Mold processing design is a crucial for injection mould
In the injection molding industry, molds are the key tools to achieve product design, and the processing design of injection molds is the core link to ensure production efficiency, product quality and cost control. An excellent injection mold design can not only improve production efficiency, but also reduce scrap rate, extend mold life, and ultimately enhance the competitiveness of the enterprise. This article will explore the basic principles of injection mold processing design in depth to help you make more informed decisions in the mold design and manufacturing process.
Table of Contents
ToggleProduct-centered design concept
The design of injection molds begins with a deep understanding of the product. At the beginning of the design, designers need to work closely with product engineers to fully understand the product’s functions, appearance requirements, dimensional accuracy, and usage environment. For example, for products that require high-precision dimensions, mold design must consider higher processing accuracy and more sophisticated cooling systems; and for products with higher appearance requirements, it is necessary to optimize the mold’s surface treatment and demolding slope.
Case sharing: The shell of an electronic product requires a high-gloss surface. Our mold design team successfully achieved the product’s high-gloss effect by optimizing the mold’s polishing process and cooling system, while shortening the molding cycle.
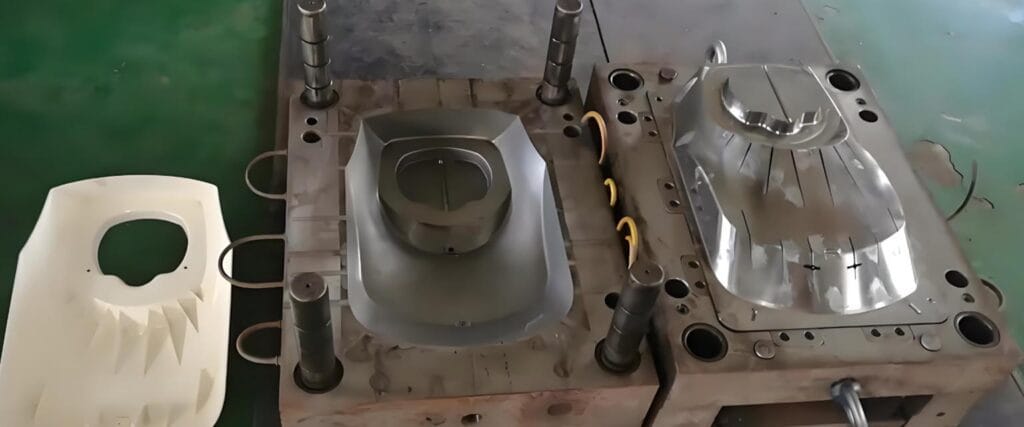
Reasonable layout of injection mould
At the beginning of mold design, the layout of the mold should be fully considered. Generally speaking, the mold should be designed according to the flow direction of the molten plastic ejected from the injection molding machine to reduce stress concentration and increase service life. At the same time, the various components of the mold should be reasonably distributed to avoid mutual interference and ensure the smoothness of the production process. In addition, the size and shape of the mold should match the model and production capacity of the injection molding machine to ensure production efficiency.
Simplify the structure of mold design and improve manufacturability. The complexity of the injection mold directly affects the processing difficulty and production efficiency. Therefore, the mold structure should be simplified as much as possible during design to reduce unnecessary complex features. For example, rationally plan the parting surface and avoid excessive inserts and slider designs, which can not only reduce the processing difficulty but also reduce the maintenance cost of the mold.
Design tips: Without affecting the product function, minimize the number of ribs on the product or optimize its layout, which can simplify the exhaust system design of the mold and improve the injection molding efficiency.
Structural optimization for injection mould
In terms of structural optimization, the design of injection molds should focus on the following aspects:
- 1. Demolding structure: A good demolding design can reduce the contact time between plastic products and molds and reduce the incidence of molding defects. Overly complex demolding structures should be avoided to avoid increasing the complexity and cost of the mold.
- 2. Gating system: The gating system is an important part of the injection mold, and its design should consider factors such as the type of plastic, molding temperature, and the properties of the mold material. Reasonable gate distribution can shorten the flow path of the molten plastic, reduce flow resistance, and increase molding speed.
- 3. Cooling system: The design of the cooling system is crucial to controlling the molding temperature and dimensional stability of plastic products. The cooling pipes should be arranged reasonably according to the shape and size of the plastic product to ensure uniform temperature of all parts of the mold.
Among them, cooling system optimization is the key to production efficiency. The cooling system is a vital part of injection mold design. A good cooling system can quickly take away the heat in the mold, shorten the molding cycle, and improve production efficiency. At the same time, uniform cooling can also reduce product deformation and internal stress, and improve product quality.
Design points:
The design of the cooling channel should be as evenly distributed as possible to ensure that the cooling speed of each part of the mold is consistent.
