Key to mold manufacturing industry is mold standardization.In modern manufacturing, mold standardization is a vital topic. Whether you work in automotive manufacturing, electronics manufacturing, medical device manufacturing, or other industries, molds play a vital role. This article will explore the importance of mold standardization, its impact on manufacturing, and how to implement effective plastic injection mold and composites compression mold standardization.
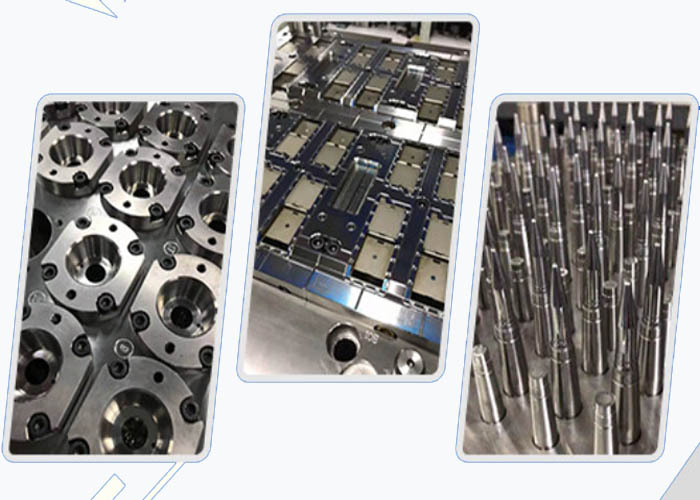
Table of Contents
ToggleWhat is mold standardization?
Mold standardization refers to the practice of adopting a set of generally accepted standards and specifications in the design, manufacture and use of molds in the manufacturing industry. These standards can cover the mold’s dimensions, materials, manufacturing processes, maintenance requirements, and other relevant factors. Through mold standardization, manufacturing companies can ensure that their products have consistent quality and performance from batch to batch.
The importance of mold standardization
1. Improve production efficiency
Mold standardization helps reduce variation and instability in the production process. When mold design and manufacturing meet standards, the stability of the production line will be greatly improved, thereby improving production efficiency. Workers can switch molds faster, reducing downtime and increasing throughput.
2. Reduce costs
Consistent mold standards make molds easier to maintain and replace. This means maintenance personnel can identify and fix problems more quickly, reducing repair time and costs. In addition, standardization can also reduce the cost of mold manufacturing because manufacturers can mass-produce standardized molds, thereby reducing the cost of a single mold.
3. Improve product quality
Standardized mold design and manufacturing processes help ensure product consistency and quality. Product size and characteristics will be more controllable, reducing defective rates. This is particularly important for industries that require high-quality products, such as medical devices and aerospace.
4. Promote innovation
Mold standardization is not the enemy of innovation; on the contrary, it can promote innovation. By following standards, manufacturers can focus on higher-level issues, such as the development of new materials, new processes, and new technologies. On the basis of standardized molds, manufacturers can more easily introduce innovative elements.
Steps to implement mold standardization
1.Assess current mold inventory: First, companies need to understand their current mold inventory, including the type, quantity, and status of molds.
2.Determine standards: Develop a set of mold standards that cover requirements for design, manufacturing, maintenance and use.
3.Train employees: Train employees so that they understand mold standards and can correctly use and maintain molds.
4.Update mold inventory: Gradually update mold inventory to comply with established standards. This may require an investment of time and money, but will ultimately yield long-term benefits.
5.Continuous monitoring and improvement: Mold standardization is an ongoing process. Companies should regularly monitor the performance of molds and make improvements and updates as necessary.
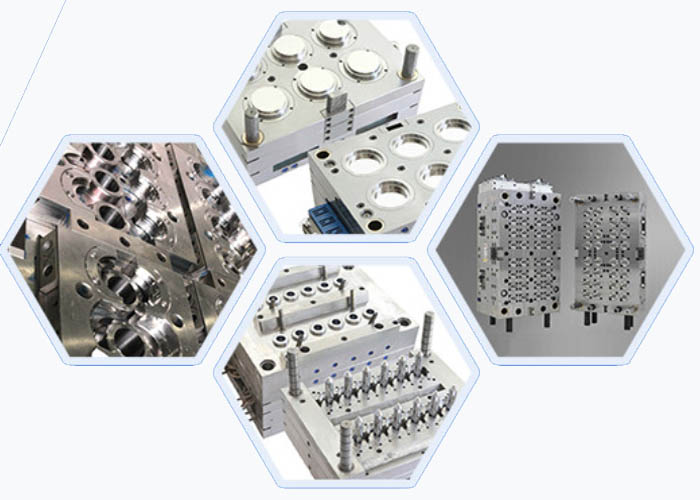
China’s mold standardization system includes four categories of standards, namely: basic mold standards, mold process quality standards, mold parts standards and technical standards related to mold production. Die standards can be divided into stamping die standards, plastic injection die standards, die-casting die standards, forging die standards, fastener cold heading die standards, wire drawing die standards, cold extrusion die standards, rubber die standards, and glass products. Ten categories such as mold and automotive die standards. At present, China has more than 50 mold standards, a total of more than 300 standard numbers, and 14 general devices and 244 varieties of automotive die parts, a total of 363 standards. The formulation, publicity and implementation of these standards have improved the degree and level of mold standardization in China.
With the increase in international exchanges, the development of the localization of imported molds, and the requirements of the three foreign-funded enterprises for international standards for their supporting molds, on the one hand, in the aspect of standard formulation, attention has been paid to adopting international standards or advanced foreign national standards as much as possible, including the adoption of advanced On the other hand, many mold standard parts manufacturers produce mold standard parts according to the market demand, in addition to producing mold standard parts according to Chinese standards, but also produce mold standard parts according to the standards of foreign advanced enterprises. For example, the standards of Japanese “Futeba”, American “dme”, German “Haskow” and other companies have become popular in China.
Mold standardization plays a key role in modern manufacturing. It helps improve production efficiency, reduce costs, improve product quality, and promote innovation. By implementing mold standardization, manufacturing companies can ensure that they remain competitive in a highly competitive market while delivering consistently high-quality products. Therefore, manufacturing companies should seriously consider mold standardization and take appropriate measures to implement it.