Kevlar Aramid UHMWPE Bulletproof Helmet Mold Compression Mould maker in China. Wanna to get quality Kevlar Bulletproof helmet mold tailored to your needs,contact us for the best aramid Bulletproof helmet compression mold,various bulletproof military helmet molds are custom production…
Taizhou Huangyan military Aramid bulletproof helmet mold compression Mould and UHMWPE bulletproof helmet mould, Winsen Mold has a strong design team can accept: provide samples, or 3D drawings, 2D drawings, you are welcome to consult and quote kevlar bulletproof helmet molds !
Our factory is the first batch of designated production units for military product molds. Our factory designed and produced Kevlar Aramid bulletproof helmet molds and UHMWPE bulletproof helmet moulds compression mould in accordance with the new standards issued by the public safety industry, and took the lead in implementing product standardization and standardization. It plays an important role in strengthening team building, equipment modernization and maintaining public safety.Exported to North America, South America, Europe, the Middle East and other countries, and are well received by customers.
WS adheres to the production and management policy of “quality is more important than Mount Tai, customers are better than God”. Create safety with high technology and make friends all over the world with integrity. Rigorous and pragmatic and continuous innovation make our army molds become international and modern products. Make your ideals a reality with advanced technology.
We are a high-tech production entity integrating production and sales. We are a mold manufacturer specializing in bulletproof series and anti-riot series products and equipment. Advanced production equipment, sound and perfect quality assurance system, rich technical information and production experience, our factory has been absorbing international new technology and new product information for a long time, so that the performance indicators of bulletproof mold production can reach the advanced level , which is unique among similar enterprises in the country.
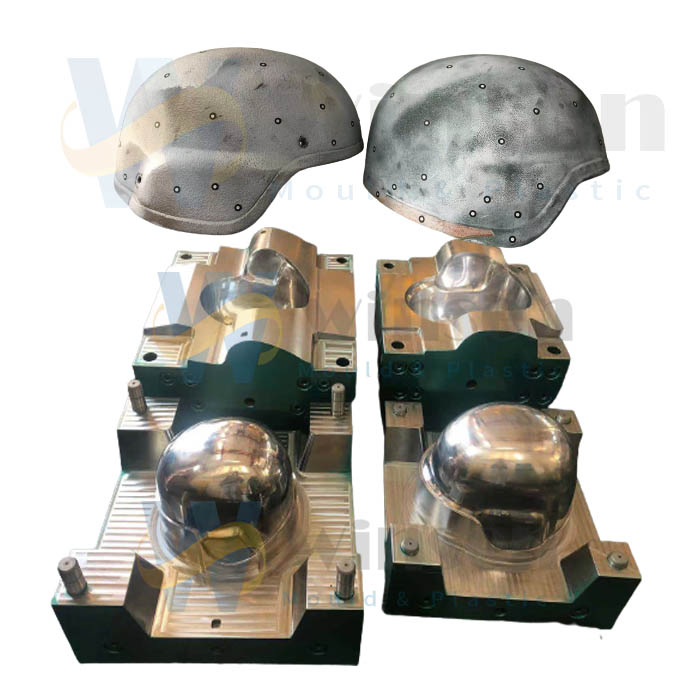
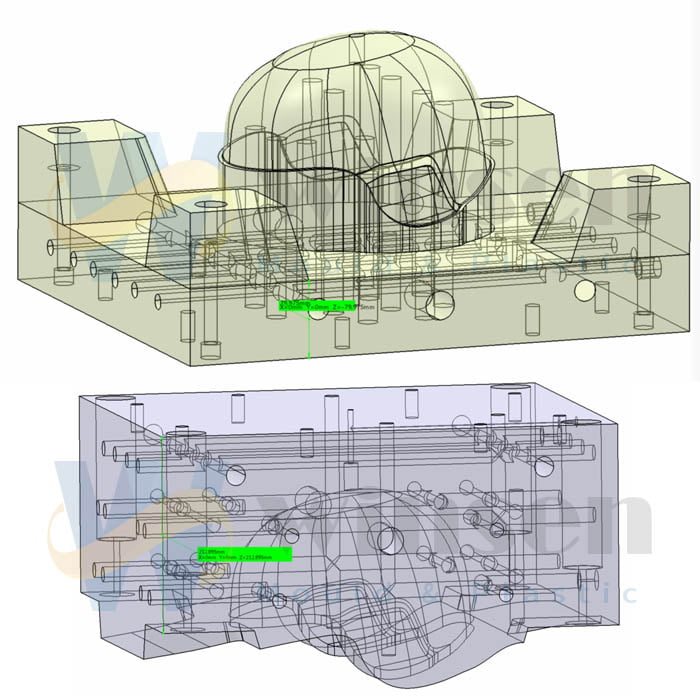
The Importance of a Bulletproof Helmet Mold and Materials Used
Introduction
When it comes to personal protection, bulletproof helmets play a crucial role in safeguarding individuals from ballistic threats. These helmets are designed to provide maximum protection while ensuring comfort and usability. One of the key components in the manufacturing process of bulletproof helmets is the mold used for compression molding. In this article, we will explore the importance of a bulletproof helmet mold, specifically focusing on the use of kevlar aramid and UHMWPE materials.
