Family Mold Injection Molding: A Comprehensive Guide
Family Molding Molds & Parts
Save on molds and costs
High production capacity
Welcome to our detailed guide on family mold injection molding, a versatile and cost-effective manufacturing process. This page aims to provide a thorough understanding of family mold injection molding, including its definition, benefits, applications, and considerations for implementation.
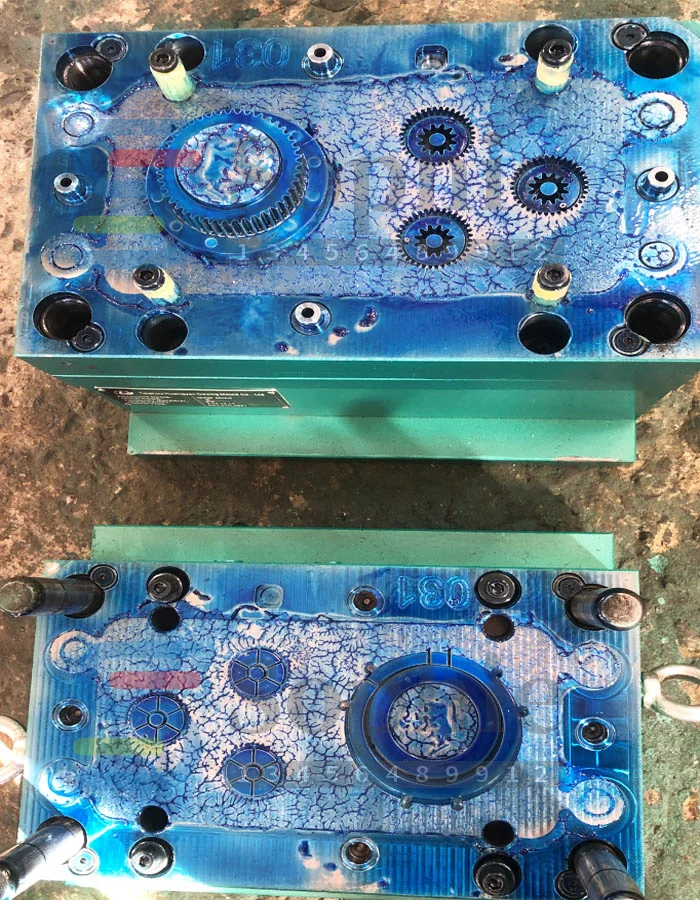
What is Family Mold Injection Molding
Family Mold Injection Molding is a specialized technique in the injection molding process that enables the production of multiple different parts within a single mold setup. This method stands out for its efficiency and cost-effectiveness, particularly when manufacturing a set of related parts that are used together or share similar characteristics.
The process involves creating various cavities within one mold, each designed to produce a distinct component during the same injection cycle. This results in reduced tooling expenses and streamlined production, as well as increased opportunities for design flexibility 。Family molds are especially beneficial for small to medium production runs and are widely used in industries such as automotive, medical devices, consumer electronics, packaging, and aerospace.
However, there are certain considerations and limitations to using family molds. For instance, all parts produced in the same family mold must be made from the same material and color, and the number of cavities for each part must match the quantity needed for the final product assembly 。Additionally, the parts should have similar shapes, sizes, and wall thicknesses to ensure uniform quality and prevent potential issues related to injection molding conditions.
Despite these considerations, family mold injection molding offers a multitude of benefits, including cost savings, increased productivity, time efficiency, consistent quality, design flexibility, reduced material waste, and streamlined assembly processes 。Manufacturers can optimize the performance and longevity of family molds through careful planning, adherence to best practices, and by leveraging the expertise of experienced mold designers and engineers.
Family Mold Injection Molding Key Features
Family Mold Injection Molding is a sophisticated and adaptable manufacturing process that offers a range of key features, making it an excellent choice for a variety of production needs.
Simultaneous Production of Various Parts
Family molds allow for the concurrent creation of multiple components within a single operation. This not only speeds up the production process but also ensures that all parts are manufactured under the same conditions, which can lead to better consistency in quality.
Cost Savings on Tooling and Production
- Reduced Tooling Costs: By consolidating the production of different parts into one mold, the need for multiple individual molds is eliminated, which can significantly reduce the initial investment in tooling.
- Decreased Material Usage: Family molds can optimize material flow and reduce waste by sharing common runners and gates, leading to a more efficient use of raw materials.
- Lower Labor and Maintenance Costs: Streamlined production reduces the labor required for mold changes and the maintenance associated with multiple molds.
