multi cavity injection mold for battery box part
In today’s rapidly developing new energy field, battery boxes are an indispensable component of electric vehicles and energy storage systems, and innovation in their manufacturing processes is particularly important. Multi-cavity injection mold technology plays an increasingly important role in the production of battery box components with its high efficiency and cost-effectiveness. This article will explore in depth how this technology can meet the high standards of Mexico customers for the manufacturing of battery box components.
Table of Contents
ToggleWhat is multi cavity injection mold
Multi cavity injection molding is an advanced manufacturing technology that allows the production of multiple identical parts in a single injection molding process. This technology significantly improves production efficiency and reduces costs by reducing production time and material waste. For products such as battery boxes that are in high demand and have uniform specifications, multi-cavity injection molds are undoubtedly the ideal choice.
Demand analysis of the Mexico market
As an important member of the North American Free Trade Agreement (NAFTA), Mexico has achieved significant development in the fields of automobile manufacturing and new energy in recent years. As the demand for electric vehicles and sustainable energy solutions grows, so does the demand for high-quality battery box components in the Mexican market. Multi-cavity injection mold technology can meet the needs of this mass production while ensuring product consistency and reliability.
Key elements of Multi cavity mold design
Designing a successful multi-cavity injection mold requires considering several key elements, including:
- Material selection: Select high-strength and chemical-resistant materials suitable for battery box applications.
- Cavity layout: Optimize the distribution of cavities to ensure uniform injection pressure and material flow.
- Cooling system: Design an efficient cooling system to speed up the production cycle while ensuring the dimensional stability of the parts.
- Demolding mechanism: Ensure that the mold has a reliable demolding mechanism to reduce the damage rate during production.
Quality control during production
Quality control is crucial during the production of multi-cavity injection molds. This includes:
- Process monitoring: real-time monitoring of temperature, pressure and time parameters during the injection molding process.
- Automated inspection: using automated visual inspection systems to identify and remove unqualified products.
- Continuous improvement: continuous optimization of the production process through data analysis and feedback loops.
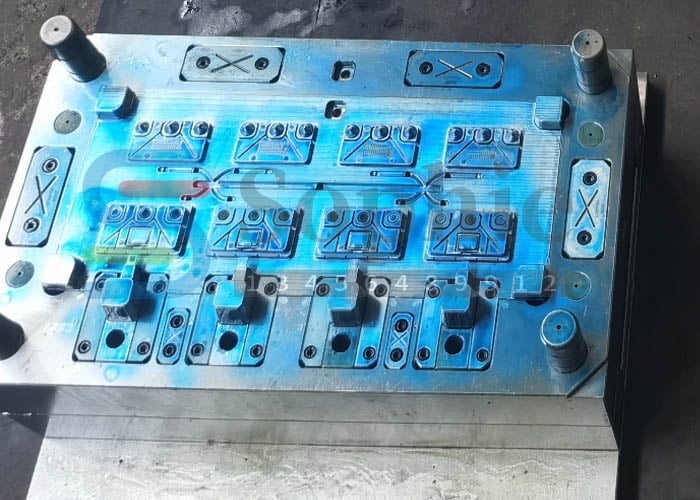
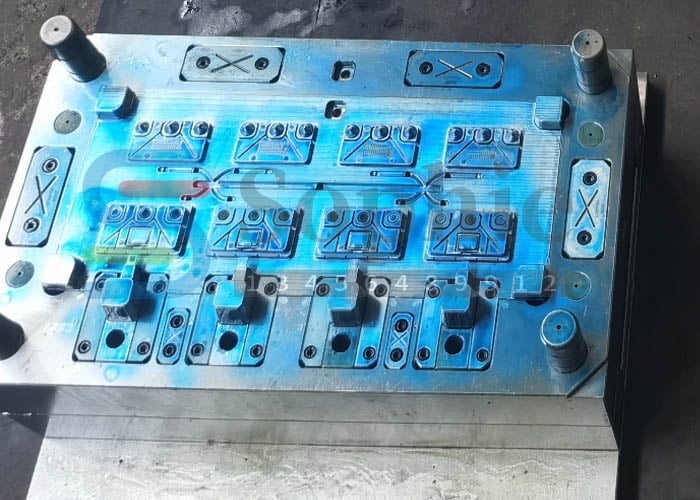
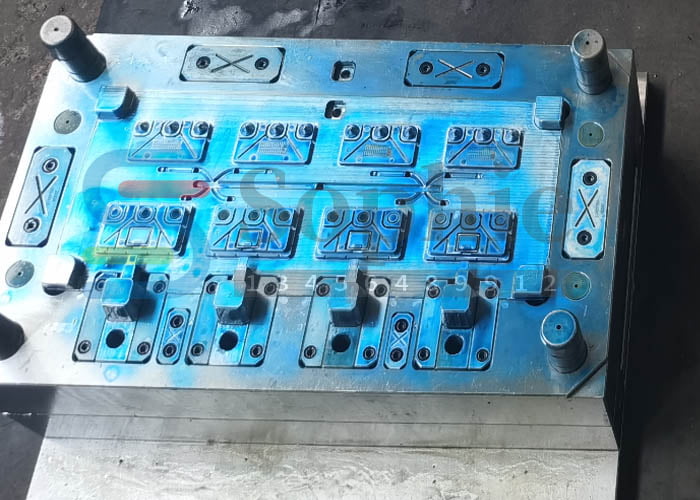
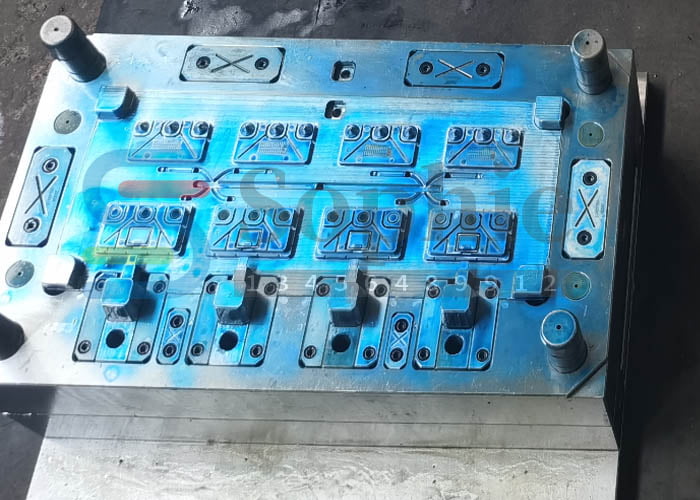
Maintenance and life management of multi cavity injection molds
In order to ensure the long-term stable operation of multi-cavity injection molds, regular maintenance and life management are essential. This includes:
- Preventive maintenance: Regularly check the wear and damage of the molds and make necessary repairs or replacements.
