DMC Compression Mold
DMC compression molds lead innovation, precision craftsmanship, and durable quality to realize your innovation vision,customize your DMC product project
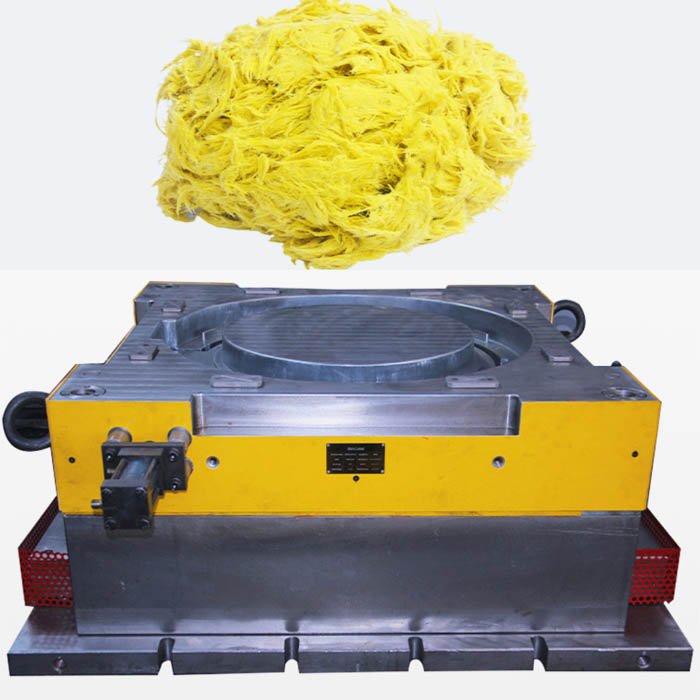
What is DMC(Bulk Molding Compound) Compression Mold
DMC (Bulk Molding Compound) compression mold is a type of mold used in the manufacturing of components and products from DMC materials. DMC is a thermosetting composite material made of a mixture of chopped glass fibers, thermosetting resin, and various additives. The DMC compression molding process involves shaping DMC material in a mold under high pressure and high heat, allowing it to harden and take the desired form. The compression mold is a tool or die used to shape and form the DMC material accurately and efficiently. It typically consists of two halves, the upper and lower halves, and is designed with the desired product shape and features. When the DMC material is placed in the mold cavity, the two halves of the mold come together under pressure and heat, causing the material to conform to the mold’s shape. This process results in the production of high-strength, durable, and dimensionally stable components that are commonly used in various industries, including automotive, electrical, and construction. DMC compression molds are crucial in achieving consistent and precise production of parts from DMC materials.
DMC mold production is a common plastic composite mold manufacturing method, usually used to produce parts with high requirements for high strength, heat resistance and corrosion resistance.
DMC material is the abbreviation of Bulk (Dough) molding compounds. When translated into Chinese, it is simply called bulk molding compound,it is also BMC and compression molding. In fact, the main components of BMC and DMC are the same, but they are called in different industries and regions. Different. The UK is the first country to adopt the abbreviation of DMC. DMC is more popular in Europe. On the contrary, the abbreviation of BMC is more popular in the United States. According to the definition of the American SPI; BMC material is chemically thickened DMC, which also shows that the history of DMC material is relatively long. China began to introduce British technology, and the DMC abbreviation is still relatively well-known in the country, especially in the electrical appliance industry. Standards such as JB/T7770-1995 also use the DMC abbreviation, but international development tends to use the BMC abbreviation. The abbreviation BMC is used more frequently than DMC.
What is DMC Mold Forming Process
The molding process of DMC (Bulk Molding Compound) mold is basically similar to other composite materials, such as SMC and BMC, including steps such as raw material preparation, mold design, filling the mold, heating and applying pressure, cooling and solidifying, demoulding, trimming and inspection,but there are also some special differences:
The following is the different of DMC mold:
- Material composition: DMC, SMC and BMC differ in material composition. DMC usually includes chopped glass fibers, thermosetting resins and various additives. SMC usually includes long glass fibers, resin and fillers. BMC also contains fiberglass, resins and fillers, but usually in smaller granular form.
- Molding method: Although they all use pressure molding technology, different composite materials may require different molding parameters such as temperature, pressure and time.
- Usage: Because different composite materials have different properties and strengths, they have different uses in different applications. DMC is commonly used in applications that require high strength and heat resistance, such as automotive parts manufacturing and electrical insulation. SMC is typically used for larger structural parts such as body panels and electrical equipment enclosures. BMC is often used in small parts such as switches and sockets.
