Composites Compression Molding
Focus on glass composite(SMC/BMC/DMC/FRP/GRP/CFRP/GMT/LFT) compression molding production
Compression moulding is mainly used for the molding of thermosetting plastics. According to the properties of the molding material and the characteristics of processing equipment and technology, compression molding can be divided into two types: compression molding and lamination molding.
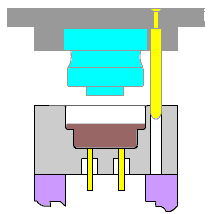
What is Compression Moulding ?
Compression molding is a molding process in which powder, granular or fibrous plastics are first put into a mold cavity at a molding temperature, and then the mold is closed and pressurized to shape and solidify the material. Compression molding can be used in the production of thermosets, thermoplastics and rubber materials.
The molding process uses the characteristics of each stage of the resin curing reaction to realize the molding of the product, that is, the molding material is plasticized, flows and fills the mold cavity, and the resin is cured. During the flow of the molding material filling the mold cavity, not only the resin flows, but also the reinforcing material flows, so the molding pressure of the molding process is higher than that of other processes, and it belongs to high-pressure molding. Therefore, it requires not only a hydraulic press that can control the pressure, but also a metal mold with high strength, high precision and high temperature resistance.
Compression forming products have dense texture, accurate size, smooth and clean appearance, no gate marks, and good stability.
What are benefits of Compression Molding?
1.Save cost:Compression forming is much cheaper than plastic injection molding,this is also one of the biggest benefits of compression molding,because the molding die is established, there is no need to consider the gate and runner, and it is not necessary to complete the mold flow analysis.
2. Production is easier:Compression molding is easier and cheaper when producing large part molds.
3. Part thickness flexibility:Compression-molded parts can be produced from the thinnest 1.5MM to the thickest 30MM, and can be seamlessly combined with product design through compression molding, without the bonding line problems that may occur in injection molding.
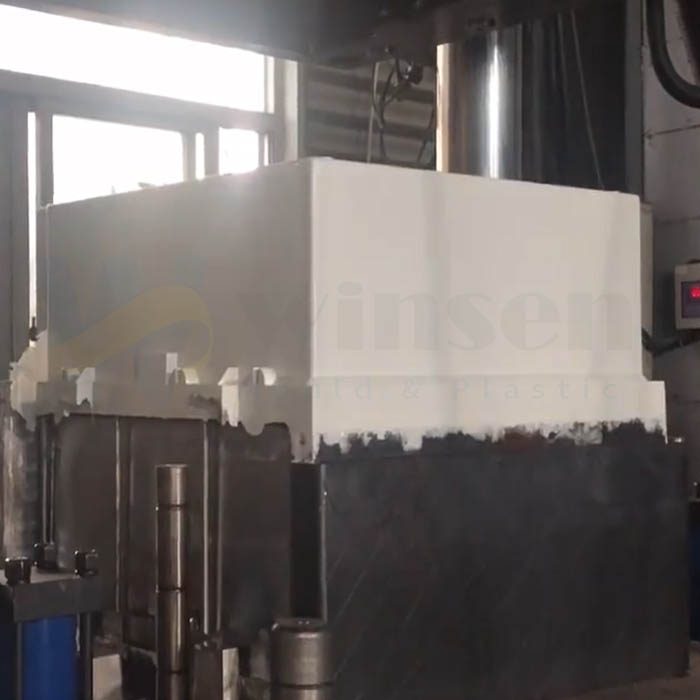
Advantages of compression molding
1. The loss of raw materials is small and will not cause too much loss (usually 2% to 5% of the quality of the product).
2. The internal stress of the product is very low, and the warpage deformation is also small, and the mechanical properties are relatively stable.
3. The wear of the mold cavity is very small, and the maintenance cost of the mold is low.
4. The cost of molding equipment is lower, the mold structure is simpler, and the manufacturing cost is usually lower than that of injection molds or transfer molding molds.
5. Larger flat products can be formed. The size of the product that can be formed by molding is only determined by the clamping force of the existing molding machine and the size of the template.
6. The shrinkage of the product is small and the repeatability is good.
7. A mold with a larger number of cavities can be placed on a given template, with high productivity.
8. Can adapt to automatic feeding and automatic removal of products.
9. High production efficiency, easy to achieve specialized and automated production.
10. The product has high dimensional accuracy and good repeatability.
11. The surface is smooth and no secondary modification is required.
12. It can form products with complex structure at one time.
13. Mass production, the price is relatively low.
Disadvantages of compression molding
1. The molding cycle in the whole production process is long, the efficiency is low, and it has a large physical consumption on the staff.
