In the world of advanced materials and cutting-edge technology, carbon fiber has emerged as a game-changer. Its lightweight, high-strength properties have made it a favorite in industries ranging from aerospace to automotive. But one of the most exciting applications of carbon fiber is in the production of Carbon Fiber Compression Helmet Molds. These compression molding molds are not just a technological marvel; they are revolutionizing the way we think about safety and performance in helmets.
Recently, our company successfully developed and exported a carbon fiber compression molding helmet mold for a Thailand customer. This project not only demonstrated our technical strength in the field of high-end mold manufacturing, but also laid a solid foundation for developing the Southeast Asian market.
We are proud to share that our expertise in this field has recently led to a successful collaboration with a valued client in Thailand. Our Carbon Fiber Compression Helmet Mold has been meticulously designed and manufactured to meet the highest international standards, ensuring that our Thai partners receive a product that excels in both quality and performance.
Table of Contents
ToggleWhat is a Carbon Fiber Compression Helmet Mold?
A Carbon Fiber Compression Helmet Mold is a specialized tool used in the manufacturing process of helmets. It is designed to shape and compress carbon fiber materials into the precise form of a helmet. The mold itself is typically made from high-grade materials that can withstand extreme temperatures and pressures, ensuring that the carbon fiber helmet produced is both durable and lightweight.
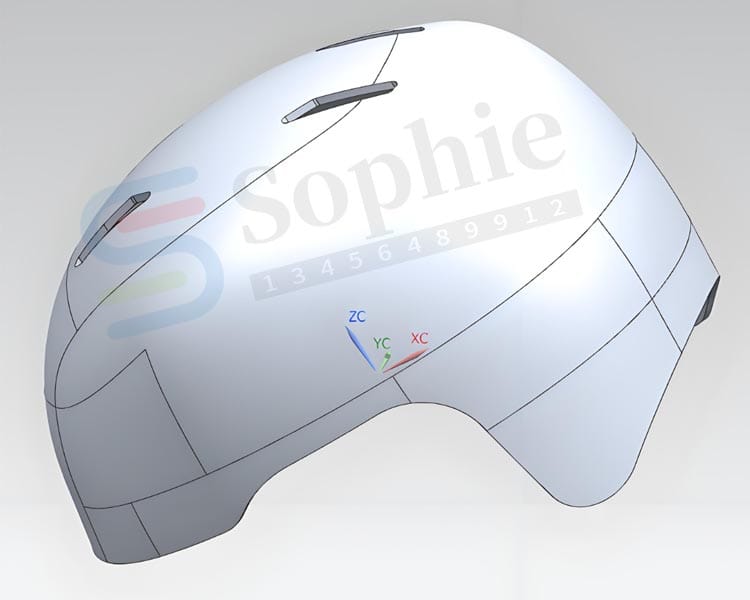
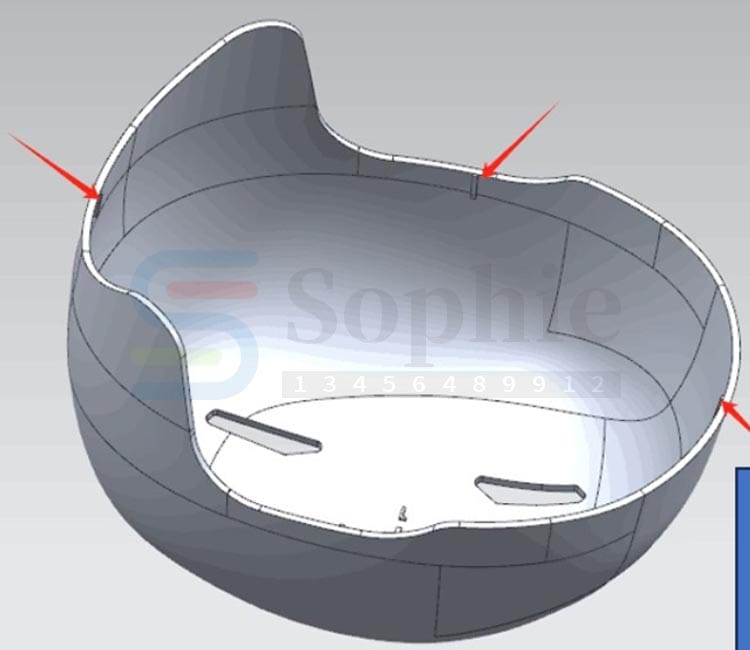
Why Carbon Fiber
Carbon fiber is renowned for its exceptional strength-to-weight ratio. It is five times stronger than steel yet significantly lighter. This makes it an ideal material for helmets, where the primary goals are to protect the wearer without adding unnecessary weight.
- Lightweight: Carbon fiber helmets are much lighter than traditional helmets, reducing fatigue and increasing comfort for the wearer.
- High Strength: Despite their light weight, carbon fiber helmets offer superior protection against impacts.
- Durability: Carbon fiber is highly resistant to corrosion, UV rays, and other environmental factors, ensuring a longer lifespan for the helmet.
The Manufacturing Process of Carbon Fiber Compression Helmet Mold
The process of creating a carbon fiber helmet using a Carbon Fiber Compression Helmet Mold involves several precise steps:
- Design and Engineering: The first step is to design the helmet using advanced CAD software. This design is then used to create the mold.
- Mold Creation: The mold is crafted from high-grade materials, often using CNC machining to ensure precision.
- Layering: Sheets of carbon fiber are layered into the mold. Each layer is carefully positioned to ensure optimal strength and weight distribution.
- Compression: The mold is then subjected to high pressure and temperature in a process known as compression molding. This compresses the carbon fiber layers, bonding them together to form a solid, durable helmet.
