Battery Terminal Cover mold Multi Cavity injection Cover Mould
In the world of manufacturing, precision and quality are paramount, especially when it comes to components as critical as battery terminal covers. As we embark on the journey of producing and exporting these Battery Terminal Cover mold multi cavity Cover Mould to Mexico, it’s essential to delve into the intricacies of the process to ensure a seamless and successful operation. Let’s explore the key aspects that make this mold production a standout in the battery box mold industry.
Table of Contents
ToggleBattery Terminal Cover mold detailed
- Battery Terminal Cover mold Plastic Injection Cover Mould
- Mold cavity:12 Cavities
- Mold Runner: Cold Runner
- Battery Terminal Cover mold cavity steel: H13
- Battery Terminal Cover mold core steel: H13
- Plastic material: PP
- Mold Cycle time:30-35 Secs
- Delivery time:40-45 days.
Battery Terminal Cover mold Design is Precision at the Core
The design of the Battery Terminal Cover mold is where art meets science. It’s crucial to consider the covert’s structure, dimensional precision, surface finish, and volume when designing the mold. Our team of engineers ensures that the battery terminal cover mold Plastic Injection Cover Mould is designed to accommodate precise terminal contact points, ensuring optimal electrical performance. This attention to detail is what sets our molds apart in the competitive landscape.
A well-structured Battery Plastic Terminal Cover mold is the backbone of efficient production. We focus on the design of parting lines, cavity layout, gating systems, venting structures, and ejection mechanisms. These elements are crucial for ensuring product quality and production efficiency. Our ejection system design ensures that the product is smoothly removed from the Terminal Cover mold without causing damage to either the product or the mold.
Mold Material Selection is Durability in Focus
The choice of Battery Terminal Cover mold Plastic Injection Cover Mould material is critical for the longevity and quality of the molded parts. We select materials that can withstand high pressure and temperature, while also being resistant to corrosion and wear. Common mold steels like P20 and H13 are used for their superior properties, ensuring our molds can withstand the rigors of continuous production,for this Multi Cavity Terminal Cover mold,we used H13 mold steel made it
Surface Treatment to Enhancing Performance
Surface treatment of the Plastic Injection Battery Terminal Cover mold is essential for improving the surface quality of the cover and reducing wear and adhesion. Techniques such as electroplating or coating are used to enhance the mold’s corrosion and wear resistance, thereby extending its service life.
Temperature Control Systems
Temperature control plays a pivotal role in the plastic injection molding process. Our Battery Terminal Cover mould are equipped with an effective cooling system to regulate the temperature of the plastic, ensuring the quality and efficiency of the production. The cooling water channels are designed to ensure uniform cooling across the cover mold, preventing product deformation or internal stress.
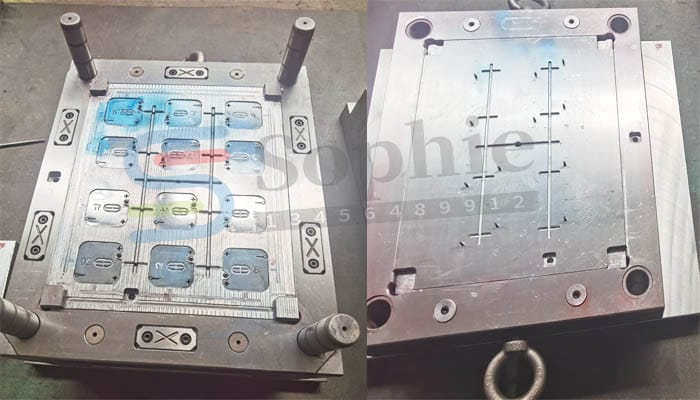
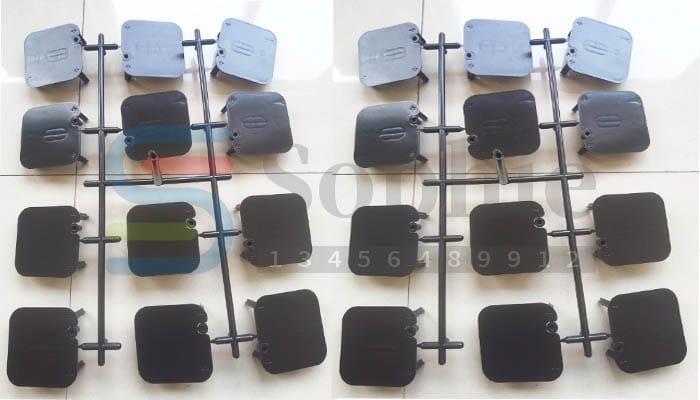
Production Considerations
During production injection Terminal Cover mould,It needs to monitor key parameters such as injection pressure, temperature, and time to ensure product consistency and quality.
By focusing on these critical aspects, we can ensure that the production of battery terminal cover molds not only meets technical requirements but also satisfies the demands of the Mexican market. This commitment to excellence enhances our product’s market competitiveness and ensures customer satisfaction.
As we continue to innovate and refine our processes, our Multi Cavity battery terminal cover molds stand as a testament to our dedication to quality and precision. We look forward to serving the Mexican market with the same level of excellence we bring to all our endeavors.
This blog post aims to provide an in-depth look at the production of battery terminal cover molds, highlighting the importance of each step in the process. By adhering to these best practices, we can ensure that our products meet the highest standards and exceed customer expectations.