The Essential Guide to Injection Molding Defects
Plastic injection moulds often have some problems. Today, the editor will explain the 9 Common Plastic Injection Molding Mold Defects as follows:
Table of Contents
Toggle1. Plastic Injection Molding Mold of Gate stripping is difficult
During the injection molding process, the gate sticks to the gate sleeve and is not easy to come out. When the mold is opened, the finished product exhibits crack damage. In addition, the operator must knock out the top of the copper rod from the nozzle to loosen it before demoulding, which seriously affects the production efficiency.
The main factor of this disadvantage is the poor brightness of the gate cone hole and the knife marks in the circumferential direction of the inner hole. Another, the material is very soft and the small end of taper hole is deformed or damaged after a period of use, and the spherical arc of nozzle is too small, causing the gate material to have a rivet head here. The taper hole of the sprue sleeve is difficult to process, and standard parts should be used as much as possible. If you need to process it yourself, you should also restrain yourself or buy a special reamer. The taper hole needs to be ground to above Ra0.4. In addition, it is necessary to set gate pull rod or gate ejector.
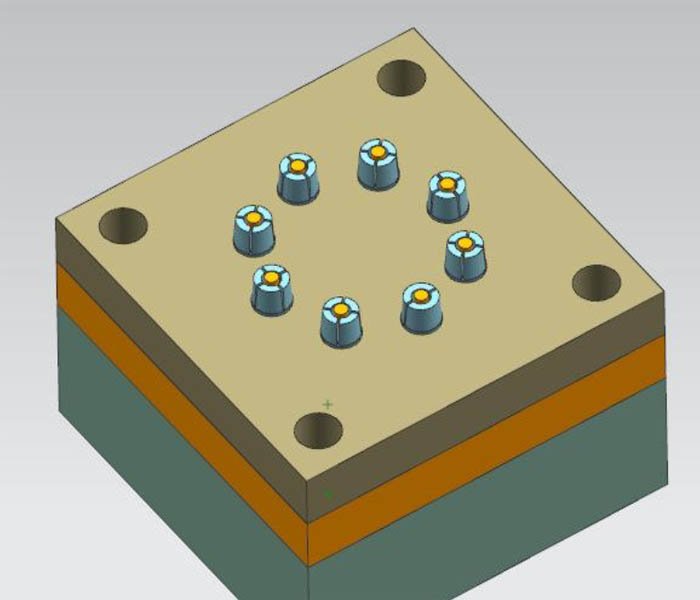
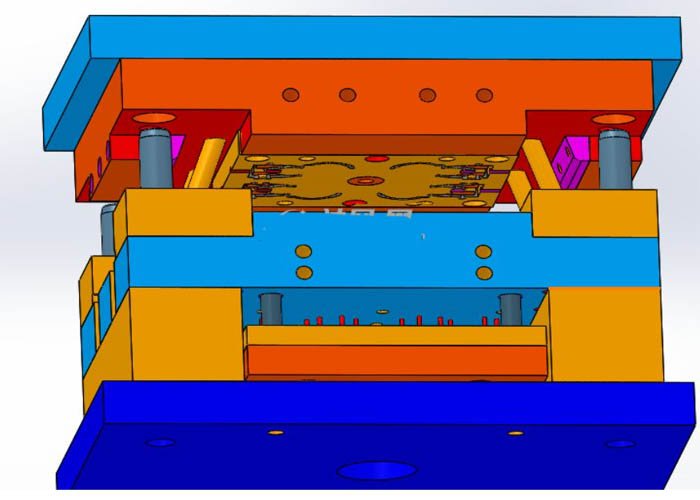
9 Common Plastic Injection Molding Defects
2. Moving and fixed mold offset
Due to the different filling rates of the large molds and the influence of the self-weight of the mold when the mold is loaded, the moving and fixed molds are offset. In the above cases, the lateral deflection force will be applied to the guide post during injection, and the surface of the guide post will be rough and damaged when the mold is opened.
In order to solve the above questions, it can added a high-strength positioning key on each of four sides of mold parting surface. The most concise and useful is to use a cylindrical key. The straightness of the guide hole and the parting surface is very important. During processing, the movable and fixed dies are used to align and clamp, and then the boring machine is finished at one time. Minimize straightness errors. In addition, the heat treatment hardness of the guide post and guide bush must meet the requirements of the plan.
3. Guide post damage
The guide rod mainly plays a guiding role in the mold,it can ensure the core and the cavity of molding surfaces don’t touch each other under any circumstances,the guide rod cannot be used as a positioning part.
In several cases, infinite lateral deflection forces will occur during the injection of the moving and stationary molds. When the wall thickness of the plastic part is not uniform, the flow rate of the material passing through the thick wall is large, and a large pressure occurs here; The back pressures are not equal.
4. Moving template twists and turns
When the mold is injected, the molten plastic in the mold cavity has an infinite back pressure, usually 600~1000 kg/cm. Mold makers sometimes do not pay attention to this question, usually change the original plan standard, or replace the moving template with low-strength steel plate. In the mold with ejector ejector, due to the large span between the two sides, the template bends down during injection.
Therefore, it is necessary to choose high-quality steel for the moving formwork, and it must meet the thickness. Low-strength A3 steel plate is not allowed to use. When necessary, a support column or a support block should be set under the moving formwork to reduce the thickness of the formwork and adjust the forward bearing capacity.