- Cleaning and maintenance: Keep the molds clean to avoid material residues affecting product quality.
- Technology upgrade: With the development of technology, the molds are continuously upgraded to meet new production needs.
Environmental impact and sustainable development
In the production of battery box components, environmental impact and sustainable development are factors that cannot be ignored. Multi-cavity injection mold technology helps to achieve a more environmentally friendly production process by reducing material waste and energy consumption. In addition, the use of recyclable materials and optimized product design are also key to achieving sustainable development.
Future-oriented multi cavity mold technology trends
With the continuous advancement of technology, multi-cavity injection mold technology is also developing. Future molds may integrate more intelligent functions such as self-diagnosis, predictive maintenance, and real-time production adjustments. In addition, the combination of 3D printing and new material technology will further promote the innovation and optimization of mold design.
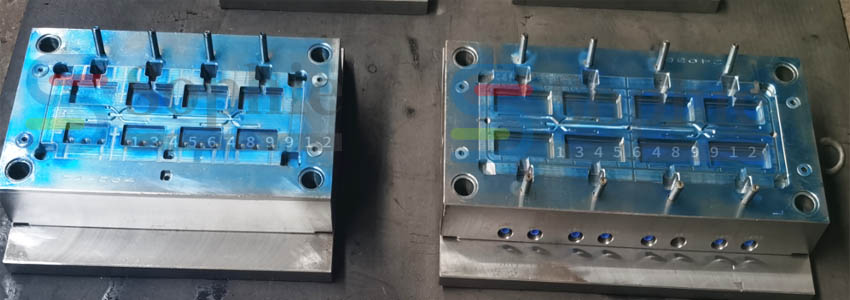
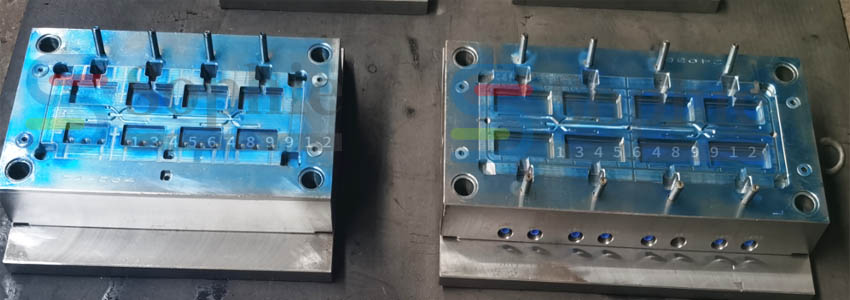
How to improve the manufacturing efficiency and quality of battery box components through multi-cavity injection mold technology
Multi-cavity injection mold technology can improve the manufacturing efficiency and quality of battery box components through the following key aspects:
Improve production efficiency
Multi-cavity molds are capable of manufacturing multiple parts in a single injection molding process, significantly reducing production cycle time and costs. Automated demoulding systems can reduce manual intervention and increase production speed.
Ensure component consistency
Multi-cavity molds ensure that parts in each cavity are produced to strictly the same parameters, ensuring part consistency. By precisely controlling injection molding parameters such as temperature, pressure and speed, the quality of each part can be ensured.
Optimize material usage
Multi-cavity molds reduce material waste because each cavity is filled with exactly the required amount of material. By optimizing mold design, the generation of flash and scrap can be reduced.
Precise cooling system
Multi-cavity molds are usually equipped with precise cooling systems that can cool each cavity evenly, speeding up the solidification process and improving production efficiency. Uniform cooling helps reduce component deformation and internal stress, improving the dimensional stability and mechanical properties of the component.
Quality control and testing
Multi-cavity molds can be integrated with online quality inspection systems to monitor the size and appearance of components in real time to ensure quality. Automated visual inspection systems can quickly identify and reject substandard products.
Design flexibility
Multi-cavity mold design allows flexible adjustment of the number and layout of cavities to accommodate different production needs and product specifications. Mold design can easily adapt to product updates or design changes, reducing the cost of re-moulding.
Through these methods, multi-cavity injection mold technology can not only improve the production efficiency of battery box parts, but also ensure the high quality of parts and meet the growing market demand for high-performance battery boxes.
Multi-cavity injection mold technology provides an efficient, economical and sustainable solution for the manufacture of battery box components. With the continuous demand for new energy and electric vehicles in the Mexican market, this technology will play a more important role in the future. Through continuous technological innovation and quality control, we are confident that we can meet the high standards of our customers and drive the entire industry towards a greener and smarter direction.