How to make a good medical test tube mould? As one of the common medical consumables, plastic test tubes are used in a large amount.The market demand for medical test tubes molds are also increasing day by day, and more and more companies have turned their investment targets to the medical consumables market. So how to make a medical test tube mold? Based on its own medical mold manufacturing experience, WS Mould will give you some reference.
If you want to truly make a pair of precision medical molds for customers, early product risk assessment, mold flow To do a good medical test tube, you have to make a good test tube mold. The difficulty of making test tube molds lies in a series of problems such as eccentricity, low precision, and low pass rate. Such test tubes cannot meet the technical standards of medical devices.
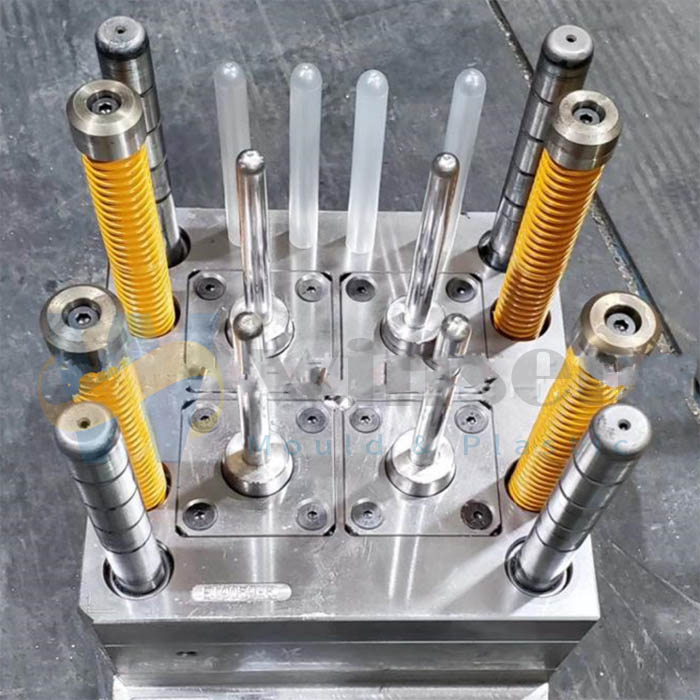
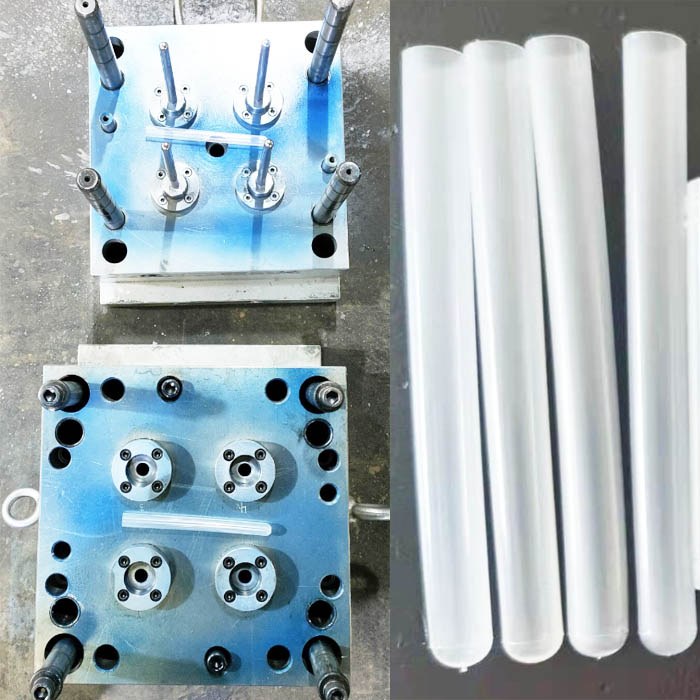
Table of Contents
ToggleTest Tube Mold Steel
The mold steel is made of stainless steel imported from Germany, which greatly increases the life of the mold; the mold base is also changed to high-quality pre-hardened steel, which has higher hardness and better flatness! At the same time, after the core cavity is mirror polished, the surface of the test tube can achieve a higher smoothness.