- Curing: The helmet is cured in an oven, further strengthening the carbon fiber.
- Finishing: The final step involves trimming, sanding, and applying any necessary coatings or finishes.
Applications of Carbon Fiber Helmets
Carbon fiber helmets are used in a variety of high-performance and safety-critical applications:
- Motorcycle Helmets: Offering superior protection and comfort for riders.
- Cycling Helmets: Lightweight and aerodynamic, perfect for competitive cyclists.
- Military and Tactical Helmets: Providing maximum protection without the burden of heavy weight.
- Sports Helmets: Used in sports like skiing, snowboarding, and rock climbing where safety and performance are paramount.
Benefits of Using Carbon Fiber Compression Helmet Molds
Precision and Consistency: The molds ensure that each helmet is produced with exacting precision, maintaining consistent quality across all units.
Efficiency: Compression molding is a highly efficient process, allowing for the rapid production of helmets without compromising on quality.
Customization: The molds can be customized to produce helmets of various shapes, sizes, and designs, catering to specific needs and preferences.
Cost-Effectiveness: While the initial investment in carbon fiber molds can be high, the long-term benefits in terms of durability and performance make it a cost-effective solution.
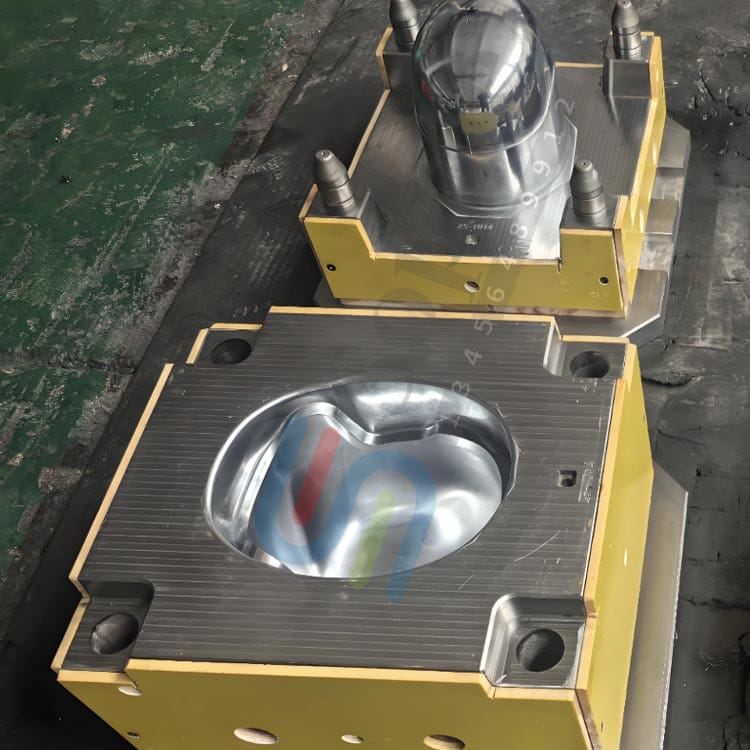
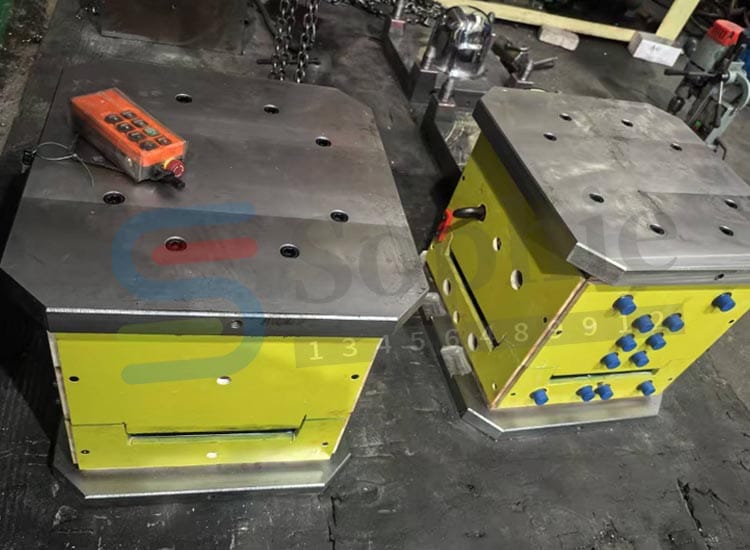
The Future of Carbon Fiber Helmets
As technology continues to advance, we can expect to see even more innovations in the field of carbon fiber helmets. From enhanced safety features to more sustainable manufacturing processes, the future looks bright for this incredible material.
In conclusion, the Carbon Fiber Compression Helmet Mold is a cornerstone of modern helmet manufacturing. It combines the unparalleled properties of carbon fiber with advanced molding techniques to produce helmets that are not only safer but also more comfortable and efficient. Whether you’re a professional athlete, a motorcycle enthusiast, or someone who values top-tier safety, carbon fiber helmets are the way of the future.
By investing in a Carbon Fiber Compression Helmet Mold, manufacturers can ensure they are at the forefront of this exciting industry, delivering products that meet the highest standards of quality and performance. So, if you’re looking to stay ahead of the curve, now is the time to embrace the power of carbon fiber.
Our recent export of the Carbon Fiber Compression Helmet Mold to our esteemed client in Thailand is a testament to our commitment to excellence and innovation. We look forward to continuing our partnership and exploring new opportunities to bring cutting-edge solutions to the global market.
The successful export of carbon fiber compression molding helmet molds is not only a victory for us in the field of high-end mold manufacturing, but also an important step for us to enter the international market. We look forward to cooperating with more international customers to jointly promote the development of carbon fiber composite material technology.