The mold used for compression molding is a critical factor in ensuring the quality and effectiveness of bulletproof helmets. It is responsible for shaping the helmet and determining its structural integrity. The design of the mold must be precise and accurate to ensure that the final product meets the necessary safety standards.
When it comes to materials used in bulletproof helmets, kevlar aramid and UHMWPE are two commonly used options. Kevlar aramid is a synthetic fiber known for its exceptional strength and resistance to impact and penetration. It is lightweight and flexible, making it an ideal material for bulletproof helmets. UHMWPE, on the other hand, stands for Ultra-High Molecular Weight Polyethylene. It is a type of plastic that offers excellent ballistic performance and is often used in combination with kevlar aramid for enhanced protection.
The choice between kevlar aramid and UHMWPE depends on various factors, including the level of protection required, weight considerations, and cost. Kevlar aramid is generally more expensive than UHMWPE but offers superior performance in terms of strength and durability. UHMWPE, on the other hand, is lighter and more cost-effective, making it a popular choice for certain applications.
In conclusion, the mold used for compression molding is a crucial component in the manufacturing process of bulletproof helmets. It determines the shape and structural integrity of the helmet, ensuring maximum protection for the wearer. The choice of materials, such as kevlar aramid and UHMWPE, further enhances the helmet’s ballistic performance. By understanding the importance of these factors, manufacturers can produce high-quality bulletproof helmets that meet the rigorous safety standards required in today’s world.
Not only does the bulletproof helmet mold play a vital role in shaping the outer shell of the helmet, but it also contributes to the overall strength and durability of the final product. The mold is designed to withstand high temperatures and pressures during the molding process, ensuring that the helmet’s material is evenly distributed and properly compressed.
One of the key considerations in designing a bulletproof helmet mold is the material used for the mold itself. It needs to be strong and rigid enough to withstand the pressures of the molding process while also being resistant to wear and tear. Typically, molds for bulletproof helmets are made from hardened steel or aluminum alloys, which offer the necessary strength and durability.
In addition to material selection, the design of the mold is also critical. The mold needs to be precisely engineered to create the desired shape and dimensions of the helmet. This involves careful consideration of factors such as the curvature of the helmet, the thickness of the shell, and the placement of any additional features or accessories.
Furthermore, the bulletproof helmet mold must also incorporate features that allow for easy removal of the molded helmet. This is achieved through the use of ejector pins or other mechanisms that help release the helmet from the mold without causing any damage to its structure.
Once the mold design is finalized, it is manufactured using advanced machining techniques such as CNC milling or wire EDM. These methods ensure the accuracy and precision required for the mold to produce consistent and high-quality helmets.
Overall, the bulletproof helmet mold is an essential component in the manufacturing process, as it determines the shape, strength, and durability of the final product. Its careful design and construction are crucial for producing reliable and effective bulletproof helmets that can withstand the demands of various hazardous situations.
Understanding Compression Molding
Compression molding is a widely used manufacturing technique for producing bulletproof helmets. It involves the use of a mold, which is filled with a composite material such as kevlar aramid or UHMWPE. The mold is then heated and subjected to high pressure, causing the material to flow and conform to the shape of the mold. This process results in a helmet with excellent strength and impact resistance.
One of the key advantages of compression molding is its ability to produce complex shapes with high precision. The mold used in this process is typically made of steel or aluminum and is designed to create the desired shape of the helmet. The composite material, which is in the form of sheets or pellets, is placed inside the mold and evenly distributed. The mold is then closed, and pressure is applied to compress the material.
During the compression stage, the heat and pressure cause the composite material to soften and flow. This allows it to conform to the intricate details of the mold, ensuring that every part of the helmet is accurately replicated. The combination of heat and pressure also helps to eliminate any air pockets or voids in the material, resulting in a dense and uniform structure.