2. It is not suitable for compression molding of complex products with depressions, side slopes or small holes.
3. In the production process, it is difficult to fully fill the mold, and there are certain technical requirements.
4. After the curing stage, different products have different stiffness, which affects the performance of the product.
5. For products with high dimensional accuracy requirements (especially for multi-cavity molds), this process is somewhat short-handed.
6. The flash edge of the final product is thick, and the workload of removing the flash edge is large.
7. The disadvantage of compression molding is that the mold manufacturing is complicated, the investment is large, and it is limited by the press, so it is most suitable for mass production of small and medium-sized composite products.
Difference Between Compression Molding and Lamination Molding
1. Compression Forming
Compression molding is the primary method of molding thermosets and reinforced plastics. The process is to pressurize the raw material in a mold that has been heated to a specified temperature, so that the raw material melts and flows and fills the mold cavity evenly.
2. Lamination Molding
Lamination molding is a method of combining two or more layers of the same or different materials into a whole under the conditions of heating and pressure as a sheet or fibrous material as a filler.
The lamination molding process consists of three stages of dipping, pressing and post-processing, and is mostly used to produce reinforced plastic sheets, pipes, bars and model products. The products produced are dense in texture and smooth in surface.
Scope of application of compression molding
Mainly used as structural parts, connecting parts, protective parts and electrical insulating parts. Widely used in industry, agriculture, transportation, electrical, chemical, construction, machinery and other fields. Due to the reliable quality of molded products, they have also been used in weapons, aircraft, missiles, and satellites.
There are many varieties of molding materials, which can be prepreg materials, premix materials, or blanks. The main varieties of molding materials currently used are: prepreg, fiber premix, BMC, DMC, FRP, SMC, GMT, GRP and LFT.
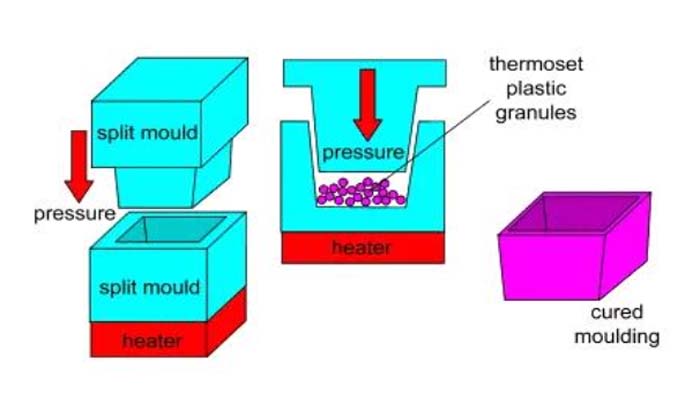
Compression molding process
The molding process can be divided into the following types according to the physical state of the reinforcing material and the variety of molding materials:
1. Fiber material molding method: The pre-mixed or pre-impregnated fibrous molding material is put into the metal mold, and the composite product is formed under a certain temperature and pressure.
2. Shredded cloth molding method: Cut the scraps of glass fiber cloth or other fabrics soaked in resin glue, such as linen cloth, organic fiber cloth, asbestos cloth or cotton cloth, into pieces, and then heat and pressurize them in the mold to form a composite. material products. This method is suitable for forming products with simple shapes and general performance requirements.
3. Fabric molding method: The two-dimensional or three-dimensional fabric pre-woven into the desired shape is impregnated with resin glue, and then placed in a metal mold to heat and press to form a composite product.
4. Lamination molding method: Cut the glass fiber cloth or other fabric pre-impregnated with resin glue into the desired shape, and then heat or pressurize the composite product in the metal mold.
5. Winding molding method: The continuous fiber or cloth (belt) pre-impregnated with resin glue is provided with a certain tension and temperature through a special winding machine, wrapped on the core mold, and then put into the mold for heating and pressure molding. Composite products.
6. Sheet plastic (SMC) molding method: Cut the SMC sheet according to the product size, shape, thickness and other requirements, and then stack the multi-layer sheets and put them into a metal mold to heat and press to form the product.
7. Preform molding method: firstly, short-cut fibers are made into preforms with similar shapes and sizes, put them into a metal mold, and then inject the prepared binder (resin mixture) into the mold. Forming under certain temperature and pressure.
