Exploring FAST MICH Kevlar Helmet Compression Mold,In the dynamic world of protective gear, innovation is a constant pursuit. One groundbreaking advancement that has redefined safety standards is the Compression Mold used in crafting FAST MICH Kevlar Helmets. This blog delves into the intricate details of this cutting-edge technology, unraveling the process, benefits, and the impact it has on elevating the performance and reliability of these state-of-the-art bulletproof helmets.See more technology on YOUTUBE
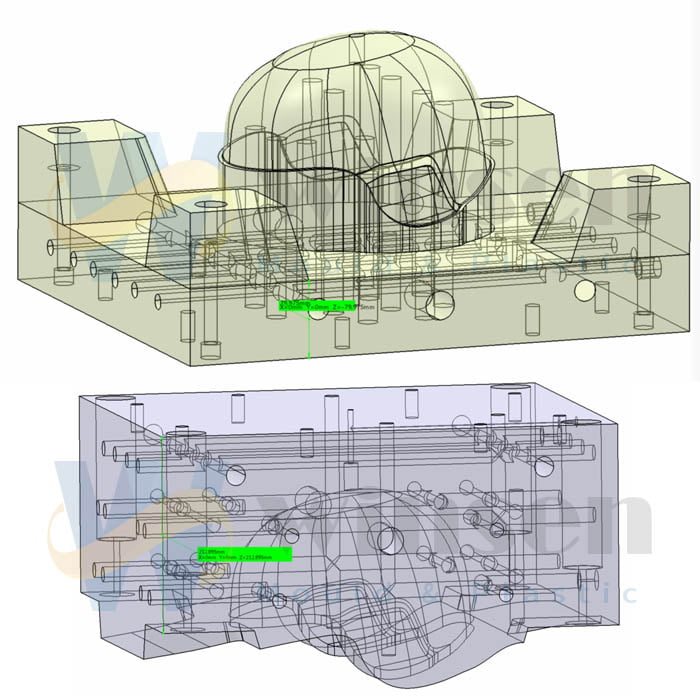

Exploring FAST MICH Kevlar Helmet Compression Mold
At the heart of every FAST MICH Kevlar Helmet lies a meticulous process driven by Compression Mould technology. We take a closer look at how this innovative moulding technique contributes to precision engineering, ensuring each helmet meets the highest standards of safety and performance.
Unveiling the Technology Behind FAST MICH Kevlar Helmet Compression Molds
kevlar bulletproof helmet mold is a compression molding process,it is assembled on the hydraulic press to heat and put kevlar material into mold cavity to produce FAST MICH kevlar bulletproof helmet.
Why are FAST MICH Kevlar Helmet compression molding
Compression Molds excel in precision molding, ensuring that advanced materials like UD/Kevlar bulletproof composites are shaped with exacting accuracy. This precision is pivotal in maintaining the material’s integrity, a key factor in the helmets’ ability to withstand ballistic threats effectively.
Beyond precision, Compression Moulds enable the replication of complex designs inherent to FAST MICH Helmets. The intricate details, crucial for both aesthetics and functionality, are faithfully reproduced, ensuring that each helmet meets the specified design standards.
Structural integrity is further enhanced through Compression Moulds. The application of heat and pressure in the molding process results in helmets with superior strength, contributing to their overall durability and protective qualities. This high-strength construction is essential for ensuring the longevity and reliability of the final product.
The enhancement of FAST MICH Helmets through Compression Moulds is a testament to the transformative impact of advanced manufacturing techniques. These specialized molds play a crucial role in shaping the distinctive design of the helmets, contributing to optimal protection without compromising on comfort and functionality.
In summary, Compression Molds elevate FAST MICH Helmets by combining precision, consistency, efficiency, and customization. Their role in the manufacturing process is instrumental in creating helmets that not only offer optimal protection but also prioritize comfort and functionality, meeting the diverse needs of military and law enforcement professionals.
FAST MICH Kevlar Helmet Compression Mold manufacturer
WS MOLD a leading Chinese manufacturer specializing in molds for military protective equipment, has been established as an industry pioneer. The compression molds utilized in crafting FAST MICH Kevlar Bulletproof Helmets, made from UD/Kevlar bulletproof composite material, have garnered widespread acclaim from both domestic and international customers.
