Heat treatment process of plastic mould, Mould heat treatment is an important means to improve the hardness performance of steel materials. Generally, it is carried out after the mold is roughed. After the heat treatment is returned, the finishing process is carried out. However, there are risks in the process of processing. Improper handling will cause cracks in the steel material, Scrap.
Table of Contents
ToggleWhat are the reasons for the abnormality of the plastic mold steel?
(1). There is serious segregation of carbide in the mold material.
(2). Mold has machining or cold plastic stress.
(3). Improper heat treatment operation of molds (too fast heating or cooling, improper selection of quenching cooling medium, too low cooling temperature, too long cooling time, etc.).
(4). The mold has complex shape, uneven thickness, sharp corners and thin threaded holes, etc., which make the thermal stress and tissue stress residual too large.
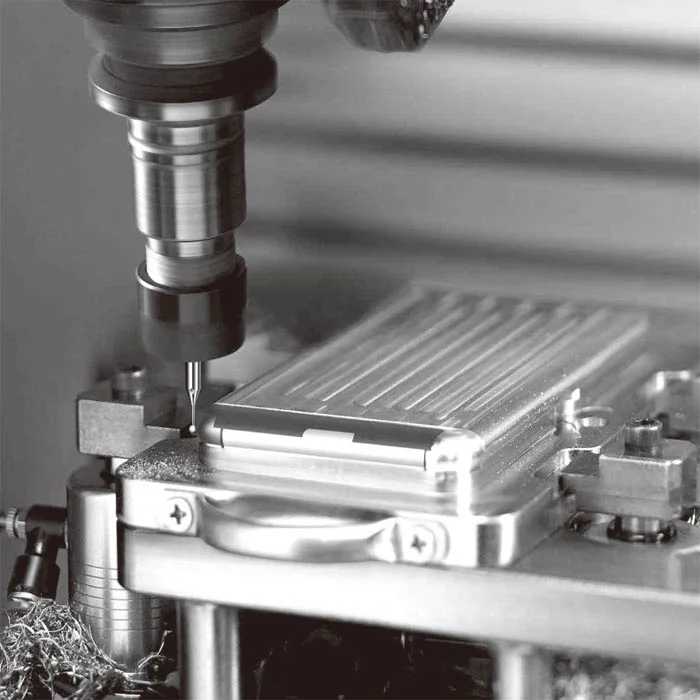
Heat treatment process of plastic mould
(5). The heating temperature of the plastic mold quenching process is too high to cause overheating or overburning.
(6). The mold is not tempered in time after quenching or the tempering holding time is insufficient.
(8). If the grinding process of mold heat treated is improper.
(9). There are high tensile stress and microcracks in the hardened layer during EDM after heat treatment of the mold.
(7). When the mold is repaired and quenched, it is reheated and quenched without intermediate annealing.
WS Mould is an expert in the injection mould industry. There are 1000 sets of moulds made every year. It is a leading mould enterprise in the industry. If you have more questions about injection moulds, please feel free to contact me.
Heat treatment characteristics of plastic mould
1. Heat treatment characteristics of carburized steel plastic molds
(1). For plastic molds with high hardness, high wear resistance and high toughness requirements, carburizing steel should be used to manufacture, and carburizing, quenching and low temperature tempering should be used as the final heat treatment.
(2). Requirements for the carburized layer, generally the thickness of the carburized layer is 0.8-1.5mm. When pressing plastics containing hard fillers, the thickness of the mold carburized layer is required to be 1.3-1.5mm. When pressing soft plastics, the carburized layer is required The thickness is 0.8-1.2mm. The carbon content of the carburized layer is preferably 0.7% to 1.0%. If carbon and nitrogen co-infiltration are used, the wear resistance, corrosion resistance, oxidation resistance and anti-sticking properties will be better.
(3). The carburizing temperature is generally 900-920°C, and 840-860°C is suitable for medium-temperature carbonitriding for small molds with complex cavities. The carburizing holding time is 5 to 10 hours, which should be selected according to the requirements for the thickness of the carburizing layer. The carburizing process is suitable to adopt the graded carburizing process, that is, the high temperature stage (900 ~ 920 ℃) is mainly to quickly infiltrate carbon into the surface of the part; the medium temperature stage (820 ~ 840 ℃) is mainly to increase the thickness of the carburized layer. A uniform and reasonable carbon concentration gradient distribution is established in the carburized layer, which is convenient for direct quenching.
(4). The quenching process after carburizing is different according to the steel type. After carburizing, it can be used respectively: reheating and quenching; direct quenching after graded carburizing (such as alloy carburizing steel); direct quenching after medium temperature carbonitriding (such as industrial Small precision molds formed by cold extrusion of pure iron or low-carbon steel); air-cooled quenching after carburizing (such as large and medium-sized molds made of high-alloy carburizing steel).
2. Heat treatment of hardened steel plastic mould
(1). For molds with complex shapes, heat treatment should be carried out after rough machining, and then finish machining can ensure the minimum deformation during heat treatment. For precision molds, the deformation should be less than 0.05%.
(2). The surface requirements of the plastic mold cavity are very strict, so it is necessary to ensure that the surface of the cavity is not oxidized, decarburized, corroded, or overheated during the quenching and heating process. It should be heated in a protective atmosphere furnace or in a salt bath furnace after strict deoxidation. If an ordinary box-type resistance furnace is used for heating, a protective agent should be applied to the cavity surface, and the heating speed should be controlled at the same time. Cooling medium, control the cooling rate to avoid deformation, cracking and scrapping during the quenching process. Generally, hot bath quenching is better, and pre-cooling and quenching can also be used.
(3). After quenching, it should be tempered in time. The tempering temperature should be higher than the working temperature of the mold. The tempering time should be sufficient. The length depends on the mold material and section size, but at least 40-60 minutes.