How many types of mold maintenance are there? As the most important molding equipment for the processing of injection products, the quality of the mold is directly related to the quality of the product. Moreover, since the mold occupies a large proportion in the production cost of injection molding, its service life directly affects the cost of Injection molding products. Therefore, it is a very important task to improve the quality of injection molds, maintain and maintain them well, and extend their service life.
Table of Contents
Toggle1.Maintenance of molds before production
1). It is necessary to clean the oil and rust on the surface of the mold, and check whether there are foreign objects in the cooling water holes of the mold, and whether there is no waterway.
2). It is necessary to check whether the arc in the mold rubber sleeve is damaged and whether there is any residual foreign matter;
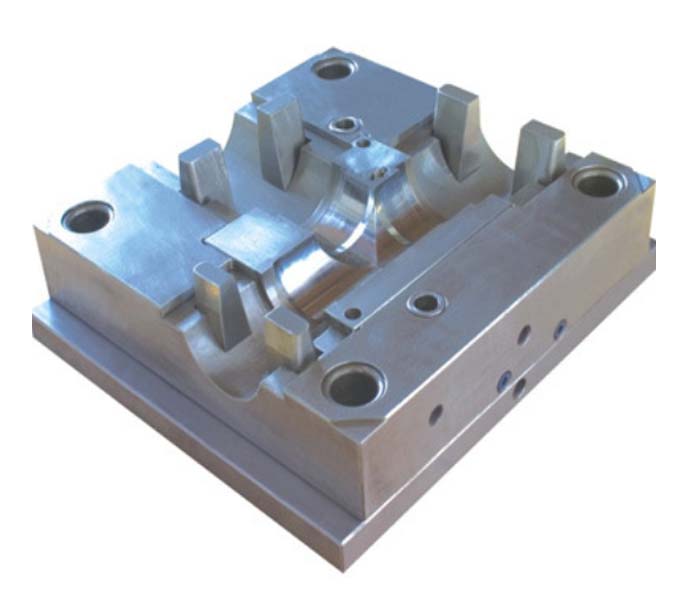
3). Whether the screws of fixed template of the mold and the clamping clamp are tightened, etc.;
4). After the mold is installed on the injection machine, the empty mold must be run first. Observe whether the movement of each part is flexible, whether there is any abnormal phenomenon, whether the moving parts such as guide post, ejector rod and row position are worn, whether the lubrication is good, whether the ejection stroke and opening stroke are in place, and whether the parting surface matches when the mold is closed. strict and so on.
2.Maintenance of molds in production
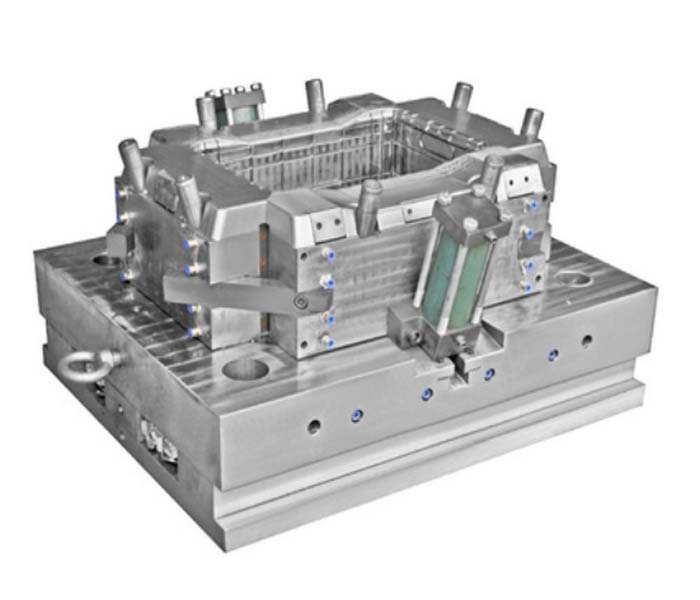
3). Before each mold clamping, you should pay attention to whether the cavity is cleaned, and no residual products or any other foreign objects are allowed to be left. It is strictly forbidden to use hard tools during cleaning to prevent bumping the surface of the cavity.
1). When the mold is in use, it is necessary to maintain the normal temperature, and it should not be cold and hot. Working at normal temperature can prolong the service life of the mold.
2). Check all the guide posts, guide sleeves, back needles, push rods, sliders, cores, etc. of the mold for damage every day. Observe at any time, check regularly, scrub in time, and regularly refuel and maintain them. Maintenance is done twice after get off work to ensure that these sliding parts move flexibly and prevent tightness from being bitten to death.
4). For molds with special requirements on the surface of the cavity, the surface roughness Ra is less than or equal to 0.2cm. It must not be wiped by hand or wiped with cotton wool. It should be blown with compressed air, or wiped gently with high-grade napkins and high-grade absorbent cotton dipped in alcohol. wipe.
5). Regularly clean the foreign matter glue, foreign matter, oil, etc. on the parting surface of the mold and the exhaust groove, and clean the parting surface and the runner surface twice a day. During the molding process, the injection mold often decomposes low molecular compounds to corrode the mold cavity, making the bright cavity surface gradually dull and reducing the quality of the product, so it needs to be scrubbed regularly, and alcohol or ketone preparations can be used for scrubbing. Dry in time after scrubbing.
