China as the world’s largest automotive lamp production and sales market,why the car lamp mold will failure? Car Lamp mold manufacturers and lamp manufacturers are well aware of the production process and injection molding process of lamp molds, but they are not very familiar with the main failure modes and causes of lamp molds. Explanation is made as follows.
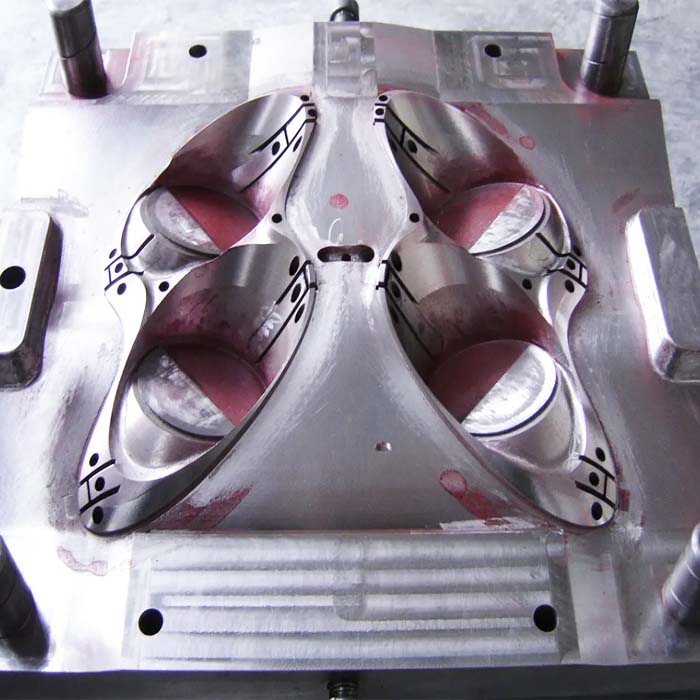
Why the lamp mold will failure
There are many varieties and specifications of car lamp molds, complex shapes, and large drop. The requirements for the surface of the cavity are high, and the manufacturing is difficult. Therefore, a comprehensive analysis of various factors is required before material selection, as shown in the figure below: We think the factors that need to be considered include or aatters needing attention in the selection of lamp mold steel:
Table of Contents
TogglePoor polishing of car lamp mold
The surface of the lamp mold is usually required to obtain the mirror polishing effect of DIN/ISO 1302 N1/SPI A1 level or above. The quality of the mirror polishing not only tests the quality of the mold material, but also tests the polisher’s carefulness and patience. In order to obtain a satisfactory polishing effect, the mold maker can be said to have worked hard, but sometimes it is half the effort, or even lost, and has to make a new set of molds. The material determines the degree of mirror finish. Selecting mold steel with excellent mirror polishing properties for high-demand plastic car lamp molds is the first step for successful polishing. There are often unevenness in ordinary 2738 or China-made age-hardening steel similar to NAK XX type. The distributed hard non-metallic inclusions (such as Al2O3, etc.) and the aggregated and distributed primary carbides in ordinary SUS420J2 steel are very easy to form pinpoint polishing defects during the polishing process. Moreover, the band-like segregation in the 2738 steel will cause uneven microhardness of the steel matrix, and it is easy to form a wrinkled and orange peel-like surface during polishing, and it is difficult to obtain a higher flatness. Therefore, the lamp mold material must have high purity, uniform and dense microstructure and uniform microhardness in order to achieve excellent mirror finish. Professional special steel mills usually use the ESR (electroslag remelting) method to refine high-quality die steel that meets the requirements of high surface polishing. grains, eliminating the holes of the original ingot and improving the density.
Early cracking of car lamp mold
Cracking will make the mold unusable, which is often a catastrophic loss to the mold factory. The possible internal cause of cracking is improper material selection, the selection of mold materials with low toughness leads to insufficient crack resistance of the mold, and the stress in the mold exceeds the mold steel. due to tensile strength. Lamp mold materials must have very good toughness and organizational uniformity.
The external reasons for cracking include: unreasonable design, unreasonable manufacturing process, improper use and operation and improper maintenance (such as welding repair) and so on.
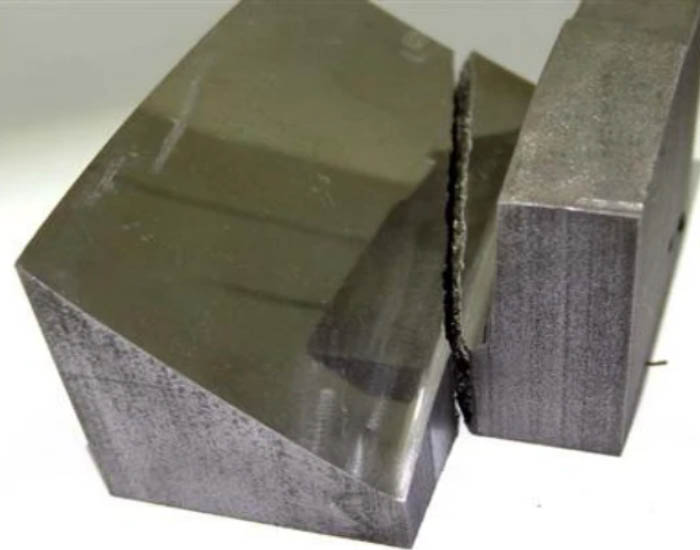
Unreasonable design
The structure of the lamp mold is complex, the drop is large, there are often gaps on the mold parts, the design sharp corners and sharp edges and corners of the R position, abnormal protrusions, and due to the strict requirements of the molding cycle, the distance from the cooling water channel to the molding surface is often small, these factors Often easy to become the incentive for early cracking. The picture on the right shows a case where too small R angle causes the stress concentration of the plastic mold, which causes the mold to crack during the mold test under the action of external stress.
The manufacturing process is unreasonable
The molding process of the lamp mold often goes through manufacturing processes such as machining, heat treatment, electrical discharge machining, and assembly. If the heat treatment process specification is not properly formulated, and electric discharge machining is performed with a large current after heat treatment, and the mold is tested or used without stress relief treatment and without removing the EDM deterioration layer after EDM, these machining processes remaining on the mold. A variety of surface defects are formed in the process, which often become the source of early cracking.
Improper use and operation and improper maintenance
The inspection, maintenance and replacement of molds and accessories are not timely or the correct welding and prognostic heat treatment process is not adopted, resulting in welding stress and welding defects, which will also become the cause of early cracking of plastic molds.