Methods to improve the production efficiency of injection molds
With the development of industry, injection molds, as an important tool for production and manufacturing, have been widely used in many fields. In order to improve the production efficiency of injection molds, the following are some commonly used improvement strategies and methods.
Table of Contents
ToggleMold design optimization
By optimizing the structure and size of the injection mold, the energy consumption and material loss in the production process can be reduced and the production efficiency can be improved. For example, by reducing the mold wall thickness and optimizing the layout of the cooling channel, the injection molding cycle can be accelerated and the production efficiency can be improved.
By fine-tuning the mold structure and size, such as reducing wall thickness and improving the cooling system, the molding cycle can be shortened.
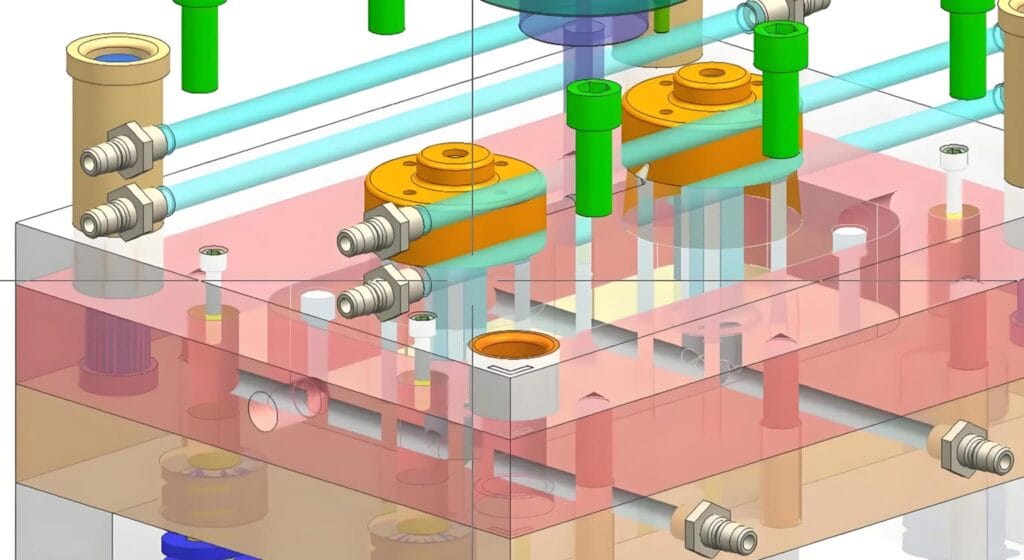
Material selection optimization
Choosing the right material is crucial to improving the production efficiency of injection molds. Using high-quality mold materials can extend the service life of the mold and reduce the number of maintenance times, thereby improving production efficiency. At the same time, choosing the right injection molding raw materials can speed up the injection molding cycle and improve production efficiency while ensuring the quality of the finished product.
Selecting the right mold and injection molding material is equally important. High-quality materials can extend the life of the mold and improve production continuity.
Use of advanced equipment and technology
he use of advanced equipment and technology in the production process of injection molds is an important means to improve production efficiency. For example, the use of high-precision CNC machining equipment can improve the processing accuracy and efficiency of the mold; the use of advanced injection molding machinery and equipment can speed up the molding cycle and improve production efficiency.
The introduction of advanced equipment and technologies, such as high-precision CNC machining and intelligent injection molding machines, can significantly improve processing efficiency and molding speed.
Automated production line
Establishing an automated injection mold production line can achieve continuity and efficiency in the production process. By using automated equipment for raw material delivery, mold loading and unloading, and product collection, it can reduce manual operation time and labor intensity and improve production efficiency.
Build an automated production line, reduce manual intervention, and achieve efficient automation of the production process.
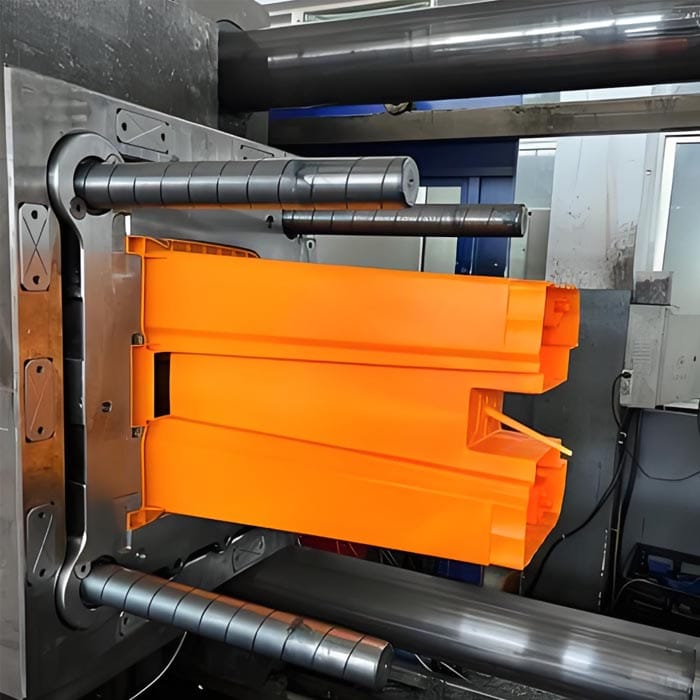
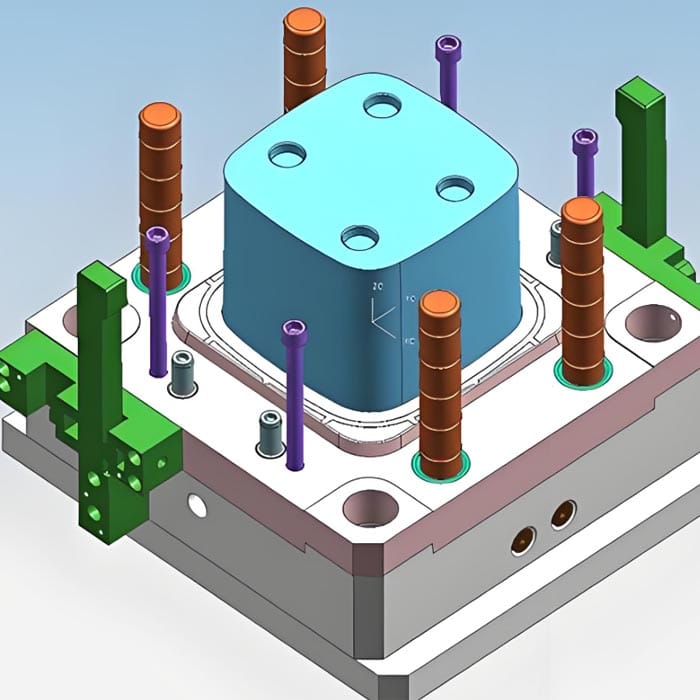
Reasonable management and scheduling
The production process of injection molds needs to be reasonably managed and scheduled to ensure maximum production efficiency. By formulating scientific and reasonable production plans, flexible production scheduling and efficient production monitoring, waiting time and downtime in production can be reduced and production efficiency can be improved.
