In the world of manufacturing, where precision and efficiency reign supreme, compression molding stands out as a reliable and cost-effective method for producing high-quality, durable parts. From automotive components to intricate electrical insulators, this versatile process has been shaping industries for decades. But what exactly is compression molding, and why should you care?
This comprehensive guide dives deep into the world of compression molding, exploring its advantages, applications, and how it can benefit your business. Whether you’re a seasoned engineer or a curious entrepreneur, this article will equip you with the knowledge to make informed decisions about your manufacturing needs.
Table of Contents
ToggleWhat is Compression Molding?
Compression molding is a manufacturing process that uses heat and pressure to shape raw materials, typically thermosetting polymers or composite materials, into a desired form. The process involves placing a pre-measured amount of material into a heated compression mold cavity, closing the mold, and applying pressure to force the material to conform to the mold’s shape.
Once the material cures (solidifies) under heat and pressure, the mold opens, and the finished part is ejected. This simple yet effective process offers numerous advantages over other molding techniques, making it a popular choice for a wide range of applications.
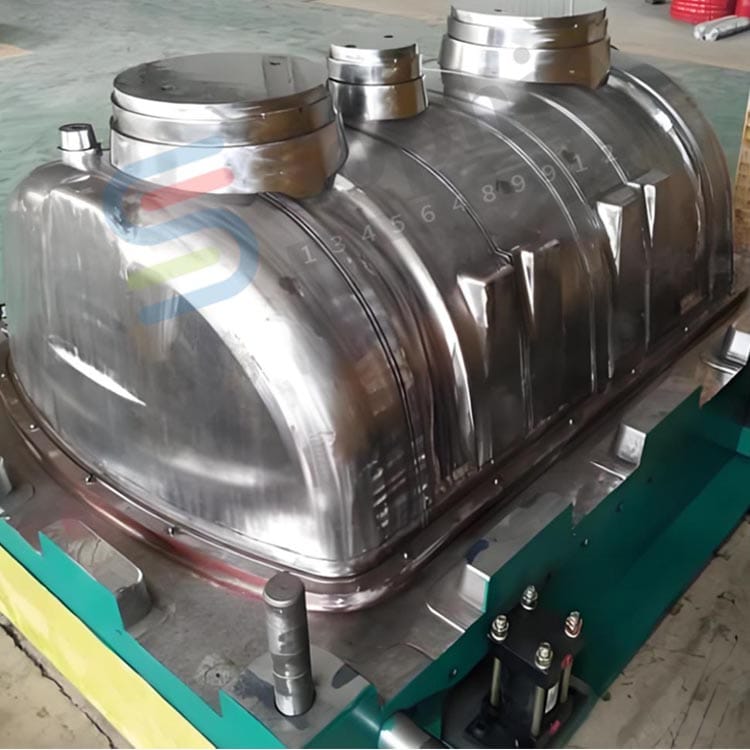
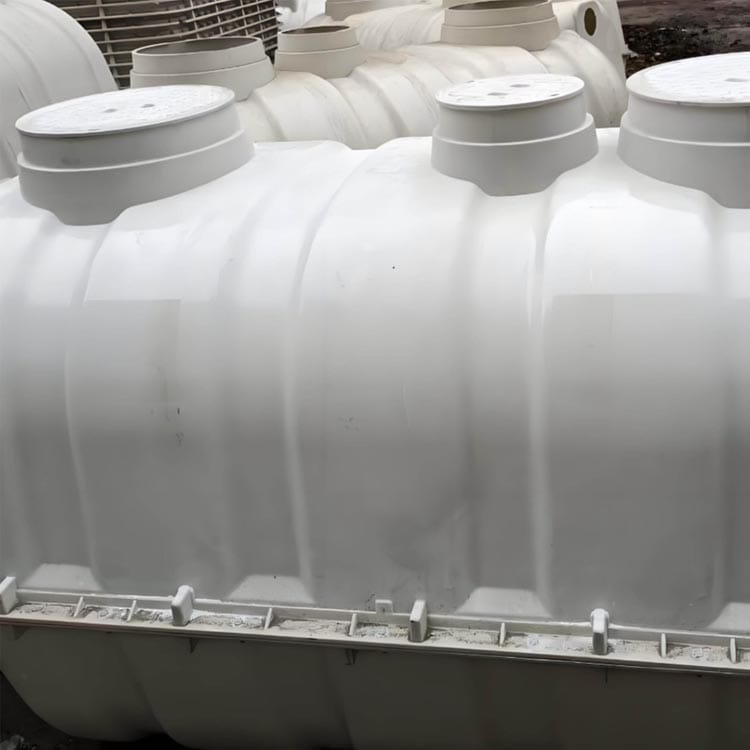
Why Choose Compression Molding? The Benefits Speak for Themselves
Cost-Effectiveness
Compression molding is a relatively low-cost manufacturing method, especially for medium to high-volume production runs. The process requires minimal tooling and setup costs compared to other techniques like injection molding.