5. The ejector is bent, cracked or leaked
The quality of the ejector rod is better, but the processing cost is too high. Nowadays, standard parts are usually used, and the quality is lower. If the gap between the ejector pin and the hole is too large, there will be leakage, but if the gap is too small, the ejector pin will swell due to the increase in mold temperature during injection, and it will be stuck.
What’s more risky is that sometimes the ejector pin is pushed out of the normal interval, and the ejector pin does not move and breaks. When the mold is clamped once, the exposed ejector pin cannot be reset and the die is damaged. In order to solve this problem, the ejector rod was reground from scratch, and a 10-15mm cooperating section was kept at the front end of the ejector rod, and the base was slightly ground by 0.2 mm. After all ejector rods are installed, it is necessary to strictly check the cooperation gap, usually within 0.05~0.08 mm, to ensure that all ejector arrangements can advance and retreat freely.
6. Poor cooling or water leakage
Magnetic grinding and polishing is to use magnetic abrasives to form abrasive brushes under the action of a magnetic field to grind workpieces. This method has high processing efficiency and nice quality,processing conditions is easy to control and good working conditions.. If use a suitable abrasives, the roughness of surface can reach Ra0.1μm.
The cooling effect of the mold directly affects the quality and production efficiency of the finished product, such as poor cooling, large shortening of the finished product, or uneven shortening and warping deformation. On the other hand, the whole of the mold may be overheated, so that the mold cannot be formed normally and production is stopped.
The solution of the cooling system, the processing depends on the shape of the product, do not omit this system due to the complicated structure of the mold or difficult processing, especially for large and medium model molds, the cooling issues have to fully considered.
7. The slider is tilted and reset is not good
Some moulds due to the area of the template was bounded,and the length of guide groove will be small. When the mold is pressed, the reset of the slider is not smooth, so that the slider is damaged or even damaged by bending. According to experience, after the slider finishes the core-pulling action, the length left in the chute should not be less than 2/3 of the total length of the guide groove.
8. The distance tensioning arrangement fails
Fixed-distance tensioning devices such as swing hooks and hasps are usually used in fixed mold core pulling or some secondary demolding molds. Because such devices are arranged in pairs on both sides of the mold, their action requirements must be synchronized. , that is, the mold is clamped together, and the mold is opened to a certain position and unhooked together.
Once the synchronization is lost, the template of the drawn mold must be tilted and damaged. The parts of these structures must have high rigidity and wear resistance, and the adjustment is also very difficult. The life of the structure is short. arrange.
In the case where the core pulling force is relatively small, the method of pushing out the fixed mold with a tension spring can be used. When the core pulling force is relatively large, the core sliding when the moving mold is withdrawn can be used. Hydraulic cylinders can be used for core pulling on large molds. The inclined pin slider core pulling arrangement is damaged.
The most common shortcomings of this arrangement are that the processing is not in place and the materials used are too small. There has two mainly questions as follows:
The inclined pin inclination angle A is large, and the advantage is that a large core pulling distance can be produced in a short mold opening stroke. However, if the inclination angle A is too large, when the pulling force F is a certain value, the bending force P=F/COSA on the inclined pin during the core-pulling process is also larger, and the inclined pin is easily deformed and the inclined hole is worn.
Meanwhile,the upward thrust of the oblique pin on the slider, N=FTGA, is also greater. This force increases the positive pressure of the slider on the guide surface in the guide groove, and then increases the friction resistance when the slider slides. It will cause uneven sliding and guide groove was weared. The inclination angle A shouldn’t be greater than 25 based on experience.
9. Poor exhaust in the injection mold
There is often gas in the injection mold. What is the reason for this?
There is air in the casting system and the mold cavity; some materials are rich in moisture that has not been removed by drying, and they will gasify into water vapor at high temperatures; due to the high temperature during injection molding, some unstable plastics will occur. Gases are generated by decomposition; some additives in plastic materials can evaporate or chemically react with each other to generate gases.
At the same time, the cause of the poor exhaust gas also needs to be found out as soon as possible. The poor exhaust of the injection mold will bring a series of damage to the quality of the plastic parts and many other aspects. The main manifestation is that the melt will replace the gas in the cavity during the injection molding process. If the gas is not discharged in time, the melt will be formed. Filling is difficult, resulting in insufficient injection volume and unable to fill the cavity; the air that is not cleaned smoothly will form a high pressure in the cavity, and enter the interior of the plastic under a certain degree of compression, forming voids, pores, sparse arrangements and silver streaks, etc. quality defects;
Because the gas is highly compressed, the temperature in the cavity rises sharply, which in turn causes the surrounding melt to decompose and bake, causing the plastic parts to appear somewhat carbonized and scorched. It mainly appears at the confluence of the two melts, at the gate flange; the gas is not swept away smoothly, so that the melt speeds entering each cavity are different, so it is easy to form movement marks and fusion marks, and make the plastic parts The mechanical function is reduced; due to the obstruction of the gas in the cavity, the filling speed will be reduced, the molding cycle will be affected, and the tax efficiency will be reduced.
The distribution of air bubbles in the plastic parts, the air bubbles generated by the accumulated air in the mold cavity, are often distributed on the part opposite to the gate; the air bubbles generated by the differentiation or chemical reaction in the plastic material are distributed along the thickness of the plastic part; in the plastic material The bubbles generated by the vaporization of the remaining water are scattered irregularly on all the plastic parts.