Use suitable cooling media (such as water or oil) and cooling methods (such as straight-through or spiral cooling channels).
Consider the thermal balance of the mold and add heating or cooling devices when necessary.
Practical application: An automotive parts production, we are as a experienced manufacturer can shortened the molding cycle by 20% and increased the product qualification rate by 15% by optimizing the mold cooling system.
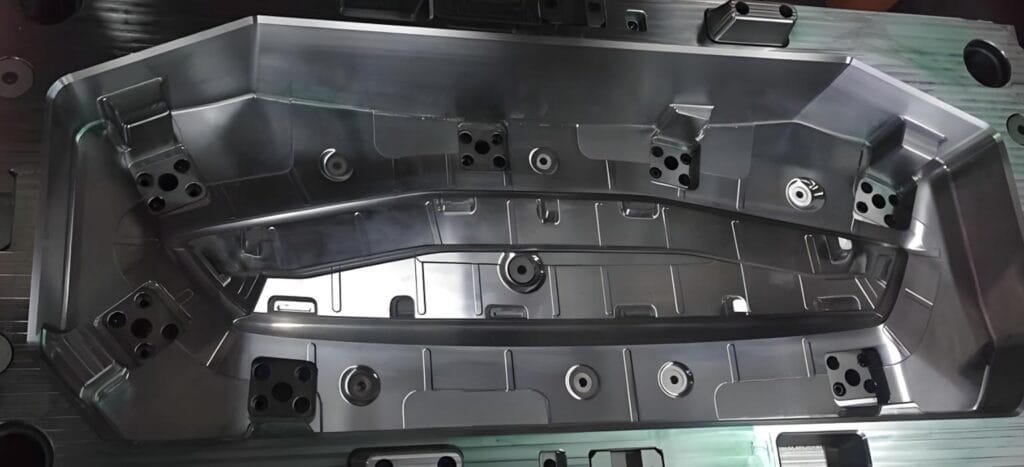
Improve efficiency for injection mould molding
Improving efficiency is one of the core goals of injection mold design. Here are some ways to improve efficiency:
1. Use advanced materials: Selecting mold materials suitable for the injection molding process can improve the service life and stability of the mold.
2. Automation: Using processing equipment and technology with a high degree of automation can improve production efficiency and quality.
3. Accurate measurement and adjustment: Accurately measuring the size and position of each part of the mold and adjusting the error in time can ensure the stability and accuracy of the production process.
4. Information management: Using an information management system can monitor the production process in real time, optimize the production process, and improve production efficiency.
Material selection: balance between durability and cost
The choice of mold material directly affects the service life and processing cost of the mold. For products with high production volume, high-strength and high-wear-resistant mold steels, such as P20 or H13, should be given priority. For some small batches or complex-shaped molds, aluminum alloys can be considered to reduce processing difficulty and cost.
Material comparison:
- Steel: strong durability, suitable for mass production, but high processing cost.
- Aluminum alloy: fast processing speed, low cost, but slightly inferior durability.
Design suggestions: When designing, choose mold materials reasonably according to the production volume and complexity of the product to avoid over-design.
Standardization and modular design
Standardization and modularization are effective means to improve mold design efficiency and reduce production costs. By adopting standardized mold components (such as ejector pins, guide pins, nozzles, etc.), the design and processing time can be shortened. At the same time, modular design can also improve the versatility and interchangeability of molds, making them easier to maintain and replace.
Actual case: WS mold factory shortened the design and processing cycle by 30% and reduced production costs by 15% by adopting standardized mold components.
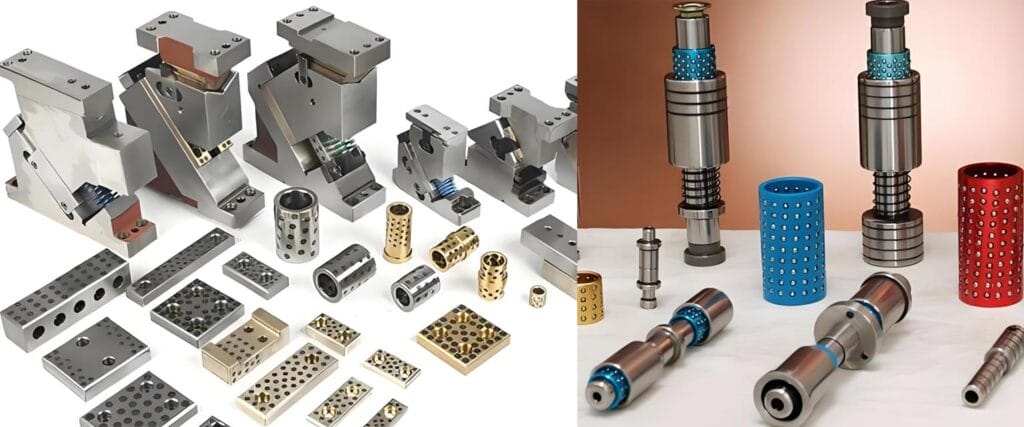
Compatibility of injection molding process
The design of injection molds should not only consider the shape and size of the product, but also the compatibility of the injection molding process. For example, the gate position and runner system should be reasonably designed to ensure that the plastic melt can evenly fill the mold cavity and reduce defects such as bubbles, shrinkage and weld lines.
