Impact of temperature on injection molds: key factors and optimization solutions
In the injection molding process, temperature is one of the core parameters that affect product quality, mold life and production efficiency. Whether it is mold temperature, melt temperature or cooling temperature, slight changes may lead to product defects, dimensional instability and even mold damage. This article will deeply explore the various effects of temperature on injection molds and provide practical optimization suggestions.
Table of Contents
ToggleEffect of temperature on injection molding quality
Plastic product surface quality
Mold temperature is too low: it may cause poor melt fluidity, flow marks, weld marks or uneven gloss on the product surface.
Mold temperature is too high: it is easy to cause shrinkage marks and bubbles on the product surface, and even warping and deformation due to uneven cooling.
Dimensional accuracy
Temperature fluctuations will affect the shrinkage rate of plastics. For example, if the mold temperature is too high, the product may shrink too much after demolding and the size may be out of tolerance.
high-precision injection molding, especially for precision parts such as electronic accessories and medical devices.
Internal structural strength
Appropriate mold temperature can promote the orderly arrangement of molecular chains and improve the mechanical strength and fatigue resistance of the product.
Uneven temperature may lead to internal stress concentration, making the product prone to cracking or deformation in later use.
Mold temperature affects the formation of molding internal stress. If the mold temperature is too low, the molten resin will cool rapidly, resulting in higher residual internal stress in the molded product. When the residual internal stress is higher than the elastic limit of the resin or under certain chemical environment erosion, cracks will appear on the surface of the plastic part.
Warping
If the cooling system of the mold is not designed properly or the mold temperature is not properly controlled, the plastic part will not be cooled enough, which will cause the plastic part to warp and deform. For plastic parts with completely symmetrical shapes and structures, the mold temperature should be kept consistent so that all parts of the plastic part are cooled evenly.
Shrinkage
Low mold temperature accelerates the “freezing orientation” of molecules, increases the thickness of the frozen layer of the melt in the mold cavity, and hinders crystal growth, reducing the molding shrinkage of the product. On the contrary, high mold temperature, slow melt cooling, long relaxation time, low orientation level, and conducive to crystallization, the actual shrinkage of the product is large.
Heat deformation temperature
For crystalline plastics, if the product is molded at a lower mold temperature, the orientation and crystallization of the molecules are instantly frozen. When in a higher temperature environment or secondary processing conditions, the molecular chains will be partially rearranged and crystallized, causing the product to deform at a temperature far lower than the thermal deformation temperature of the material. The correct approach is to use a mold temperature close to its crystallization temperature to produce the product so that it can be fully crystallized during the injection molding stage to avoid such post-crystallization and post-shrinkage.

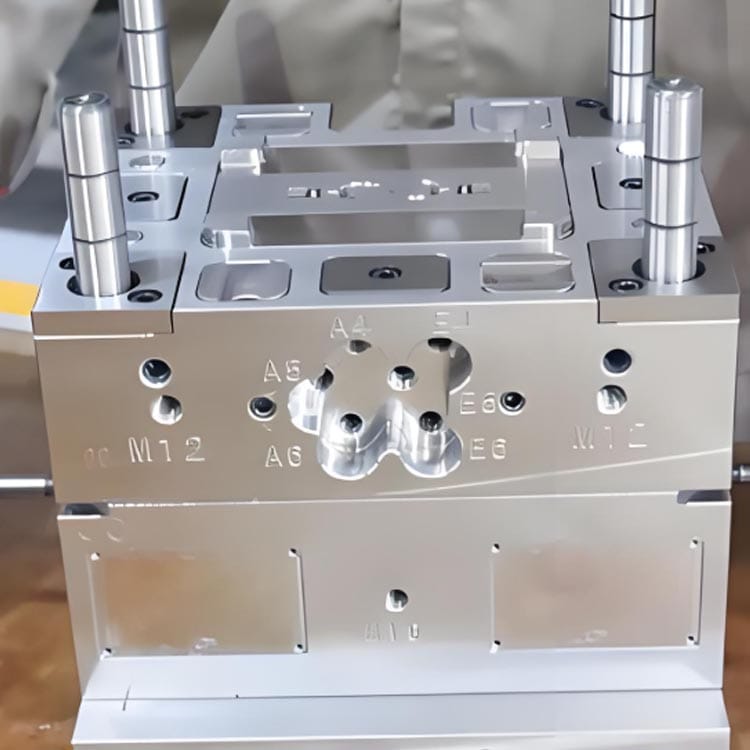
Effect of temperature on mold life
Mold life: Too high mold temperature may cause thermal fatigue and wear of the mold, thus shortening the service life of the mold. At the same time, the viscosity of the plastic decreases at high temperatures, making it easier to adhere to the surface of the mold cavity, increasing the difficulty and workload of cleaning the mold. If the mold temperature is too low, condensation may occur between the plastic and the mold surface, resulting in appearance problems such as water marks and poor gloss on the surface of the product.
Mold maintenance: Fluctuations in mold temperature will affect mold maintenance. Too high or too low temperatures may cause some abnormal conditions in the mold, such as mold deformation caused by thermal expansion or contraction, poor sealing, etc., increasing the difficulty and cost of mold maintenance.