Ideal for Small to Medium Production Volumes
- Flexibility in Production Runs: Family molds are well-suited for production runs that do not require the economies of scale associated with large volume manufacturing. They offer a cost-effective solution for producing a variety of parts in smaller quantities.
- Rapid Prototyping and Iteration: For companies that need to quickly prototype and iterate on designs, family molds can accelerate the process by allowing multiple versions of parts to be tested in a single setup.
Design Flexibility
Family molds support the creation of a diverse range of parts within a single design framework, accommodating complex geometries and intricate features that might be challenging to produce with individual molds.
Quality Consistency
Producing parts simultaneously in the same mold helps maintain uniformity in dimensions and properties, which is crucial for parts that need to fit together precisely in the final assembly.
Shorter Lead Times
The streamlined process of family mold injection molding can shorten the time from design to finished product, allowing for faster market response and reduced time to market.
Simplified Assembly Processes
With multiple components produced in one go, the assembly process is simplified, which can lead to further cost savings and improved efficiency in the final product construction.
Customization and Personalization
Family molds can be tailored to include specific features or variations for different parts, enabling a high degree of customization and personalization in the final products.
Adaptability to Material Changes
Should there be a need to change materials during production, family molds can often accommodate such changes more readily than single-cavity molds, providing additional flexibility.

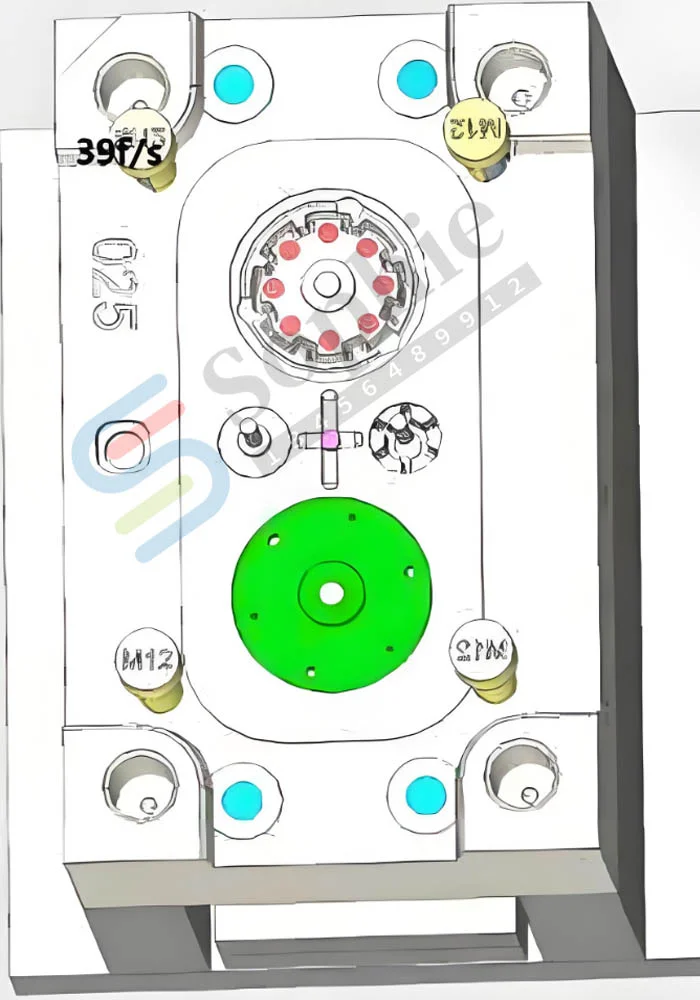
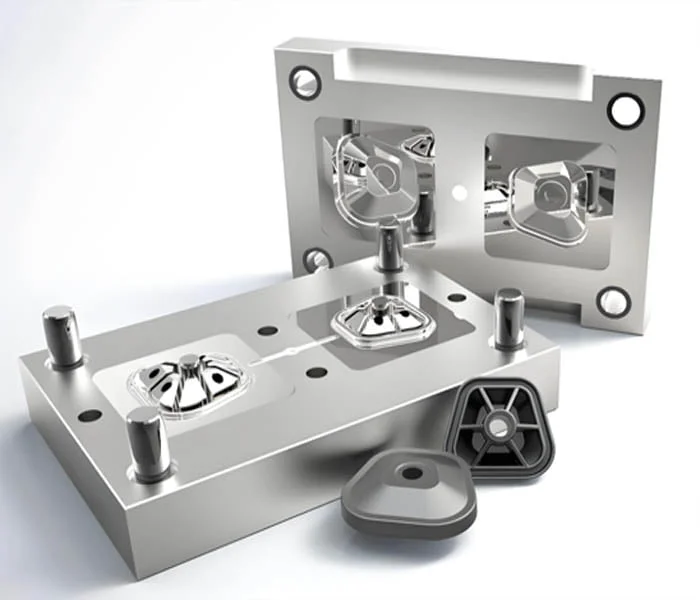

Considerations for Family Mold Injection Molding
Family Mold Injection Molding is a specialized technique in the injection molding process that enables the production of multiple different parts within a single mold setup. This method stands out for its
Material and Color Consistency
All components within a family mold must be made from the same material and color to ensure uniformity.
