Strategies to improve injection mold production efficiency
In modern manufacturing, the production efficiency of injection molds directly affects the competitiveness and economic benefits of enterprises. Improving the production efficiency of injection molds can not only reduce production costs, but also shorten the delivery cycle and meet the market’s demand for fast delivery. This article will explore how to improve the production efficiency of injection molds from multiple aspects.
Table of Contents
ToggleOptimize mold design
Mold design is the core link of injection molding production, and reasonable mold design can significantly improve production efficiency. First, by using advanced CAD/CAM technology and mold flow analysis software, the structure and function of the mold can be optimized to reduce waste and errors in the production process. Secondly, designers should fully consider the structural characteristics of the product, simplify the mold design as much as possible, and reduce the difficulty of manufacturing. In addition, optimizing the cooling system design of the mold is also key. For example, the use of a water-cooled heat dissipation system can effectively reduce the mold temperature and improve the cooling efficiency, thereby shortening the production cycle.
- Improve mold structure: By optimizing the mold parting surface, gate position, runner design, etc., reduce product defects (such as material shortage, flash, etc.), improve product quality and production stability.
- Use hot runner technology: Hot runner molds can reduce cooling time and avoid waste generated by cold runners, thereby shortening the molding cycle and improving production efficiency.
- Optimize gate and runner design: Select the appropriate gate type and location according to the type and shape of the plastic part, optimize the design of the runner system, reduce pressure loss and heat loss, and improve the fluidity and uniformity of the melt.
Reduce the molding cycle of plastic parts, rationally layout the mold structure, and ensure that the size and shape of each part of the mold match the model and production capacity of the injection molding machine to reduce stress concentration and increase service life.
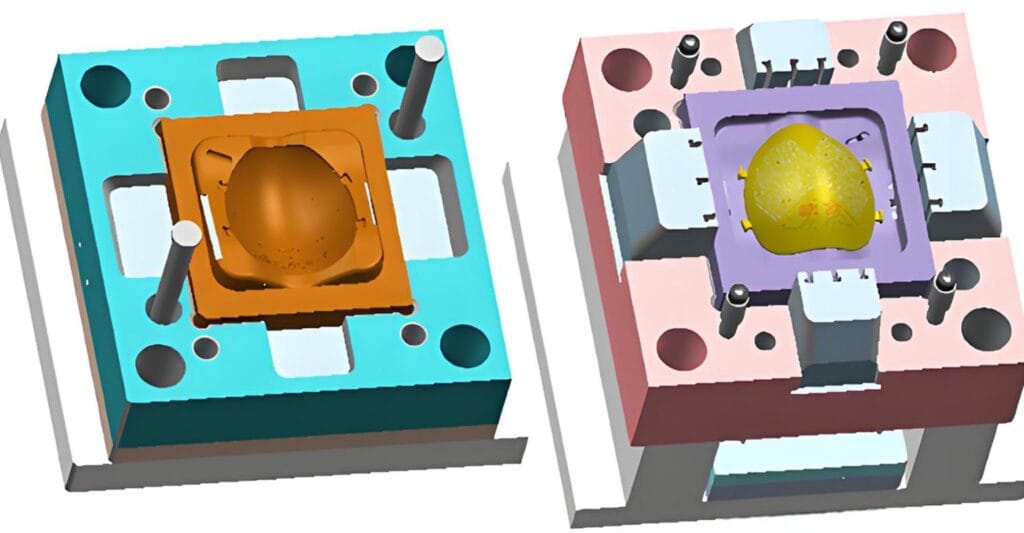
Use high-quality materials
Choosing high-quality mold materials is an important guarantee for improving production efficiency. High-quality materials can not only improve the wear resistance and corrosion resistance of the mold, but also extend the service life of the mold and reduce the frequency of maintenance and replacement. For example, the use of high-strength and high-wear-resistant mold steel can significantly reduce the wear rate of the mold and ensure the stability of the production process.
Choose mold materials with high strength, wear resistance, and corrosion resistance to extend mold life and reduce downtime caused by mold wear.
Select mold materials suitable for injection molding process to improve the service life and stability of the mold.
Introduce automation and intelligent technology
Automation and intelligence are the development trend of modern manufacturing industry and the key means to improve the production efficiency of injection molds. By introducing automated equipment, such as automatic feeders, robot arms, etc., manual operations can be reduced and production efficiency and stability can be improved. In addition, the application of intelligent equipment and information technology, such as real-time monitoring and data analysis, can help enterprises optimize production processes and reduce human errors.
- Introducing automated equipment: Using robots to remove and transport products, reducing manual intervention and improving production efficiency.
- Applying intelligent systems: Through data collection and analysis technology, real-time monitoring and optimization of the production process can be achieved to reduce human operational errors.
Use highly automated processing equipment and technology to improve production efficiency and quality.
Optimize process parameters
The optimization of injection molding process parameters is an important part of improving production efficiency. By adjusting parameters such as injection molding temperature, pressure, speed and cooling time, the injection molding cycle can be shortened and product quality can be improved. For example, optimizing the cooling process and using rapid cooling or water cooling can significantly shorten the production cycle.