Design tips:
- The gate position should be as close as possible to the thick wall area of the product to facilitate the flow of the melt.
- Optimize the runner design to reduce the heat loss of the melt in the runner.
Case sharing: We made toy mold reduced product shrinkage and improved product qualification rate by optimizing the runner design.
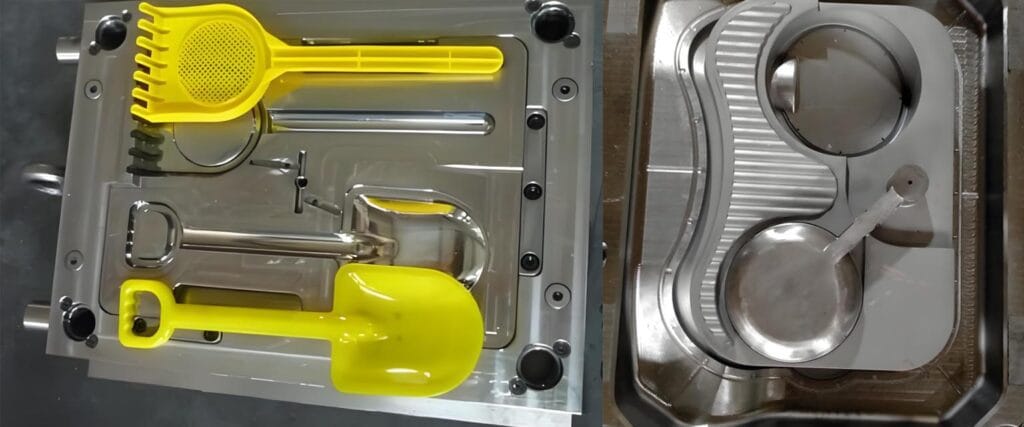
Continuous improvement and feedback mechanism
The design of injection molds is not static. During the production process, a continuous improvement mechanism should be established to collect production data and feedback information, and optimize the mold design in a timely manner. For example, by analyzing product defect data, adjust the cooling system or exhaust design of the mold.
Improvement case: WS mold factory analyzed production data and found that the exhaust system of a mold was insufficient. By optimizing the exhaust groove design, the scrap rate of the product was reduced from 10% to 2%.
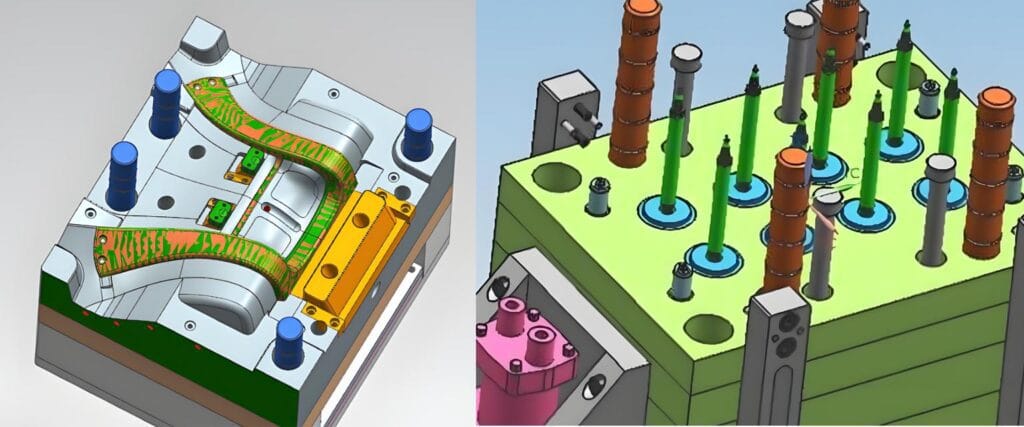
Injection mold processing design is a combination of science and art. It requires designers to take into account production efficiency, cost control and mold life while meeting product requirements. By following the above design principles, you can create efficient and accurate injection molds, providing a solid guarantee for the company’s production and manufacturing. In actual work, continuous learning and improvement are the key to improving design capabilities. I hope this article can provide some valuable references for your mold design journey.
In short, injection mold processing design is a highly comprehensive job that requires comprehensive consideration of multiple factors. By following the design principles of reasonable layout, optimized structure, and improved efficiency, we can design higher quality molds and contribute to the development of the injection molding industry.