Once the material has cooled and hardened, the mold is opened, and the helmet is removed. The excess material, known as flash, is trimmed off, leaving behind a finished product. The helmet may then undergo additional processes such as painting, polishing, or adding accessories before it is ready for use.
Compression molding offers several advantages over other manufacturing methods. Firstly, it allows for the production of helmets with consistent dimensions and properties, ensuring that each helmet meets the required standards for safety and performance. Secondly, the process is highly efficient and can be automated, making it suitable for large-scale production. Lastly, compression molding is a cost-effective method, as it minimizes material waste and requires less energy compared to other molding techniques.
In conclusion, compression molding is a versatile and efficient manufacturing technique for producing bulletproof helmets. Its ability to create complex shapes with precision, along with its high strength and impact resistance, make it an ideal choice for ensuring the safety of individuals in high-risk environments.
The Importance of Proper Mold Design
When it comes to manufacturing bulletproof helmets, proper mold design is crucial. The mold must be designed to accommodate the specific shape and size of the helmet, ensuring that it meets the required standards for ballistic protection. Additionally, the mold must be durable and able to withstand the high pressure and temperature of the compression molding process.
Proper mold design also includes the consideration of venting and cooling systems. Venting allows for the release of air and gases during the compression molding process, preventing defects such as air bubbles or voids in the final product. Cooling systems help to rapidly cool the molded helmet, reducing cycle times and increasing production efficiency.