6). Regularly check whether the waterway of mold is smooth and fasten all the fastening screws
3.Maintenance of the shutdown mold
1). When the operation leaves and needs to be stopped temporarily, the mold should be closed, and the cavity and core should not be exposed to prevent accidental damage. The downtime is expected to exceed 24 hours, and anti-rust oil should be sprayed on the surface of the cavity and core. Or mold release agent, especially in wet areas and rainy seasons, even if the time is short, anti-rust treatment should be done.
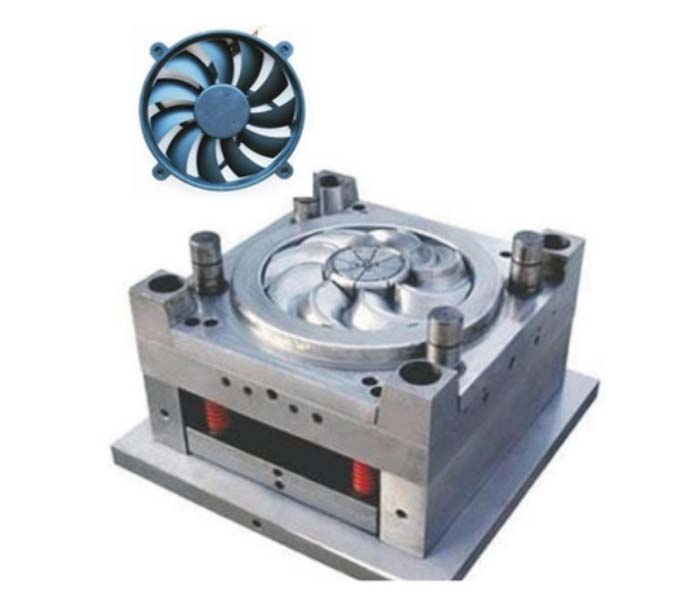
The water vapor in the air will reduce the mold and product surface quality. When the mold is used again, the oil on the mold should be removed, and it can be used after cleaning. If the mirror surface is required to be cleaned, the compressed air should be dried and then dried with hot air, otherwise it will ooze out during molding and cause defects in the product.
2). Turn on the machine after a short time shutdown. After opening the mold, check whether the limit position of the slider has moved, and the mold can only be closed if no abnormality is found. In short, you must be careful before starting the machine, and don’t be careless.
3). In order to prolong the service life of the cooling water channel, when the mold is out of use, the water in the cooling water channel should be removed immediately with compressed air, put a small amount of oil into the mouth of the nozzle, and then blow it with compressed air to make all cooling pipes have a layer. Anti-rust oil layer.
4). Carefully check the working state of each control component during the work, and strictly prevent the auxiliary system from abnormal, heating, and the maintenance of the control system is particularly important for the hot runner mold. After each production cycle, the rod heaters, belt heaters, and thermocouples should be measured with ohms and compared with the technical description data of the mold to ensure that their functions are intact. At the same time, the control loop may be tested by an ammeter installed in the loop. Hydraulic cylinder oil for core pulling should be emptied as much as possible, and the oil nozzle must be sealed to prevent the hydraulic oil leaking out or polluting the surrounding environment during storage and transportation.
5). If you hear abnormal noise from the mold or other abnormal conditions during production, you should stop the machine immediately for inspection. The mold maintenance personnel should conduct a patrol inspection of the molds that are running normally in the workshop, and if any abnormal phenomenon is found, they should deal with it in time.
6). When the operator is handing over the shift, in addition to the handover of production and the critical record of the process, the operator must also give a detailed account of the usage of the mold.
7). When the mold has completed the number of products produced, and you want to get off the machine to replace other molds, the mold cavity should be coated with anti-rust agent, the mold and its accessories should be sent to the mold maintainer, and the last qualified product should be attached as a sample. send it to the maintenance staff together.
In addition, a list of mold usage should also be sent to fill in in detail what machine tool the mold is on, how many products are produced from a certain month and a certain day in a certain year, and whether the mold is in good condition now. If there is a problem with the mold, fill in the problem with the mold on the use sheet, put forward specific requirements for modification and improvement, and hand over an unprocessed sample to the custodian for reference when the mold worker repairs the mold.
8). After the machine is shut down, it is necessary to check whether there are residual rubber threads, foreign objects, etc. on the surface of the mold.
4.Mould storage
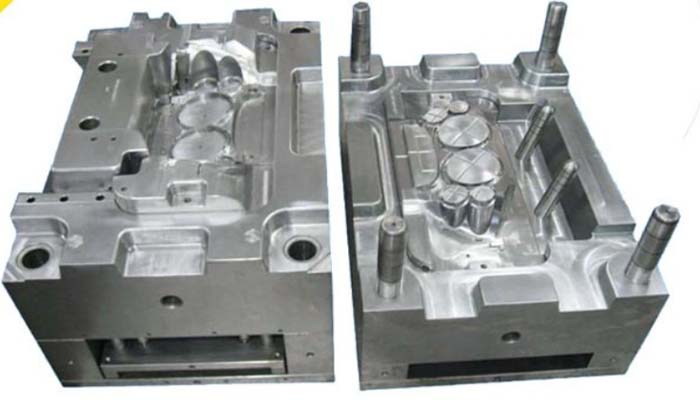
A mold library should be set up, special personnel should be set up for management, and mold files should be established. If possible, computer management of molds should be implemented. The mold warehouse should choose a low humidity and ventilation place, and the temperature kept below 70%.
If the humidity exceeds 70%, the mold will easily rust. The mold should be stored on the shelf, and pay attention to corrosion prevention and dust prevention.