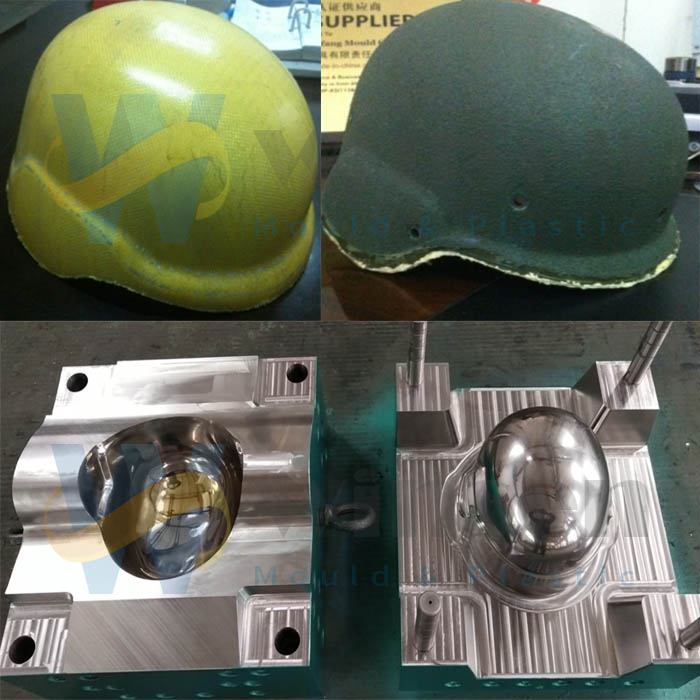
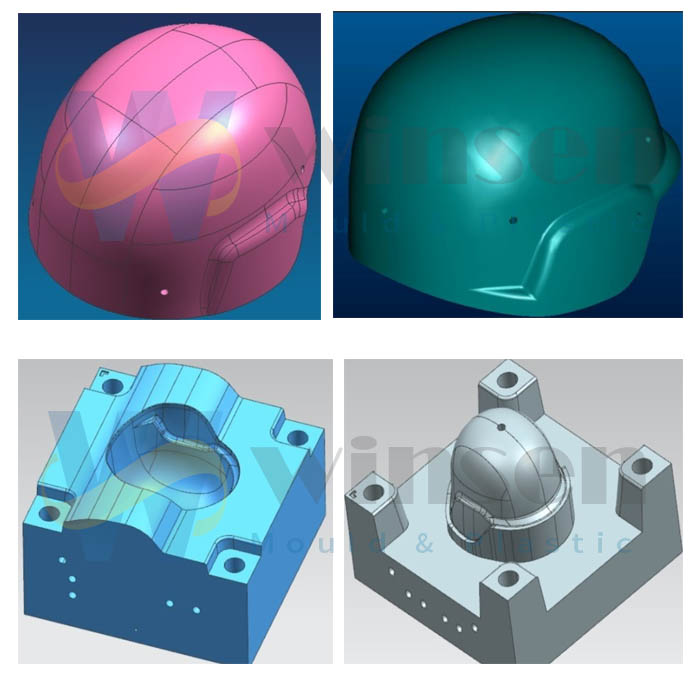
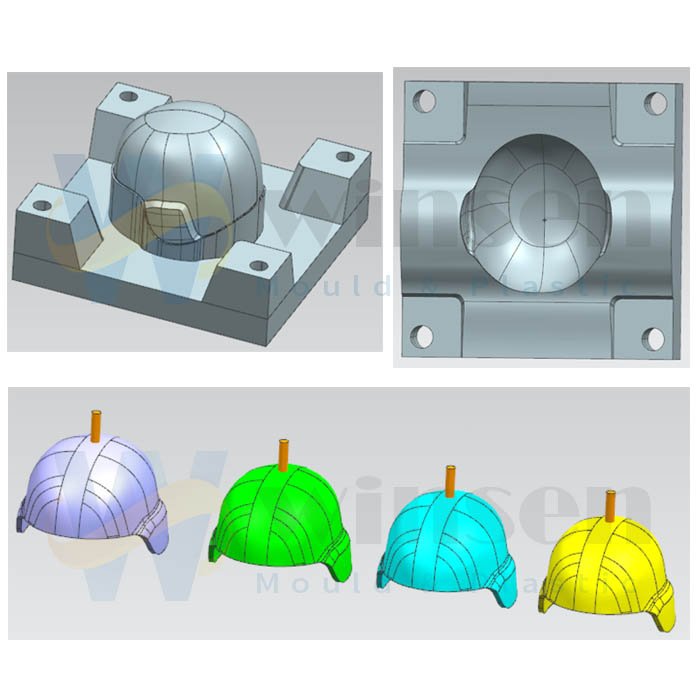
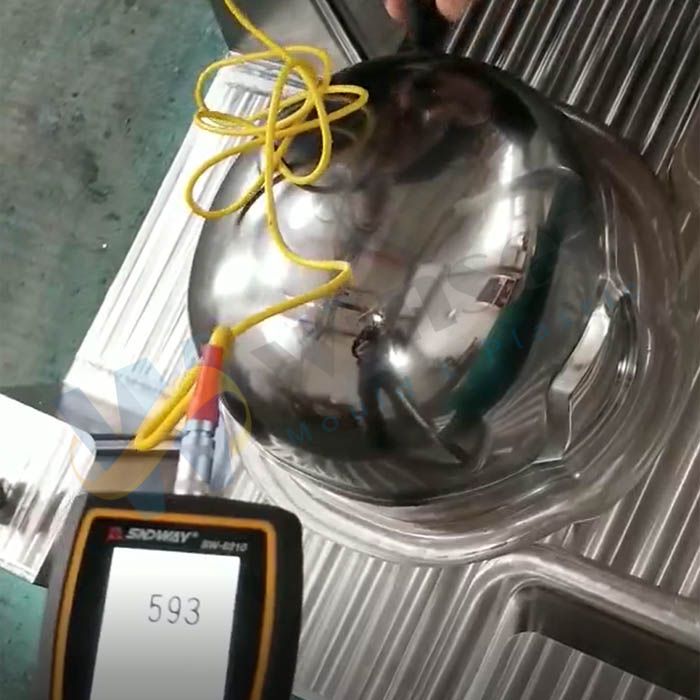
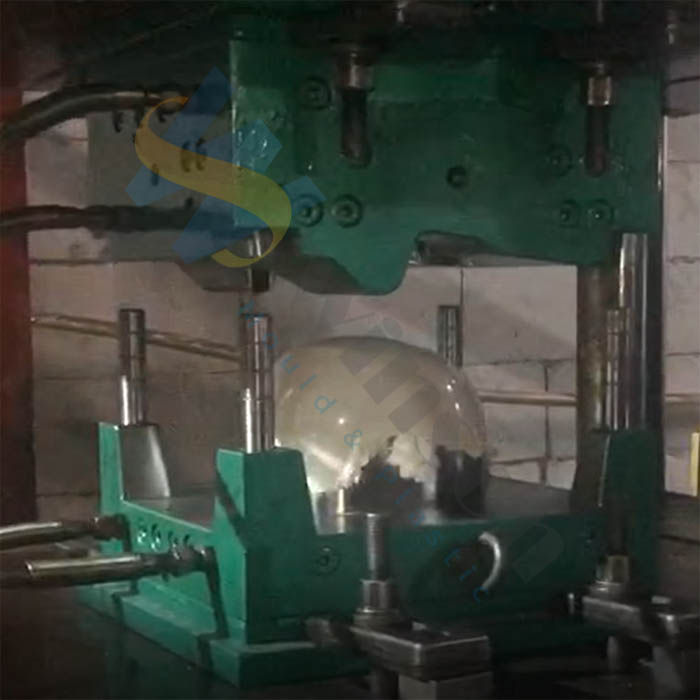
Since its inception, Winsen has dedicated extensive efforts to the meticulous study of bulletproof equipment mold production processes. A multitude of sophisticated molds has been supplied to both domestic and international military units, earning widespread acclaim within society. In recent years, a continuous focus on technological innovation and elevated production standards has resulted in consistently stable product quality and expedited services. This commitment to excellence has garnered the support and trust of our valued customers. We extend a warm welcome to friends from all industries to visit and engage in discussions about potential collaborations.
The inception of the helmet has its roots in a dramatic moment. Amid the tumultuous events of the First World War, a resourceful soldier, seeking protection, ingeniously turned a cooking pot upside down to avert potential injuries. This makeshift solution inspired others to explore and design a dedicated helmet. Over time, as technology advanced, the evolution of the helmet unfolded. From its initial form as a steel helmet, primarily designed to resist shell fragments, to the contemporary marvel we have today—a sophisticated headpiece capable of withstanding bullets and providing enhanced protection in modern warfare scenarios.