Scientific management scheduling and preventive maintenance are also important links to improve efficiency. They can ensure the rationality of production planning and the stable operation of molds.
Training and skill improvement
Operators in the production process of injection molds need to have certain professional knowledge and skills. Through training and skill improvement, the operating skills and work efficiency of operators can be improved. At the same time, the maintenance and troubleshooting of injection molds also require professionals, who need to have relevant maintenance knowledge and skills.
Train operators to improve their professional skills, optimize the quality control system and reduce the defective product rate.
Optimize quality control
Optimizing quality control can avoid repeated production and returns caused by poor product quality. By establishing strict quality control standards and process control, and strengthening the inspection and monitoring of raw materials, molds and finished products, the generation of defective products can be reduced and production efficiency can be improved.
Application of innovative technologies
The application of innovative technologies in the production process of injection molds can improve production efficiency. For example, by applying rapid prototyping technology and rapid mold manufacturing technology, the mold manufacturing cycle can be shortened and production efficiency can be improved. At the same time, the injection mold industry can also realize the digitization and intelligence of the production process by introducing intelligent manufacturing and Internet of Things technologies, and further improve production efficiency.
Actively explore innovative technologies, such as rapid prototyping and intelligent manufacturing, while establishing solid partnerships to jointly promote continuous improvement of production efficiency.
Establish a partnership
Establish a good partnership with suppliers, customers and other partners to jointly promote the improvement of injection mold production efficiency. By cooperating with suppliers to optimize raw materials and supply chains, production efficiency can be improved; cooperating with customers to adjust product design and demand can reduce production uncertainty and improve production efficiency.
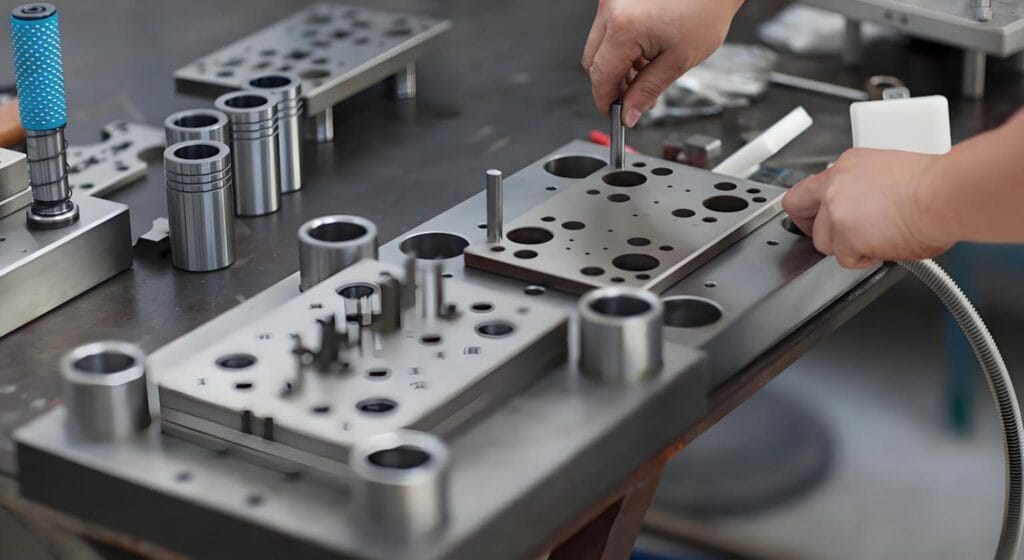
In short, improving the production efficiency of injection molds requires comprehensive consideration of injection mold design, material selection, equipment and technology application, management and scheduling, maintenance and training, etc. By comprehensively applying the above strategies and methods, the production efficiency of injection molds can be effectively improved, the competitiveness and economic benefits of enterprises can be improved, and greater economic benefits can be created for enterprises.