Cavity Balance
The design must ensure that the cavities are balanced to avoid uneven pressure distribution and potential mold damage.
Wall Thickness Uniformity
Components should have similar wall thicknesses to maintain consistent cooling rates and prevent warping.
Mold Maintenance
Family molds require regular maintenance to ensure longevity and consistent part quality.
Production Planning
Careful planning is necessary to match the production ratios of different components to the final assembly requirements.
Applications of Family Mold Injection Molding
Family Mold Injection Molding finds its applications across a variety of industries, offering distinct advantages for the production of multiple components in a single cycle. Here are some of the key applications:
Automotive Industry
Family molds are used for producing various interior and exterior components, such as dashboard parts and engine covers.
Medical Devices
This process is crucial for manufacturing precision medical devices and components that require high-quality standards.
Consumer Electronics
Family molds are ideal for creating a range of electronic components, including housings, connectors, and casings.
Packaging Industry
The process is utilized for producing various packaging components like caps, closures, and containers.
Aerospace
Family molds contribute to the production of lightweight and high-strength components for aerospace applications.


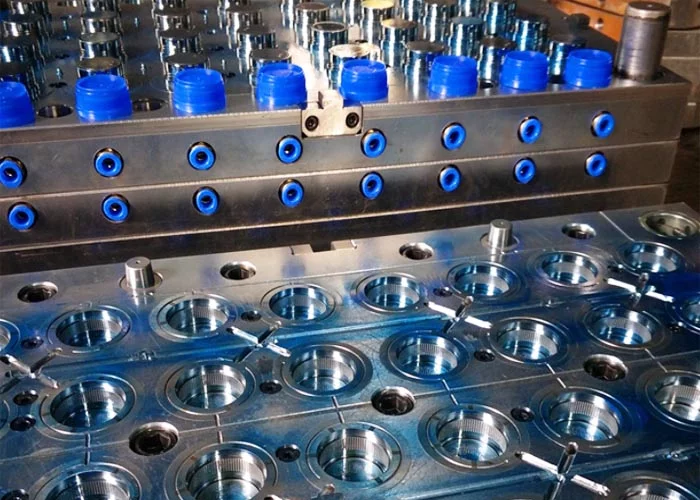
Family Molds are also called Multiple-Cavities Molds
A tool with one part is usually called a single cavity mold, whereas a custom molds with two or more cavities of same part is referred to as a multiple cavity molds(Family Mould). Aside from a single molding part being produced in a molding cycle,molds can be also designed to produce multiple numbers of same parts in one mold,the use of multi-cavity molds is becoming more and more common.Some extremely high-volume production molds,such as bottle caps moulds and preform molds, it can be up to 96 cavities,cutlery tableware plastic injection spoon moulds can reach 48 cavities,there are also medical test tube molds, etc.
A multiple cavities mold may also be referred to as a “family” mold. In fact, a family mold is more accurately defined as one which can produce multiple, like-sized parts in the same quantity and material. Family molding parts are often part of an assembly, such as a product top half and bottom half.
The most important factor to consider in the design of family molds is filling balance. In family(multi-cavity) injection molding molds, the runner system is usually designed as an “H”-shaped structure. The “H”-shaped runner system is geometrically completely symmetrical from the injection nozzle to each mold cavity, so it is also called “geometrically balanced” or “naturally balanced” runner system design.
Of course, the flow and filling of the molten resin in the “H”-shaped runner system is balanced, the melt temperature distribution caused by flow shear heat generation, and the asymmetry after the bifurcation of the runner may still lead to uneven filling in the cavity,so it is necessary to make necessary improvements to the injection
Family mold injection molding is a powerful manufacturing solution that offers a range of benefits for producing complex assemblies and diverse components. By understanding its advantages, applications, and considerations, manufacturers can leverage this technique to enhance productivity, reduce costs, and improve product quality.
For More Information:Contact our team of experts for consultation on how family mold injection molding can be integrated into your production process.
Thank you for visiting our guide on family mold injection molding. We hope this information has been valuable to your manufacturing endeavors. Don’t hesitate to reach out for further assistance or inquiries.