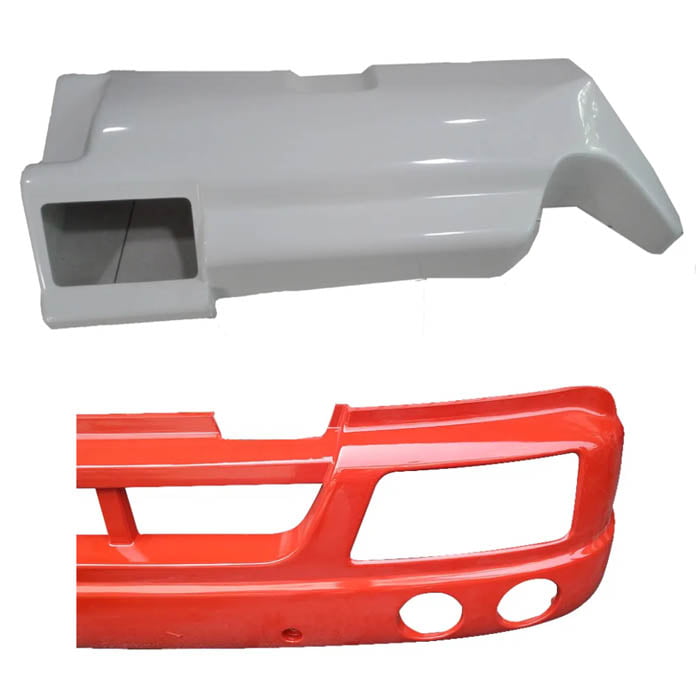
Mold polishing method and working principle
Mold polishing usually uses whetstone strips, wool wheels, sandpaper, etc. to plastically deform the surface of the material and remove the protrusions on the surface of the workpiece to obtain a smooth surface, generally manual operation is the main method. For those with high surface quality requirements, the ultra-fine grinding and polishing method can be used. The ultra-fine grinding and polishing method adopts a special abrasive tool. Polishing can reach a surface roughness of Ra0.008μm
Used tools and specifications for mold polishing
1) The commonly used tools for mold polishing are: sandpaper, whetstone, felt wheel, grinding paste, alloy file, diamond grinding needle, bamboo chip, fiber whetstone, and circular rotary grinding machine.
2) Sandpaper: 150#, 180#, 320#, 400#, 600#, 800#, 1 000#, 1 200#, 1 500#;
3) Whetstone: 120#, 220#, 400#, 600#;
4) Felt wheel: cylindrical, conical, square tip;
5) Grinding paste: 1# (white color) ,3# (yellow color) ,6# (orange color) ,9# (green color) ,15# (blue color) ,25# (brown color) ,35# (red color) ,60# (purple color);
6) File: square, round, flat, triangular and other shapes;
7) Diamond grinding needle: generally 3/32 shank or 1/8 shank, with round wave shape, cylindrical shape, long straight cylindrical shape, long conical shape;
8) Bamboo slices: various shapes are suitable for the operator and the shape of the mold, the function is to press the sandpaper and grind it on the workpiece to achieve the required surface roughness;
9) Fiber whetstone: 200# (black color) ,400# (blue color), 600# (white color) ,800# (red color)
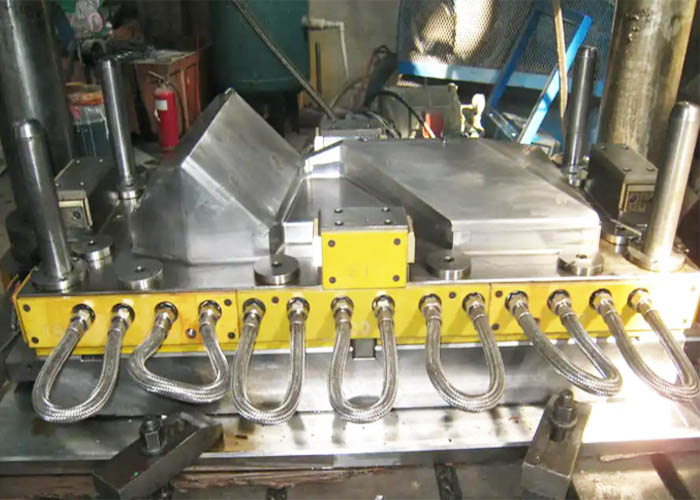
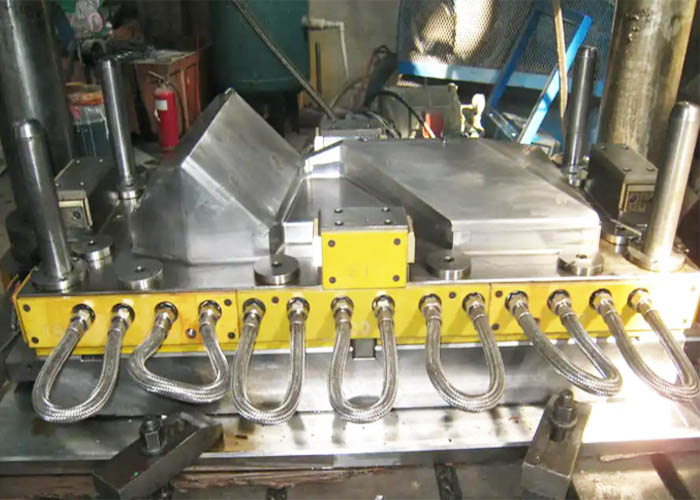
Polishing process
(1) Rough throw
The surface after finishing milling, EDM, grinding and other processes can be polished by a rotating surface polishing machine with a speed of 35000-40000 r/min. Then there is manual whetstone grinding, strip whetstone with kerosene as a lubricant or coolant. The order of use is 180#→240#→320#→400#→600#→800#→1000#.
(2) Semi-fine polishing