- Adjust process parameters: According to the requirements of plastic materials and products, optimize the process parameters such as injection temperature, pressure, speed and cooling time to reduce the injection cycle.
- Improve the cooling system: Use efficient cooling methods (such as water cooling, air cooling) or optimize the cooling channel design to shorten the cooling time.
Ensure injection speed, pressure, etc., ensure good equipment performance, and maintain stable temperature conditions
Strengthen equipment maintenance and management
The normal operation of equipment is the basis of production efficiency. Regular maintenance and care of injection molding equipment, including cleaning, lubrication and replacement of worn parts, can reduce equipment failures and downtime. At the same time, according to production needs and technological development, timely update equipment and introduce more efficient and energy-saving injection molding machines.
- Regularly maintain equipment: Establish a complete equipment maintenance system, regularly maintain and overhaul injection molding machines and molds to reduce downtime caused by equipment failure.
- Introduce advanced equipment: Use high-speed, high-precision, energy-saving and environmentally friendly injection molding machines to improve production efficiency.
Improve employee skills and management level
Employees are the key factors in the production process. Improving employee skills and management level can significantly improve production efficiency. Through regular training, employees can better master injection molding technology and operating procedures and reduce errors in production. In addition, establishing a sound quality management system and incentive mechanism can stimulate the enthusiasm and creativity of employees.
- Improve employee skills: Train employees on injection molding technology and operating procedures to reduce operational errors and improve production efficiency.
- Establish an incentive mechanism: Stimulate employee enthusiasm and creativity through a reward system.
Adopt information management system to monitor the production process in real time, optimize the production process and improve production efficiency.
Optimize supply chain management
Optimizing supply chain management is an important means to improve the production efficiency of injection molds. By integrating various links in the supply chain, companies can optimize resource allocation, reduce operating costs, and improve production efficiency.
- Select high-quality suppliers: cooperate with reliable raw material suppliers to ensure timely supply and stable quality of raw materials.
- Manage inventory reasonably: optimize material allocation and warehouse management to reduce material waiting time at the production site.
Control scrap rate
In the production of injection molds, controlling the scrap rate can not only reduce costs, but also significantly improve production efficiency. Reducing scrap means less waste of raw materials, less downtime in the production process, and improved utilization of equipment and manpower. By optimizing mold design, strictly controlling process parameters, strengthening quality inspection and equipment maintenance, the generation of scrap can be effectively reduced. This not only improves the product qualification rate, but also shortens the production cycle and improves overall production efficiency. Therefore, controlling the scrap rate is an important means to improve the production efficiency of injection molds.
- Optimize molds and processes: Reduce product defects and scrap rate by improving mold design and optimizing process parameters.
- Strengthen quality control: Establish a complete quality management system to ensure that product quality meets requirements.
Strengthen the cooling and heating system of the mold
Maintain stable temperature conditions, arrange cooling pipes reasonably, ensure uniform temperature of each part of the mold, and shorten cooling time.
Precise measurement and adjustment
Accurately measure the size and position of each part of the mold, adjust the error in time, and ensure the stability and accuracy of the production process.
Simplify mold structure
Adopt modular design concept to reduce manufacturing cost and maintenance difficulty; optimize mold opening and closing action, improve mold opening and closing speed and stability, and reduce mold opening and closing time.
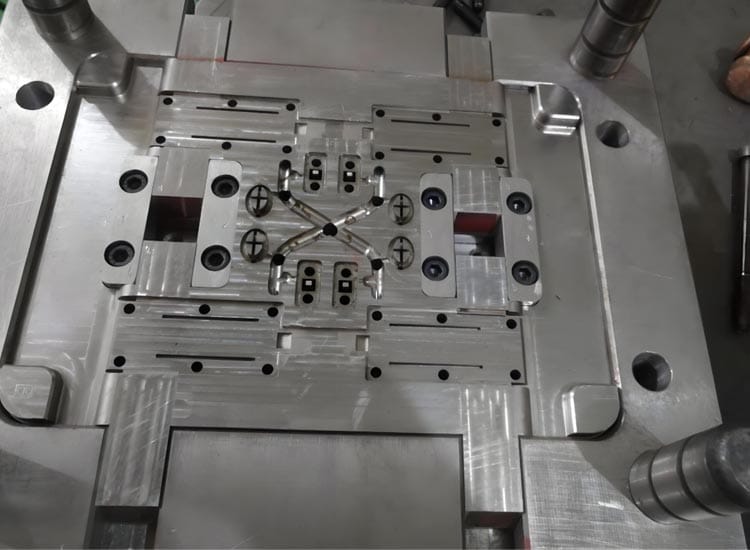
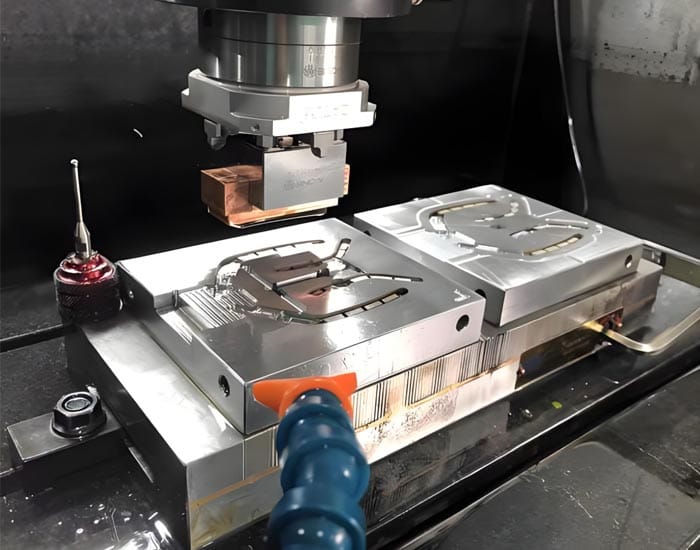
Implement lean production
Lean production is a systematic management method that aims to eliminate waste and non-value-added activities in the production process. By optimizing the production process and reducing unnecessary processes and waiting time, enterprises can significantly improve production efficiency. For example, reasonable arrangement of production plans, optimization of material allocation and warehousing management can reduce the waiting time of materials at the production site.
