How to solve injection parts stick to the mold ? The product sticks to the cavity, which is relatively common in our mold factory when trying out the mold, and it is relatively simple to handle. If the mold is pulled to the plastic factory, it will be a little more troublesome to deal with, because it has to go through the approval process one by one.
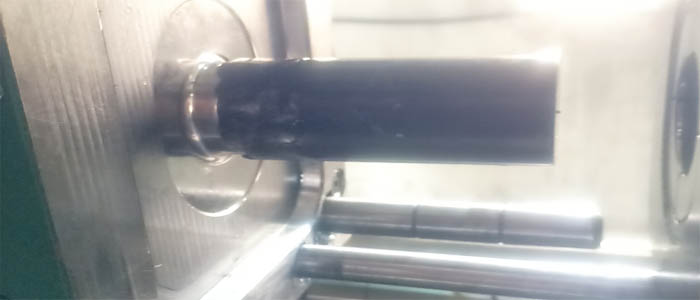
How to solve injection parts stick to the mold
When injection-molded parts stick to the mold, it can be a challenging issue to resolve. Here are some steps you can take to address the problem:The injection parts is sticky to the cavity because there is no place to be stressed on the core side, so it is good to increase the stress-bearing place.
1. Add a few undercut ribs on the core side
The simplest and most effective method is to add a few undercut ribs on the core side, so that the sub-core will not stick to the cavity when it is stressed in some places. Generally, the core does not affect the inside of the product. Exterior.
2. The specific problems are analyzed in detail
The specific problems are analyzed in detail. Sometimes spray the mold release agent to see the effect and judge whether it is the cause of the polishing. Sometimes the light is too bright, but it is easier to stick to the cavity. The cavity waterway is very effective, the cavity side is too cold, and sometimes it is easy to fix the cavity.
3. Use the bullet on the cavity side
Use the bullet on the cavity side, but check whether the bullet block has a force-bearing position, and there is a line on the cavity side whether the customer can accept it, so the limitations are relatively large.
4. Open the mold with a small cavity,
Open the mold with a small cavity, press the spring on the side of the cavity, and open the mold on the side of the cavity before the mold is opened.
5. Review mold release agent
Ensure that an appropriate mold release agent is being used. Mold release agents help create a barrier between the mold surface and the injected material, facilitating easy part ejection. Confirm that the mold release agent is compatible with the material being injected and that it is applied correctly and uniformly.
6. Optimize mold temperature
Adjusting the mold temperature can help prevent parts from sticking. If the mold is too cold, the material may not solidify or shrink adequately, leading to adhesion. If the mold is too hot, the material can become excessively soft or partially melted, also causing sticking. Experiment with different mold temperatures to find the optimal range for your specific material.
7. Check injection parameters
Evaluate the injection molding parameters such as injection speed, pressure, and cooling time. Inadequate cooling time can result in semi-solid parts that adhere to the mold. Adjust the parameters to ensure proper cooling and solidification of the injected material.
8. Enhance mold surface finish
A smooth mold surface can aid in part ejection. Evaluate the mold surface finish and consider enhancing it, if necessary. Polishing or applying a suitable coating to the mold surface can reduce friction and adhesion, making it easier for the parts to release.
9. Evaluate draft angles
Draft angles are inclined surfaces incorporated into the design of the mold and parts. These angles facilitate the removal of the parts from the mold. Insufficient draft angles or improper design can cause parts to stick. Ensure that the draft angles are appropriate for the material and part geometry.
10. Optimize cooling system
nsufficient cooling can contribute to parts sticking in the mold. Verify that the cooling system is functioning correctly and providing adequate cooling to the mold. Enhancing the cooling system by adjusting coolant flow, using cooling channels or inserts, or employing more efficient cooling methods can help alleviate the issue.
11. Consider mold venting
Inadequate venting can trap air or gases, leading to part adhesion. Evaluate the mold for proper venting and ensure that any trapped air can escape during the injection process. Incorporate additional vents or improve the existing venting system to facilitate the release of air and gases.
12. Verify material properties
Some materials may inherently exhibit higher levels of adhesion or stickiness. Review the material properties and consult with material suppliers to ensure that the selected material is appropriate for the application. Consider alternative materials that have better release characteristics.
13. Inspect and maintain the mold
Regularly inspect the mold for any signs of damage, wear, or contamination. Address any issues promptly by repairing or cleaning the mold. Ensuring that the mold is in good condition can help prevent sticking issues.
14. Optimize part ejection mechanism
Assess the ejection mechanism of the molding machine. The ejection pins or mechanisms should be correctly positioned and provide sufficient force to eject the parts without causing damage. Adjusting the ejection mechanism can assist in smooth part removal.
Therefore, the problem of product sticking cavity should be done as much as possible in the product design stage and dealt with accordingly. Before the mold design, let the mold master participate in the review to see whether the product will hold the cavity and how to change the product. This will make it much easier later on.