Compression Molding is key of Precision Manufacturing.In modern manufacturing, compression molding technology has become an indispensable part due to its high efficiency, cost-effectiveness and design flexibility. This article will take a deep look at the principles, process flow, application areas of compression molding and how it shapes modern industrial compression molds production.
Compression molding is a manufacturing technique that uses a mold to apply pressure to a material to deform it or fill the mold cavity to form a desired shape. This technique is widely used in the processing of plastics, rubber, ceramics and other materials.
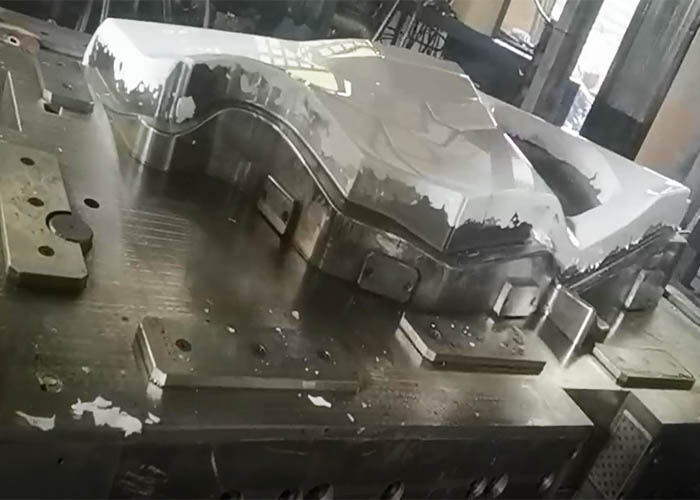
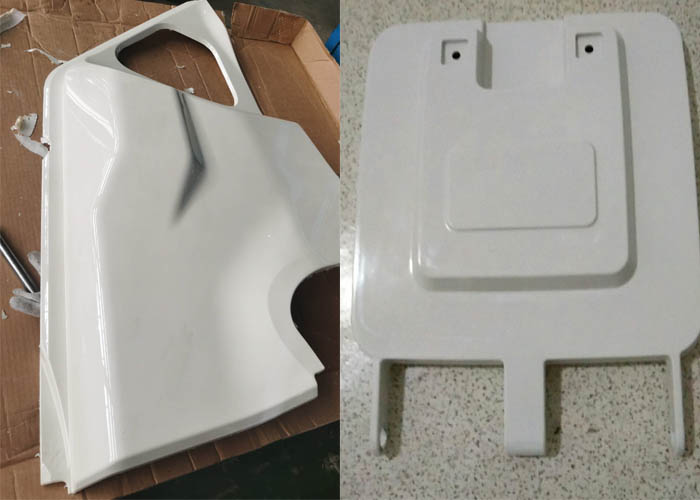
Table of Contents
ToggleCompression molding technology overview
Compression molding, also known as compression molding or pressure molding, is a manufacturing process that places a material into a mold at high temperature or room temperature, deforms it by applying pressure and fills the mold cavity to form the desired shape. This technology can be used for a variety of materials such as thermosetting plastics, thermoplastics, rubber, ceramics, etc.
The process flow of compression molding
The basic process flow of compression molding includes the following steps:
- Material preparation: Select suitable materials such as plastic granules, powders or prefabricated sheets according to product requirements.
- Preheating: For thermosetting materials, the materials need to be preheated to a certain temperature to make them plastic.
- Loading: Put the material into the upper or lower mold of the mold.
- Closing the mold: Close the mold through a press to apply pressure to the material.
- Pressure holding and curing: Maintain a certain pressure and time to allow the material to cure and form in the mold.
- Demolding: After the material is cured, open the mold and take out the molded product.
- Post-processing: Trim, grind or perform secondary processing on the product as needed.
Key Advantages of Compression Molding
The reason why compression molding technology is widely used mainly benefits from the following advantages:
High production efficiency: high degree of automation, suitable for mass production.
High material utilization rate: less material waste and significant cost-effectiveness.
Design flexibility: Products with complex shapes and high precision can be manufactured.
Good product consistency: The repeated use of molds ensures product consistency.


Application of compression molding in different fields
Compression molding technology plays an important role in many industries:
- Automotive industry: used to manufacture various plastic and rubber parts, such as dashboards, bumpers, etc.
- Electronics industry: production of housings and insulation parts for electronic devices.
- Medical equipment: manufacture of disposable medical devices and parts for precision instruments.
- Aerospace: used to manufacture lightweight and high-strength composite parts.


Challenges and Solutions of Compression Molding
Although compression molding technology has many advantages, it also faces some challenges in practical applications:
Mold cost: The design and manufacturing cost of high-precision molds is high.
Material limitations: Some materials may not be suitable for compression molding or require special processing conditions.
Product defects: Such as bubbles, warping, or incomplete filling.
To overcome these challenges, manufacturers need to:
- Optimize mold design: Improve mold durability and maintainability.
- Choose the right material: Choose the right material based on product requirements and molding process characteristics.
- Improve process control: Reduce product defects by precisely controlling temperature, pressure, and time.
Future trends in compression molding
Compression molding technology is also evolving as new materials and technologies continue to emerge. Future trends include:
Intelligent production: integrating sensors and intelligent control systems for more precise process control.
Material innovation: developing new high-performance materials to meet specific application requirements.
Environmentally friendly: using recyclable or biodegradable materials to reduce environmental impact.
Customized production: meeting small batch and diversified market needs.
As a precision manufacturing technology, compression molding is constantly driving industrial production towards a more efficient and economical direction. With the continuous emergence of new materials and new technologies, the application areas of compression molding will become more extensive, and its position in the future manufacturing industry will become more important.