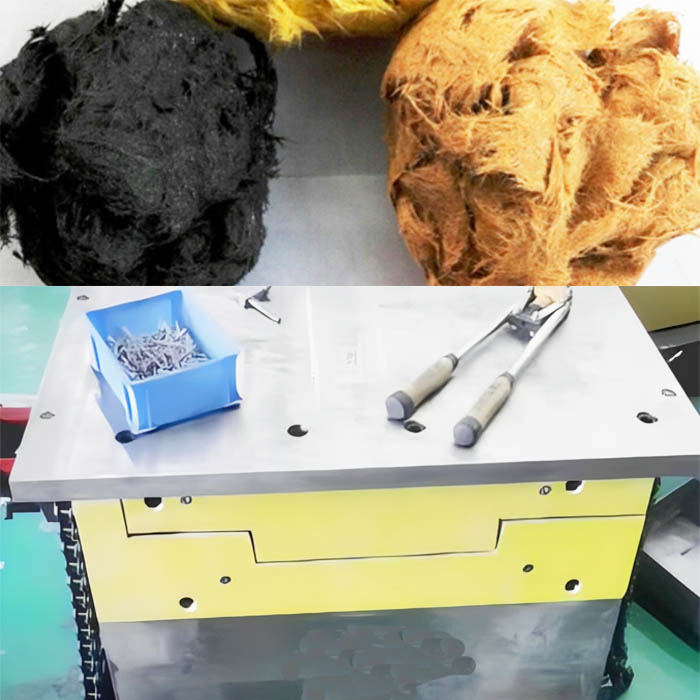
Although DMC, SMC and BMC have the same pressure forming principle, they have differences in raw materials, molding parameters and application fields, and they need to be selected according to specific needs.
To sum up, DMC material is a multifunctional composite material with excellent properties and is widely used in automobile manufacturing, electrical engineering, construction and other industries. Its strength, heat resistance and insulation make it ideal for a variety of applications.

Features of DMC Compression Mold
First, DMC materials have excellent strength and can withstand high loads and impacts, so they are widely used in manufacturing high-strength parts and products. It also has excellent heat resistance and can maintain stable performance in high temperature environments. This makes it widely used in high temperature engineering fields.
In addition, DMC material is an outstanding insulating material, suitable for electrical and electronic equipment manufacturing, and used to make electrical enclosures, insulators, etc. It also has good corrosion resistance and can withstand corrosion from a variety of chemicals, making it very reliable in harsh environments.
Last, DMC materials have extremely high dimensional stability and are not affected by temperature and humidity, making them suitable for applications requiring high precision. In addition, its products usually have a smooth surface and require no additional surface treatment, reducing production costs.
DMC (Bulk Molding Compound) material is a composite material composed of chopped glass fibers, thermosetting resin and various additives. This material has several outstanding characteristics that make it popular in a variety of industries and applications.
To sum up, DMC material is a multifunctional composite material with excellent properties and is widely used in automobile manufacturing, electrical engineering, construction and other industries. Its strength, heat resistance and insulation make it ideal for a variety of applications.
The difference between DMC mold and other composite material(SMC/BMC) molds
DMC (Bulk Molding Compound) molds differ from other composite material molds, such as SMC (Sheet Molding Compound) and BMC (Bulk Molding Compound) molds, in several aspects:
Material composition
DMC molds are usually composed of chopped glass fiber, thermosetting resin and various additives. These materials are available in powder or granular form.
SMC molds contain longer lengths of glass fiber, resin and fillers and are typically supplied in sheet or sheet form.
The material composition of BMC molds is similar to DMC, but is usually provided in smaller pellet form.
Application areas
DMC is commonly used in applications that require high strength, heat resistance and insulation, such as automotive parts, electrical insulation, building materials, etc.
SMC is usually used to manufacture larger structural parts, such as automobile body panels, power equipment casings, etc.
BMC is commonly used in small components such as switches, sockets and medical equipment components.
Molding method
Although they all use pressure forming technology, different composite materials may require different forming parameters such as temperature, pressure and time. This is because of their different material properties.
Features and Benefits
DMC molds have properties such as high strength, heat resistance, insulation, corrosion resistance and dimensional stability, making them suitable for applications requiring high performance.
SMC molds have excellent performance and appearance in the manufacturing of large structural parts because they can manufacture products with complex shapes and high surface quality requirements.
BMC molds are suitable for manufacturing small, fine parts and have excellent insulation and corrosion resistance.
