Compression Molds helping in the European Market
Compression Molds are driving force in the European market.In the heart of the European manufacturing sector, compression molding molds are playing an increasingly pivotal role, shaping the future of production across various industries. As a high-volume, high-pressure molding method, compression molding is particularly well-suited for creating complex parts with high-strength fiberglass reinforcements. This blog will delve into the significance of compression molds in the European market, their applications, and the advantages they offer in terms of economy and efficiency.
Table of Contents
ToggleUnderstanding Compression Molds
Compression molds are the backbone of the compression molding process, which involves heating a mold to a specific temperature and then placing the material (usually a thermoset plastic) into the mold cavity. The mold is then closed, and pressure is applied until the material conforms to the shape of the mold cavity. This process is ideal for producing large, detailed parts with excellent surface finish and dimensional stability

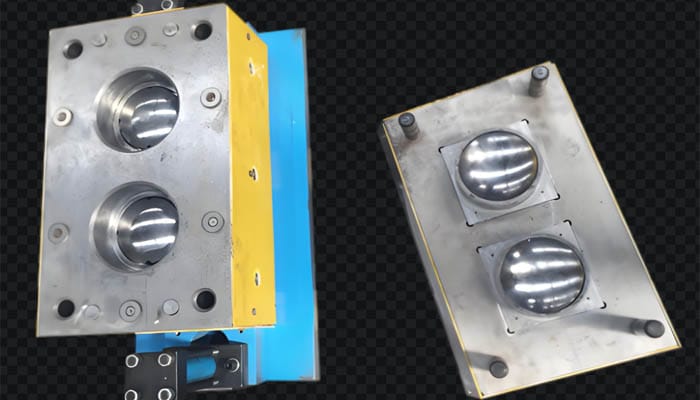
Materials Used in Compression Molds
Compression molds are compatible with a wide range of thermoset plastics, including:
Watch the military parade
- Phenolic Resins: Known for their heat resistance and electrical insulation properties.
- Urea-Formaldehyde Resins: Used in applications requiring dimensional stability and hardness.
- Epoxy Resins: Chosen for their excellent adhesive properties and chemical resistance.
- Polyesters: Commonly used for their versatility and strength-to-weight ratio.
- Melamine Resins: Selected for their durability and heat resistance.
Each of these materials has unique properties that make them suitable for specific applications, and the choice of material can significantly influence the performance of the final product
Applications Across Industries
Compression molds have found their way into various European industries, including:
- Automotive: Producing large components such as bumpers, dashboards, and door panels.
- Aerospace: Manufacturing lightweight, high-strength parts for aircraft and spacecraft.
- Electrical and Electronics: Creating insulation components and housings for various electrical devices.
- Construction: Fabricating durable materials for construction and infrastructure projects.
- Medical: Producing parts with precise dimensions and high surface quality for medical devices.
The versatility of compression molds allows them to cater to the specific needs of these industries, providing tailored solutions for complex manufacturing challenges
Economic Benefits
The use of compression molds in the European market is not only about the quality of the end product but also about economic efficiency. The process is advantageous because it:
Minimizes Material Waste
Precise material placement and controlled pressure application reduce waste.
Optimizes Production Costs
High-volume production capabilities mean lower costs per unit.
Reduces Post-Processing Needs
The high precision of compression molding often eliminates the need for secondary finishing processes.
These economic benefits are particularly important in a competitive market like Europe, where manufacturers are constantly seeking ways to reduce costs without compromising on quality
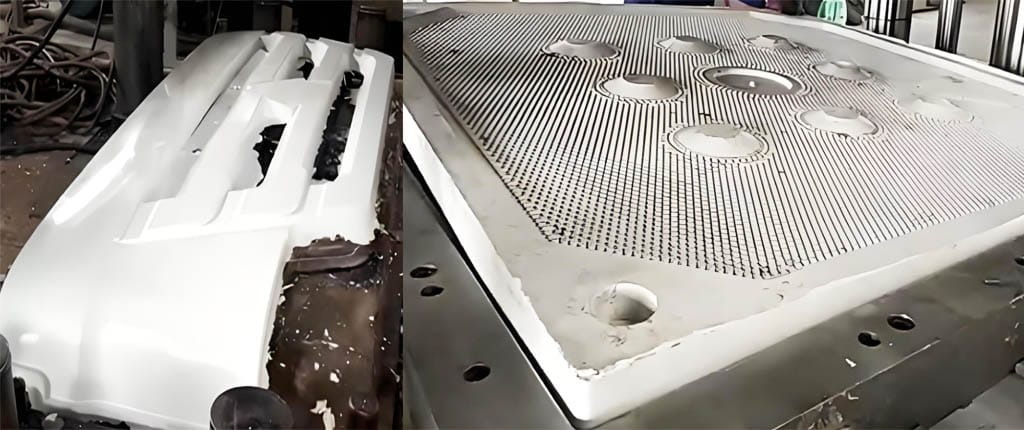
Environmental Considerations
In line with Europe’s commitment to sustainability, compression molds also contribute to environmental responsibility:
- Material Efficiency: The process uses materials efficiently, reducing waste.
- Energy Efficiency: Modern compression molding machines are designed to be energy-efficient.
- Recyclability: While thermosets are not recyclable, the focus is shifting towards using more sustainable materials and practices.
The Future of Compression Molds in Europe
As the European market continues to evolve, so does the role of compression molds. Future trends indicate a move towards:
- Automation: Increasingly automated processes for improved efficiency and precision.
- Advanced Materials: The development and use of new, high-performance plastics.
- Sustainability: A growing focus on environmentally friendly practices and materials.
Compression molds are poised to play a significant role in driving innovation and efficiency in the European manufacturing sector, contributing to the region’s economic growth and technological advancement
In conclusion, compression molds are a critical component of the European manufacturing landscape, offering a blend of simplicity, efficiency, and versatility. As the market continues to demand high-quality products with complex geometries and high strength, compression molds stand ready to meet these challenges. Understanding the fundamentals of compression mold design and the molding process is essential for manufacturers aiming to leverage this technology to its fullest potential. By adhering to best practices and embracing continuous innovation, the future of industrial manufacturing with compression molds in Europe looks both promising and exciting.