One of the key factors in mold design is the selection of materials. The mold must be made from a material that can withstand the high pressures and temperatures involved in the compression molding process. Common materials used for molds include steel and aluminum, which have excellent heat resistance and durability.
Another important aspect of mold design is the incorporation of proper gating and runner systems. These systems help to control the flow of material into the mold cavity, ensuring uniform filling and reducing the risk of defects. The design of the gating and runner systems depends on factors such as the material being used, the shape of the helmet, and the desired properties of the final product.
Furthermore, mold design also takes into account the ease of mold release. A well-designed mold should allow for easy removal of the molded helmet without causing any damage. This is achieved through the use of draft angles, which are tapered surfaces on the mold that facilitate the release of the molded part.
In conclusion, proper mold design is essential for manufacturing bulletproof helmets. It ensures that the helmets meet the required standards for ballistic protection, while also optimizing production efficiency and reducing the risk of defects. By considering factors such as material selection, venting and cooling systems, gating and runner systems, and mold release, manufacturers can create molds that produce high-quality helmets consistently.
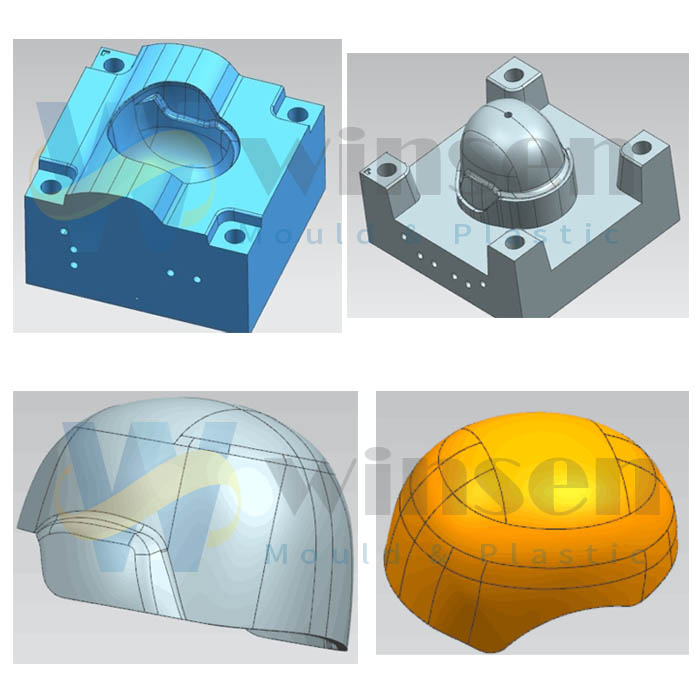
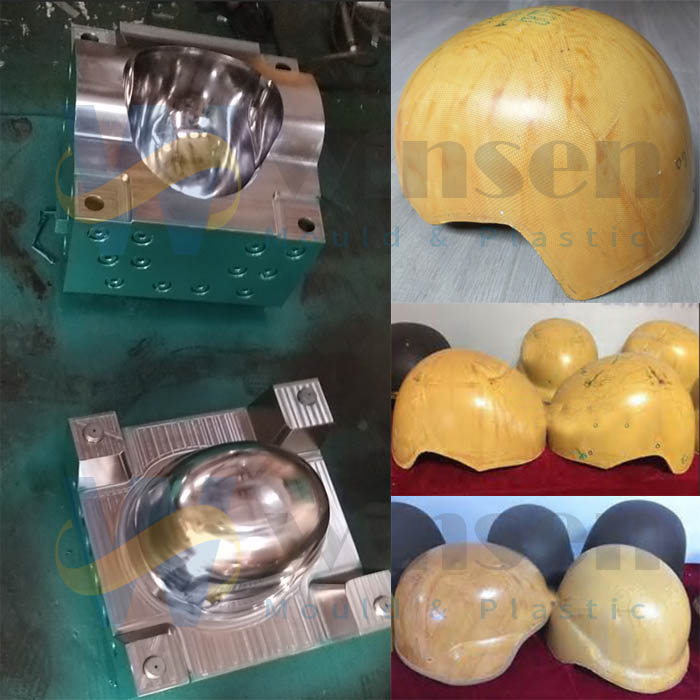
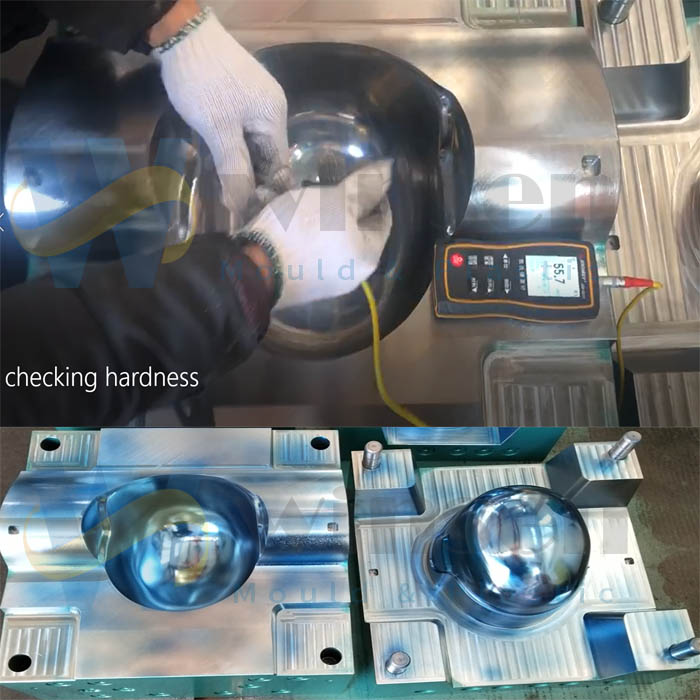
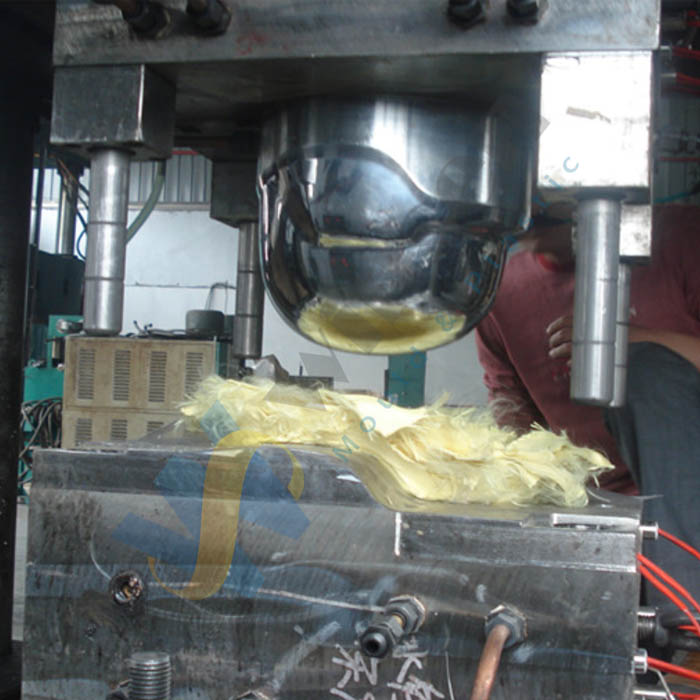
Learn about the importance of bulletproof helmet molds and the use of kevlar aramid and UHMWPE materials. Understand the process of compression molding and the benefits of kevlar aramid. Discover the advantages of UHMWPE in bulletproof helmet molds and the importance of proper mold design in manufacturing. Find out how to create high-quality bulletproof helmets that meet safety standards.