Cooling system efficiency: Too high cooling water temperature or insufficient flow will prolong the molding cycle and increase the heat load on the mold. Optimizing the cooling channel design (such as conformal cooling) can balance the mold temperature and extend the mold life.
Effect of temperature on production efficiency
Molding cycle: The higher the mold temperature, the longer the cooling time usually needs to be, which may reduce production efficiency.
Energy cost: Precise temperature control (such as using a mold temperature controller) can reduce ineffective heating/cooling and reduce energy consumption
Impact on injection molding process
Plastic flow and molding: The temperature of the mold directly affects the flow behavior of the plastic. In a high-temperature mold, the viscosity of the plastic decreases, the fluidity increases, and it is easy to fill the mold cavity, but too high a temperature may cause the plastic to melt and flow too quickly, causing excessive internal stress or flow marks in the part, or even thermal degradation. In a low-temperature mold, the plastic has poor fluidity, which may lead to insufficient filling or rough surface of the part.
Part cooling and shrinkage: The mold temperature determines the cooling rate and shrinkage rate of the plastic in the mold cavity. Cooling too fast may cause greater internal stress inside the part, resulting in warping, cracking and other problems; cooling too slowly may cause deformation of the part or excessive internal stress.
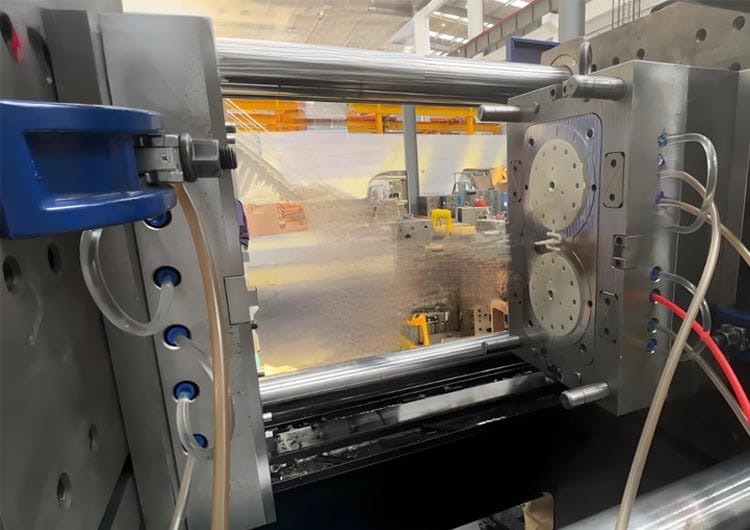
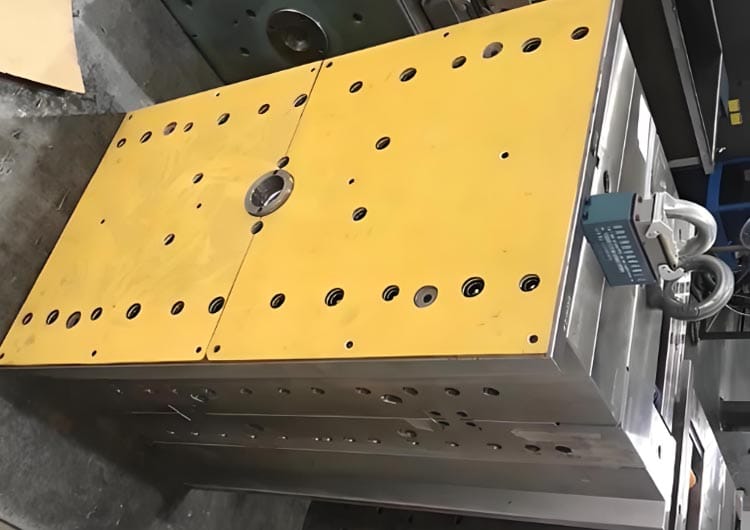
Temperature control optimization solution
- Segmented temperature control technology: Set different temperatures for different areas of the mold (such as core and cavity) according to the product structure to reduce thermal deformation.
- Dynamic temperature regulation: Increase the mold temperature during the filling stage to improve fluidity, and reduce the mold temperature during the pressure holding stage to shorten the cycle.
- Advanced cooling design: Use beryllium copper inserts or 3D printed conformal cooling channels to improve heat dissipation uniformity.
- Intelligent monitoring: Monitor the mold temperature in real time through sensors, and automatically adjust the process parameters in combination with the MES system
Industry application cases
Auto parts: High mold temperature (80-120°C) ensures the fluidity of PA/GF materials and reduces warping caused by glass fiber orientation.
Optical lenses: Constant temperature within ±0.5°C to avoid weld marks affecting light transmittance.
Temperature control is the “invisible hand” in the injection molding process, directly affecting cost, quality and delivery capabilities. Choosing reasonable mold temperature settings, maintaining cooling system stability, and optimizing the process with digital tools can significantly improve competitiveness.
Does your injection molding project require a more professional temperature management solution? Welcome to contact our engineering team!