Material Versatility
Compression molding accommodates a wide range of materials, including thermosetting plastics (phenolics, epoxies, silicones), rubber compounds, and even some thermoplastics. This versatility allows manufacturers to choose the most suitable material for their specific application.
High Strength and Durability
Compression-molded parts are known for their exceptional strength, dimensional stability, and resistance to heat, chemicals, and wear. This makes them ideal for demanding applications in industries like automotive, aerospace, and electrical.
Design Flexibility
Compression molding allows for the production of complex shapes with intricate details, including undercuts, ribs, and bosses. This design flexibility opens up a world of possibilities for product designers and engineers.
Environmentally Friendly
Compression molding generates minimal waste compared to other manufacturing processes. The excess material, known as flash, can often be recycled and reused, reducing environmental impact.
Compression Molding in Action: Real-World Applications
The versatility of compression molding makes it suitable for a wide range of industries and applications. Here are just a few examples:
Automotive: Brake pads, clutch facings, gaskets, seals, engine components, interior trim parts.
Electrical: Insulators, connectors, circuit breakers, switchgear components.
Aerospace: Radomes, antenna housings, interior panels, ducting.
Appliances: Handles, knobs, housings, insulation components.
Consumer Goods: Cookware handles, appliance housings, power tool components.
Is Compression Molding Right for Your Project?
While compression molding offers numerous advantages, it’s essential to consider your specific project requirements before choosing this method. Factors to consider include:
Part Size and Complexity: Compression molding is well-suited for medium to large parts with relatively simple to moderately complex geometries.
Production Volume: This method is most cost-effective for medium to high-volume production runs.
Material Selection: Ensure that your desired material is compatible with compression molding.
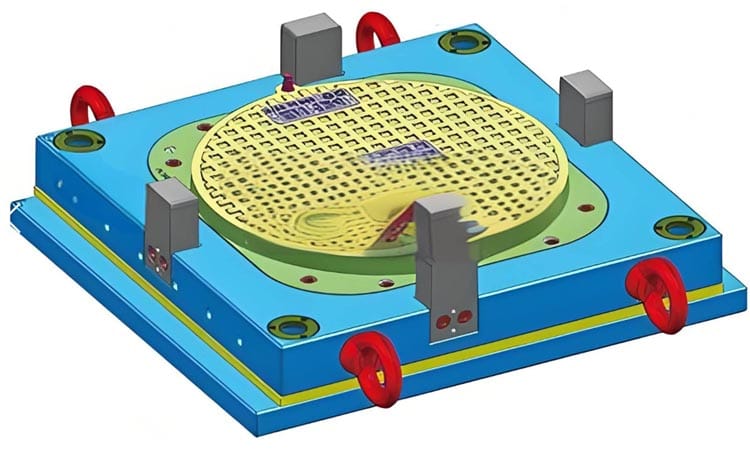
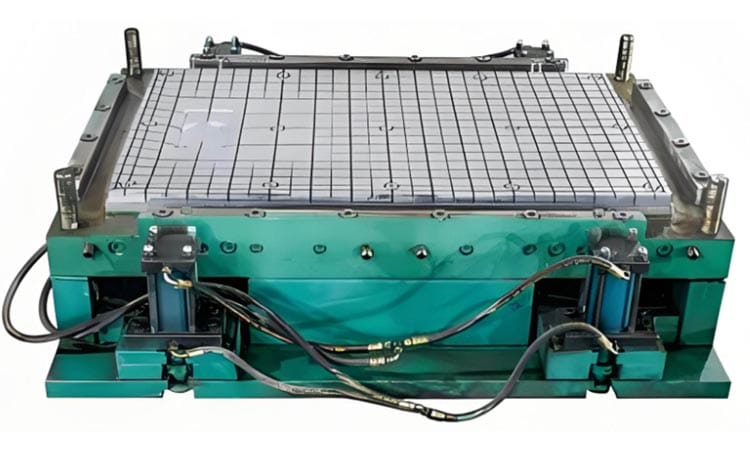
Partnering with a Compression Molding Expert
If you’re considering compression molding for your next project, partnering with an experienced manufacturer is crucial. A reputable compression molding company can provide valuable guidance on material selection, design optimization, and production processes to ensure the success of your project.
Looking for a reliable compression molding partner? Look no further! Winsen has years of experience in delivering high-quality compression-molded parts to a wide range of industries. Contact us today to discuss your project requirements and discover how we can help you bring your ideas to life.
Conclusion
Compression molding is a time-tested manufacturing process that continues to play a vital role in various industries. Its cost-effectiveness, material versatility, and ability to produce durable, high-performance parts make it an attractive option for manufacturers worldwide. By understanding the benefits and applications of compression molding, you can make informed decisions about your manufacturing needs and unlock new possibilities for your business.
Ready to experience the advantages of compression molding? Contact Winsen Mold today and let us help you take your product to the next level!