Injection mold precision and durability: Why are they so important?
In the injection molding industry, mold precision and durability directly affect product quality, production costs and corporate competitiveness. High-precision molds can ensure product size stability and perfect appearance, while high durability can reduce downtime and maintenance costs. This article will explore the importance of injection mold precision and durability and share optimization strategies.
Table of Contents
ToggleInjection mold precision: the key to product quality
What is mold precision?
Mold precision usually refers to whether key parameters such as mold dimensional tolerance, surface finish, and fit clearance meet design requirements. High-precision molds can ensure the consistency of each batch of injection molded products and reduce the need for post-processing.
Common problems of insufficient precision
- Dimensional deviation: makes product assembly difficult and affects function (such as electronic connectors and automotive parts).
- Flash (burr): inaccurate fit of parting surface or ejector position, increasing post-processing costs.
- Surface defects: such as shrinkage marks and flow lines, which affect appearance quality (such as consumer electronic products).
How to ensure mold precision?
- Precision machining: CNC milling, EDM, mirror polishing and other processes are used.
- Material selection: Use mold steel with high hardness and low thermal deformation coefficient (such as S136, NAK80).
- Temperature control: Avoid thermal expansion errors caused by mold temperature fluctuations (within ±1°C).
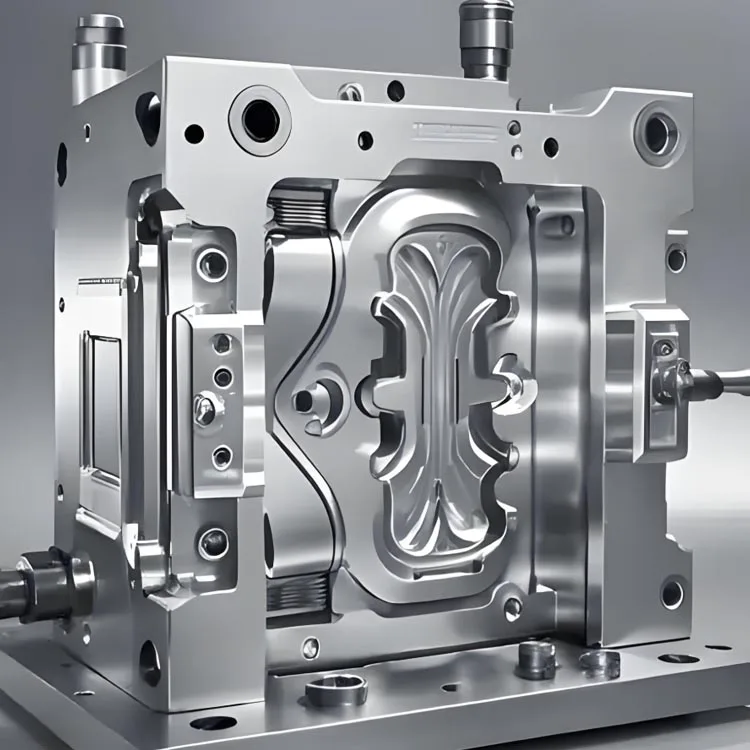
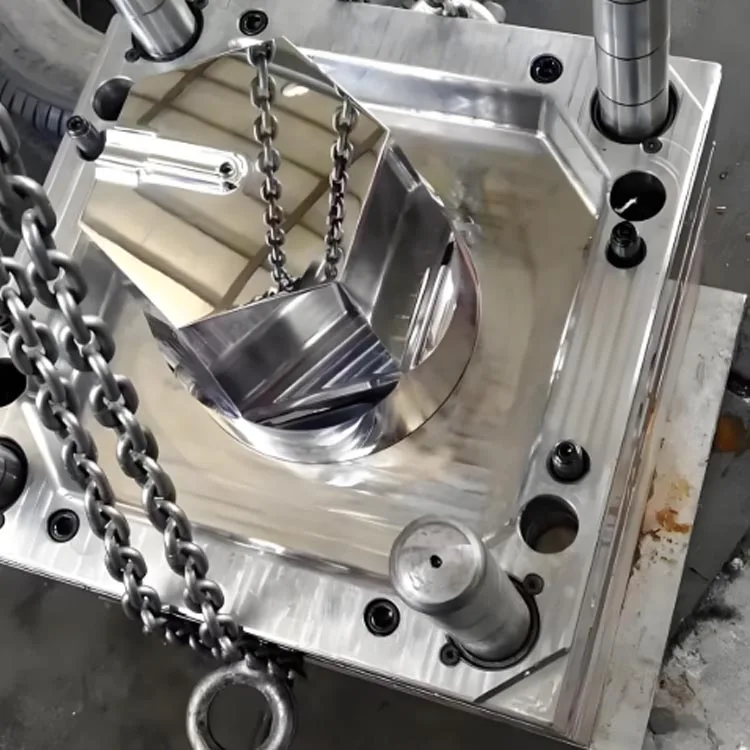
Why is the precision of injection molds important
Ensure product quality: The precision of injection molds directly affects the size and appearance quality of the final product. High-precision molds can produce parts that meet strict tolerance requirements, ensuring the dimensional consistency and functionality of the product.
Improve production efficiency: High-precision molds can reduce scrap and rework rates in the production process, thereby improving overall production efficiency. Efficient mass production can be achieved through precise mold design and manufacturing.
Meet complex design needs: Injection molding can produce parts with complex geometries and details, such as thin walls, threads, and undercuts. High-precision molds are the key to achieving these complex designs.
Why is the durability of injection molds important
Extend service life: Durable injection molds can maintain good working conditions for a long time, reducing the need for frequent mold changes, thereby reducing production costs.
Reduce maintenance costs: Durable mold design and material selection can reduce the risk of wear and damage, and reduce the frequency and cost of daily maintenance and repairs.