Innovation and continuous improvement
In a highly competitive market, continuous innovation is the key to maintaining competitiveness. Enterprises should encourage employees to put forward improvement suggestions and continuously optimize process flow, equipment configuration and management methods. For example, some companies have significantly improved the heat dissipation performance and production efficiency of molds through innovative cooling system design.
Check the key components of the mold
Regularly checking the key components of the mold is an important part to ensure its normal operation. Here are some parts and inspection contents that need to be focused on:
- Mold surface: Check the mold surface for scratches, wear or cracks. Minor scratches can be repaired by polishing, but serious damage may require replacement of mold components.
- Cooling system: The cooling system is an important part of the injection mold, and its performance directly affects the molding cycle and product quality. Regularly check whether the cooling channel is blocked or leaking, and ensure that the flow and temperature of the coolant meet the design requirements.
- Heating element: For hot runner molds, the performance of the heating element is crucial. Regularly check whether the heating rod, thermocouple and other components are working properly to ensure the accuracy of temperature control.
- Sliders and ejectors: Sliders and ejectors are active parts in the mold and are prone to wear due to frequent movement. Check the lubrication of these parts, add or replace lubricating oil in time to ensure their smooth movement.
To effectively improve the production efficiency of injection molds, we need to start from multiple dimensions. To sum up, through these comprehensive measures, the production efficiency of injection molds will be significantly improved, creating greater economic benefits for the enterprise.
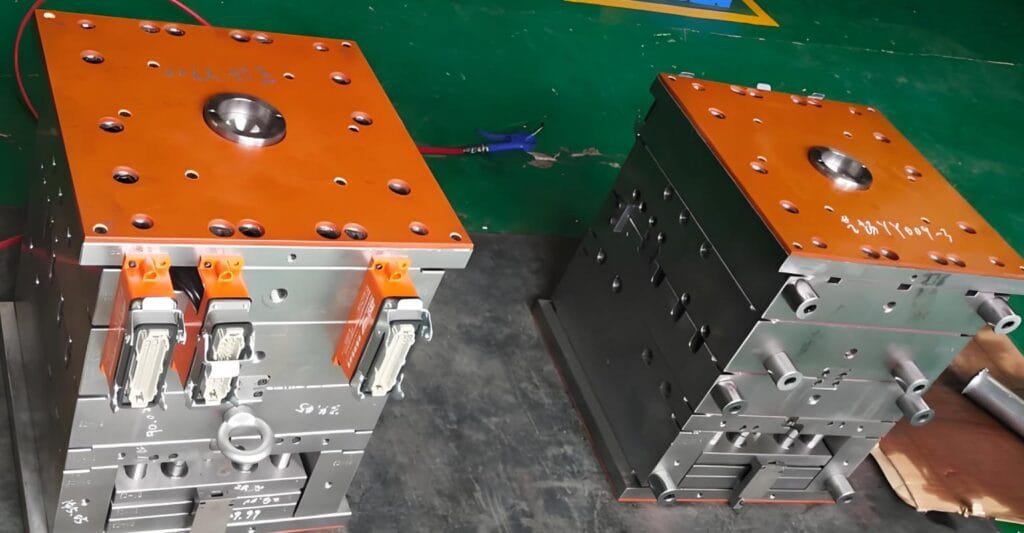
Improving the production efficiency of injection molds requires comprehensive consideration of design, materials, equipment, processes, personnel, and management. By optimizing mold design, using high-quality materials, introducing automation and intelligent technology, optimizing process parameters, strengthening equipment maintenance and management, improving employee skills and management level, implementing lean production, and continuous innovation, companies can significantly improve production efficiency, reduce costs, and enhance market competitiveness.