Key point of plastic injection mold maintenance,plastic injection molds are essential tools in the manufacturing industry, playing a pivotal role in producing high-quality plastic components injection moulding. To maximize their efficiency and lifespan, regular maintenance is crucial. In this blog post, we’ll delve into the key points of plastic injection mold maintenance, highlighting the practices that can ensure precision and longevity.
Table of Contents
ToggleKey point of plastic injection mold maintenance
Users of molds should maintain comprehensive records that include detailed information on mold usage, maintenance activities (such as lubrication, cleaning, and rust prevention), and any instances of damage. This practice enables users to analyze patterns and gather statistics on which specific parts and components are prone to damage and the extent of wear. By doing so, users can effectively identify and address potential issues.
These records should also encompass essential details related to the molding process, including mold parameters and the materials utilized in the production of the molded products. Such information serves as valuable resources, aiding in the swift identification of potential problems and facilitating quicker solutions.
In essence, meticulous record-keeping not only helps in understanding the history and condition of molds but also plays a crucial role in streamlining the testing phase and improving overall production efficiency.
1. Cleaning and Inspection
The first step in mold maintenance is thorough cleaning. Residual plastic, contaminants, and other debris must be removed to prevent defects in the molded parts. Regular inspections should also be conducted to identify any wear, damage, or potential issues. Addressing these issues promptly can prevent more extensive damage and costly repairs down the line.
It is essential to conduct comprehensive testing on the mold while the injection molding machine and mold are in normal operation. This involves measuring the dimensions of the final molded plastic part. This information serves as a valuable indicator for assessing the current condition of the mold. By scrutinizing the plastic parts, one can ascertain the state of critical components such as the cavity, core, cooling system, and the parting surface. This examination provides insights into potential damage and allows for a thorough evaluation of the mold’s overall health. Based on the information obtained from the plastic parts, one can make informed judgments about the damage status of the mold and devise appropriate maintenance measures. In essence, testing and measurement during regular operation are indispensable tools for understanding the mold’s performance and ensuring effective maintenance.
2. Lubrication of plastic injection mold
Proper lubrication is essential for the smooth operation of injection molds. Lubricate moving parts to reduce friction and wear. However, it’s crucial to use the correct lubricants, as using the wrong ones can lead to contamination and affect the quality of the molded parts.
3. Temperature Control
Maintaining optimal temperature conditions is paramount for the injection molding process. Regularly check and calibrate the temperature controls to ensure consistency. Variations in temperature can result in defects and affect the overall quality of the molded products.
4. Mold Storage
When molds are not in use, proper storage is crucial. Ensure they are stored in a clean and controlled environment to prevent corrosion and damage. Implementing protective measures, such as rust inhibitors, can help preserve the mold’s surface integrity.
5. Repair and Refurbishment
Even with regular maintenance, molds may still require periodic repairs or refurbishment. It’s important to address any signs of wear, damage, or fatigue promptly. Work with skilled professionals who can assess the condition of the mold and recommend appropriate repairs to extend its lifespan.
6. Training and Skill Development
Equip your team with the necessary skills and knowledge for effective mold maintenance. Training programs can help employees understand the importance of proper maintenance practices and enable them to identify potential issues early on.
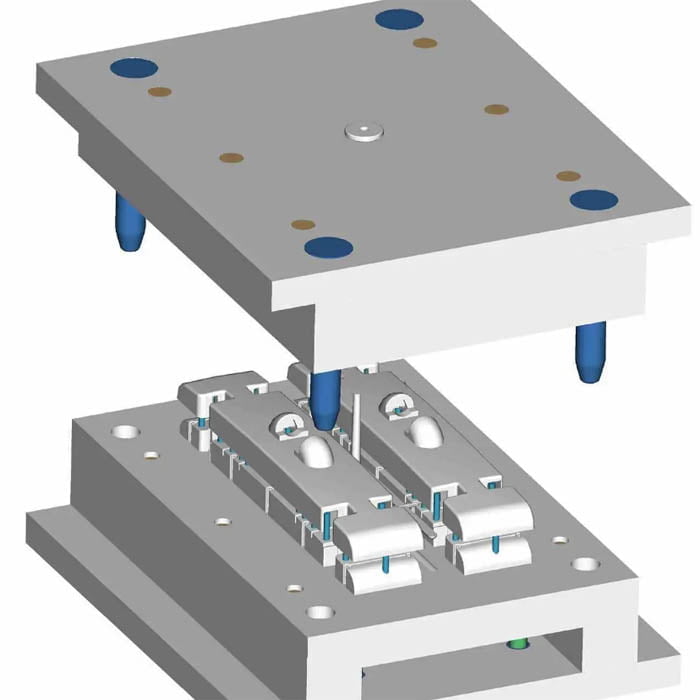
Critical Mold Components: Prioritizing Tracking and Testing
1. Checking the ejection and guide components
The ejection and guide components play a vital role in facilitating the smooth opening and closing movements of the mold, as well as the efficient ejection of plastic parts. Any disruption or damage to these parts can lead to production halts, underscoring the need for frequent maintenance. It is crucial to apply lubrication to the mold thimble and guide post, using the most suitable lubricant. Regular inspections should be conducted to identify deformities or surface damage in the ejector pin and guide post, promptly replacing them when necessary.
After each production cycle, it is imperative to clean the mold’s working surface. Additionally, the moving and guide components should be coated with specialized anti-rust oil. Special attention must be given to preserving the elastic strength of bearing parts in gear, rack, and spring molds to ensure they consistently operate at their best. This meticulous maintenance routine guarantees the continued seamless functionality of these crucial mold elements.
2. Replace spring components
Elastic components, like springs, are particularly susceptible to damage during regular use, often experiencing fractures and deformities. The recommended course of action is replacement. When undertaking the replacement procedure, meticulous attention should be given to the specifications and model of the spring. Confirmation of the spring’s size and type is determined through three key factors: color, outer diameter, and length. Replacement is only deemed appropriate when all three criteria match precisely. It’s worth noting that imported springs generally exhibit higher quality, although domestic mold springs also boast commendable quality standards.
Over the course of continuous production, the cooling water channels are susceptible to the accumulation of scale, rust, sludge, and algae. These deposits lead to a reduction in the cross-sectional area of the cooling channels, resulting in a significant narrowing of these passages. This, in turn, substantially diminishes the heat exchange rate between the cooling liquid and the mold, subsequently escalating production costs. Therefore, meticulous attention should be given to the cleaning of runners to maintain optimal performance. In the case of hot runner mold products, particular emphasis must be placed on the maintenance of heating and control systems to avert production failures.
In the realm of stamping and blanking die products, it is imperative to sharpen the cutting edges following prolonged use.
During the utilization of mold products, punches are prone to breakage, bending, and wear, with the punch sleeve typically experiencing wear. In instances of damage, it is recommended to replace the punches and sleeves with components of identical specifications. Key parameters for punches primarily encompass the dimensions of the working part, installation part, and overall length.
Inspect fastened components to ensure they are secure and undamaged. If any fastening parts are found to be loose or compromised, the recommended approach is to locate replacement parts of the same specifications. Evaluate pressing components like pressing plates and excellent glue, as well as unloading elements such as stripping plates and pneumatic top materials during maintenance. This involves a thorough examination of the interrelationships between these parts, identifying any damage, and subsequently repairing the affected components.
For pneumatic top materials, conduct checks for potential air leakage and implement appropriate measures based on specific circumstances, which may include the replacement of damaged air pipes.