Improve production stability: Durable molds can maintain stable operation in harsh environments of high temperature, high pressure and mechanical friction, ensuring the continuity and consistency of the production process.
Adapt to complex production environments: Injection molds are affected by a variety of factors such as chemical erosion, thermal stress and mechanical wear during the production process. Durable mold design and material selection can effectively meet these challenges and ensure the long-term performance of the mold.
Durability of injection molds: the core factor affecting production costs
Determinants of mold life
Steel quality: High-quality mold steel (such as H13, P20) has stronger wear and corrosion resistance.
Heat treatment process: Quenching, nitriding and other treatments can improve surface hardness (HRC 48-52).
Determinants of mold life
- Steel quality: High-quality mold steel (such as H13, P20) has stronger wear and corrosion resistance.
- Heat treatment process: Quenching, nitriding and other treatments can improve surface hardness (HRC 48-52).
- Cooling system design: Uniform cooling can reduce thermal stress and extend mold life.
Common causes of premature mold failure
- Wear: High-frequency contact parts such as gates and ejectors are prone to wear.
- Corrosion: Certain plastics (such as PVC) decompose acidic substances and corrode the mold.
- Fatigue cracking: Long-term exposure to alternating stress causes mold cracking.
How to improve mold durability
- Surface treatment: Chrome plating, TD treatment, DLC coating and other methods enhance wear resistance.
- Optimize ejector system: Reduce ejector friction and avoid tearing the mold cavity.
- Regular maintenance: Clean, lubricate, and store in a rust-proof manner.
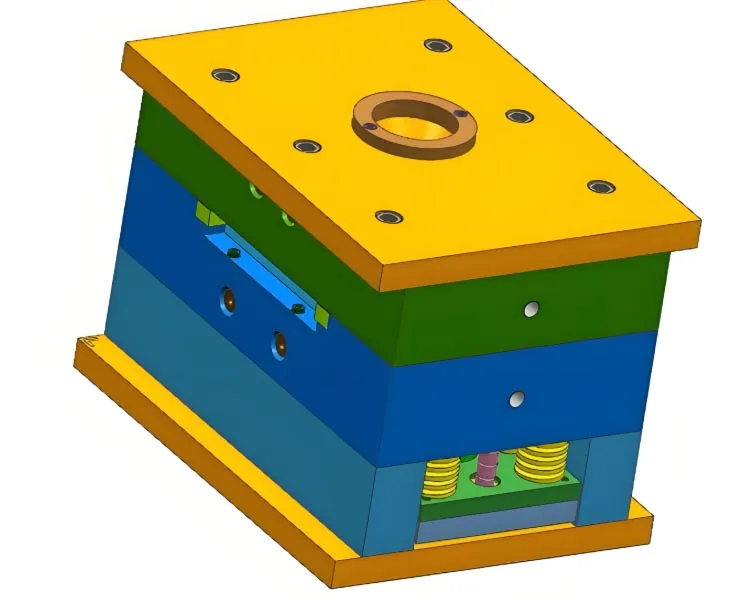
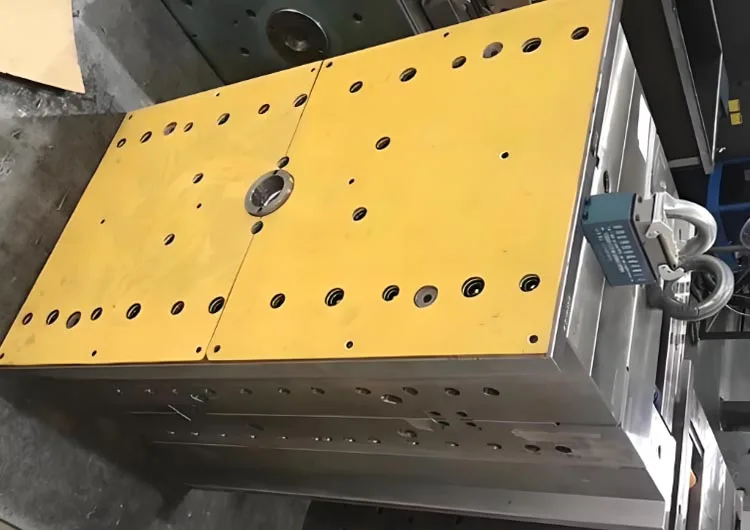
How to optimize high precision and high durability together
Design stage
Use **Moldflow** to optimize the pouring system and reduce local wear.
Use standardized mold frames (such as HASCO, DME) to ensure matching accuracy.
Manufacturing stage
Test mold verification after precision machining and adjust process parameters.
Perform hardness test on key components (such as sliders and inclined tops).
Production stage
Monitor the number of times the mold is used and formulate a preventive maintenance plan.
Record defect modes (such as burrs, dimensional tolerances) for targeted optimization.
Industry application cases
Medical industry: High-precision molds (±0.01mm) ensure that syringes and infusion connectors are burr-free.
Automotive industry: Long-life molds (more than 500,000 times) reduce the unit cost of bumpers and dashboards.
Investing in precision and durability is investing in competitiveness
Short term: High-precision molds reduce scrap rates and speed up delivery.
Long term: High-durability molds reduce unit costs and increase customer trust.
The precision and durability of injection molds are key factors affecting product quality, production efficiency and economic benefits. High-precision molds can ensure product consistency and the realization of complex designs, while durable molds can extend service life, reduce maintenance costs, and improve the stability of the production process. By optimizing mold design, selecting suitable materials, and implementing a strict maintenance plan, the comprehensive performance of injection molds can be significantly improved, thereby achieving efficient and economical production.
Does your injection molding project require a mold solution with higher precision and longer life? Welcome to contact our expert team to provide you with customized suggestions!