8. Orientation auxiliary molding: The main stress direction of the unidirectional prepreg product is oriented and laid, and then molded. The fiber content in the product can reach 70%, which is suitable for molding products with high unidirectional strength requirements.
9. Molding powder molding method: Molding powder is mainly composed of resin, filler, curing agent, colorant and mold release agent. The resins are mainly thermosetting resins (such as phenolic resins, epoxy resins, amino resins, etc.), and thermoplastic resins with high molecular weight, poor fluidity and high melting temperature that are difficult to inject and extrude can also be made into molding powder. The molding process of molding powder and other molding materials is basically the same. The main difference between the two is that the former does not contain reinforcing materials, so its products have lower strength and are mainly used for secondary stress parts.
10. Adsorption preform molding method: use adsorption method (air adsorption or wet pulp adsorption) to preform glass fiber into a preform similar in structure to a molded product, and then place it in a mold and pour it on it. Into the resin paste, molding at a certain temperature and pressure. The material cost of this method is low, and long chopped fibers can be used, which is suitable for molding products with complex shapes, and can be automated, but the equipment cost is high.
11. Bulk molding compound molding method: Bulk molding compound (BMC) is a fiber-reinforced thermosetting plastic, and is usually composed of unsaturated polyester resin, chopped fiber, filler and various additives. A well-mixed dough prepreg. A low shrinkage additive is added to the BMC, which greatly improves the appearance of the product BMC.
12. Felt molding method: In this method, resin (mostly phenolic resin) is used to impregnate glass fiber mats, and then dried into prepreg mats, which are cut into desired shapes and placed in molds, heated and pressed into products. . This method is suitable for forming thin-walled large-scale products with simple shapes and little change in single thickness.
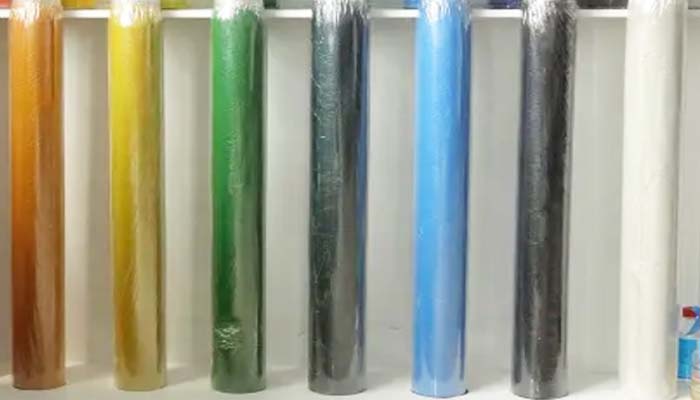
2. Reinforcement material
The commonly used reinforcing materials in molding materials mainly include glass fiber cutting wire, untwisted roving, twisted roving, continuous glass fiber bundle, glass fiber cloth, glass fiber mat, etc. There are also a small number of special products using asbestos felt, asbestos fabric (cloth) and Asbestos paper, high silica fiber, carbon fiber, organic fiber (such as aramid fiber, nylon fiber, etc.) and natural fiber (such as linen, cotton, scouring cloth, non-scouring cloth, etc.) and other varieties. Sometimes two or more fiber blends are used as reinforcing materials.
Raw materials for compression molding
1. Synthetic resin
The molding compound used in composite molding products requires the synthetic resin to have:
① It has good wettability to the reinforcing material, so as to form a good bond on the interface between the synthetic resin and the reinforcing material;
② With proper viscosity and good fluidity, it can evenly fill the entire cavity with the reinforcing material under pressing conditions;
③ It has a suitable curing speed under pressing conditions, and no by-products or few by-products are produced during the curing process, and the volume shrinkage rate is small;
④ It can meet the specific performance requirements of molded products. According to the above material selection requirements, commonly used synthetic resins are: unsaturated polyester resin, epoxy resin, phenolic resin, vinyl resin, furan resin, silicone resin, polybutadiene resin, allyl ester, melamine resin, Polyimide resin, etc. In order to make molded products achieve specific performance indicators, after selecting resin varieties and grades, corresponding auxiliary materials, fillers and pigments should also be selected.
3. Auxiliary materials
It generally includes auxiliary materials such as curing agent (initiator), accelerator, diluent, surface treatment agent, low shrinkage additive, mold release agent, colorant (pigment) and filler.