Semi-fine polishing mainly uses sandpaper and kerosene. The numbers of the sandpapers are as follows:
400#→600#→800#→1000#→1200#→1500#. In fact, #1500 sandpaper is only suitable for hardening die steel (above 52HRC), not for pre-hardened steel, because it may cause damage to the surface of pre-hardened steel and cannot achieve the expected polishing effect.
(3) Fine polishing
Fine polishing mainly uses diamond abrasive paste. If a polishing cloth wheel is used for grinding with diamond grinding powder or grinding paste, the usual grinding sequence is 9μm (1800#)→6μm (3000#)→3μm (8000#). 9μm diamond abrasive paste and polishing cloth wheel can be used to remove hair-like scratches left by 1 200# and 1 500# sandpapers. Then polish with sticky felt and diamond abrasive paste, the order is 1μm (14000#)→1/2μm (60 000#)→1/4μm (100000#). After that, it is ground by hand with whetstone, and the strip of whetstone is added with kerosene as a lubricant or coolant. The order of use is 180#→240#→320#→400#→600#→800#→1000#.
Polished work environment
The polishing process should be completed in two separate work sites, namely, the rough grinding process site and the finishing process site are separated, and attention should be paid to cleaning the sand particles remaining on the surface of the workpiece in the previous process.
Generally, after rough polishing from whetstone to 1200# sandpaper, the workpiece needs to be transferred to a clean room for polishing to ensure that no dust particles in the air stick to the surface of the mold. The polishing process with precision requirements of more than 1 μm (including 1 μm) can be carried out in a clean polishing chamber. For more exact polishing, it have to in an clean space, because dust or dandruff and saliva may scrap the high-precision polished surface.
After the polishing process is finished, the surface of the part should be protected from dust. When the polishing process is stopped, all abrasives and lubricants should be carefully removed to keep the surface of the workpiece clean, and then a layer of mold anti-rust coating must be sprayed on the surface of the workpiece.