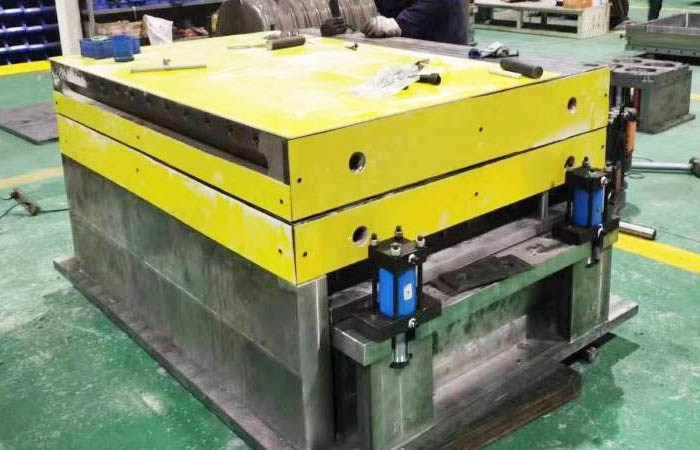
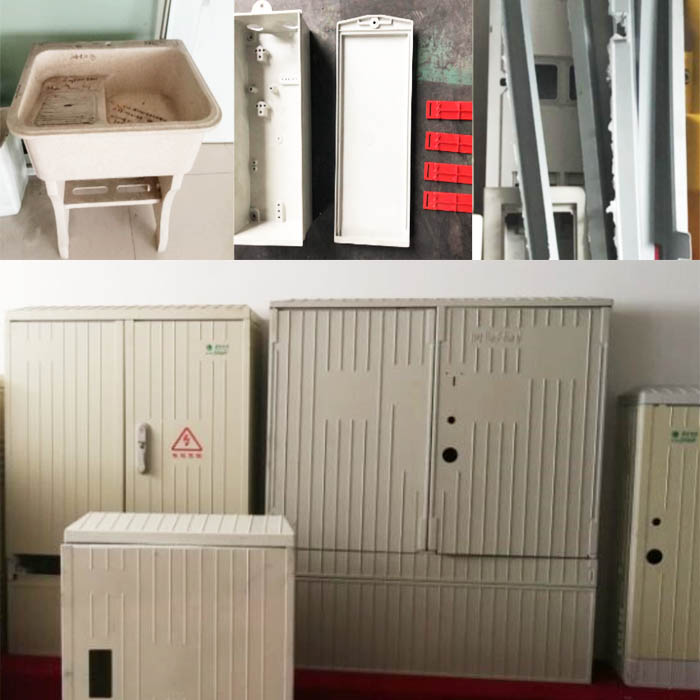
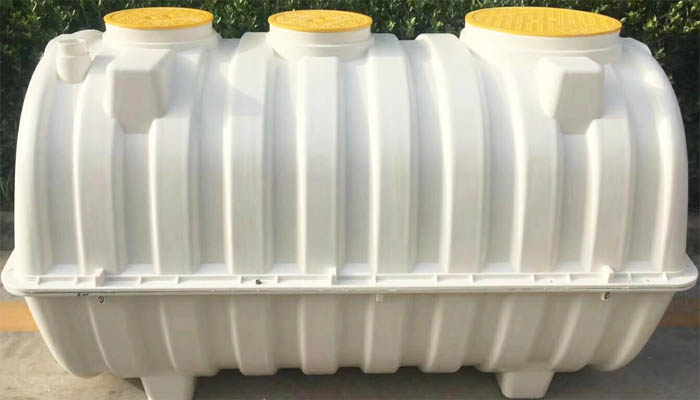

DMC Mold Future Outlook
DMC molds have many potential development prospects in the future. The following are some possible future prospects:
Wider application areas: As technology advances and demand continues to grow, DMC molds may expand to more application areas. For example, you may see more use of DMC products in emerging clean energy industries, such as the manufacturing of electric vehicles and renewable energy equipment.
Lightweight materials: DMC materials can achieve lightweighting during the manufacturing process, which is of great significance to the automotive industry and aerospace fields. The future is likely to see more lightweight designs to improve energy efficiency and reduce carbon emissions.
Intelligent manufacturing: As the manufacturing industry develops towards intelligence and automation, the production process of DMC molds may also become more intelligent. Technologies such as automated production lines and 3D printing may be combined with DMC molds to improve production efficiency and quality.
Sustainability: As the focus on sustainability continues to increase, the materials and manufacturing processes of DMC molds may become more environmentally friendly and sustainable. The use of recycled materials and more energy-efficient production methods will be the trend of the future.
Personalization and customization: Consumer demand for personalized products continues to increase, and the flexibility and customization capabilities of DMC molds make them ideal for meeting this demand. We may see more personalized DMC products in the future.
In short, DMC molds are expected to continue to develop and evolve in the future to meet changing market demands and sustainable development goals. As technology continues to advance, DMC molds will continue to play a key role in multiple fields, providing high-performance, environmentally friendly and innovative solutions to the manufacturing and engineering fields.