Gate selection of plasstic test tube molds
The more the number of test tube mold cavities, the greater the difficulty coefficient. The molten material in the cavity needs to be cooled quickly after injection molding to avoid eccentricity. Therefore, the temperature control balance of the gate is very critical. The WINSEN test tube mold adopts the self-developed Arnold needle valve hot runner gate with high design precision, and the gate is convenient for rapid injection molding and tight sealing.
Cooling system of Vacuum blood collection tube mould
The large nozzle cooling system is used to enter and exit the water to achieve rapid cooling, and the melt in the cavity is cooled evenly to avoid the eccentricity problem of the product.
Interchangeable design of Medical Test Tube Mould
Multi-cavity test tube molds can achieve interchangeable functions, which can reduce repeated investment costs and follow-up maintenance costs. The core of WINSEN test tube mold adopts independent self-locking structure, which can realize the exchange of product size, gram weight and wall thickness.
Processing equipment for PP and PET test tube molds
The mold steel is made of stainless steel imported from Germany, which greatly increases the lifThe most important thing for the test tube mold is the wall thickness control of the product, which cannot be eccentric. Therefore, the parallelism of each template and the concentricity of the hole position of the insert are very high. The traditional process uses a boring machine, but the accuracy is difficult to control. WINSEN switched to coordinate grinding to ensure the parallelism of template processing and the concentricity of inserts within 0.01mm.
WS Mould is a leader in the manufacture of disposable medical device moulds. The company specializes in the research and development, production, sales and service of disposable medical consumable moulds. WS MOLD has a very good understanding of the development of medical consumables in China at this stage, and is familiar with the product use and requirements of many medical consumables. It can provide customers with and assist in improving the complete mold configuration plan for the production of disposable medical devices. How to make a good precision mold is a problem that many mold manufacturers will face.
If truly make a pair of precision medical molds for customers, early product risk assessment, mold flow analysis, rigorous design, precise processing, and skilled assemblers are all essential, and mold manufacturers need to do a good job of it. Every step, so as to make a pair of precision medical product molds and win the trust of customers.
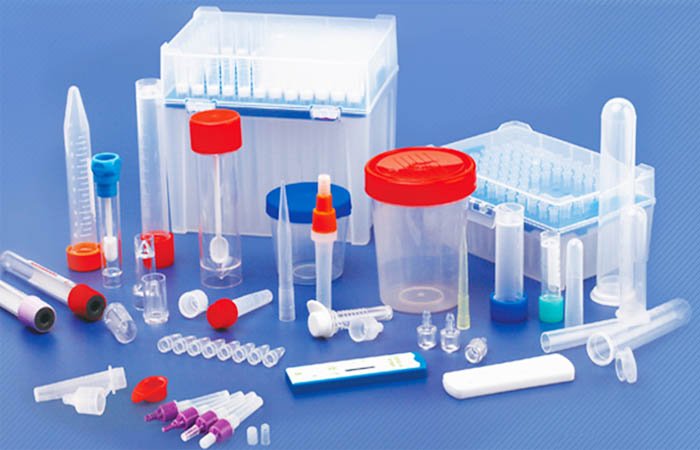

After receiving the customer’s medical product design, WS mold will convene all relevant technical personnel to analyze and evaluate its shortcomings and problems that may be encountered during processing, such as feasibility analysis of plastic parts molding, mold design and processing technology feasibility Analysis, etc., to optimize the design of plastic parts and molds as comprehensively as possible, can prevent and avoid most of the problems that may be encountered in mold production in advance. This also avoids unnecessary time waste and plaster-type mold repairs in the later stage.
Pay attention to mold flow analysis before medical mold design. In the era of data, making precision medical molds requires professional software analysis, and makes full use of analysis data to guide mold design. A good mold flow analysis can correctly design the mold, reduce the design and manufacturing cost, and improve the molding quality of the product.
For more medical molds design and making please contact