Impact of mobility of SMC molding material on molding process,the mobility of Sheet Molding Compound (SMC) material plays a crucial role in the molding process. SMC is a composite material consisting of chopped glass fibers, resin, and various additives. Its ability to flow and conform to the shape of the mold is essential for achieving the desired product quality and structural integrity.
In this context, mobility refers to the material’s capacity to flow and fill intricate mold cavities smoothly during the molding process. The impact of material mobility on the SMC compression molding process is multifaceted. It affects the distribution of fibers, the consolidation of the composite, and the overall quality of the final product.
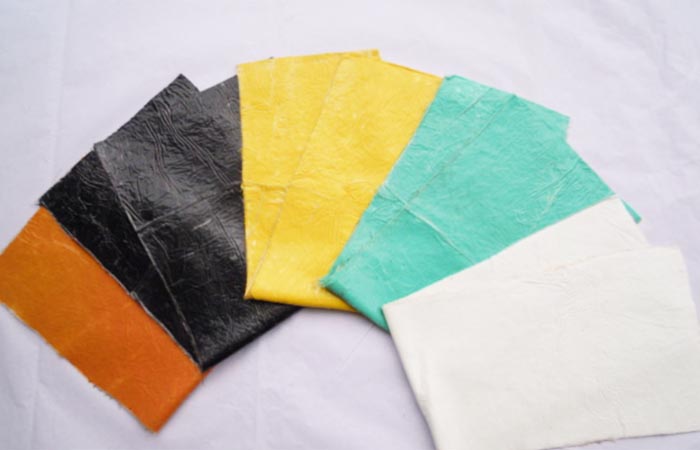
Impact of mobility of SMC molding material on molding process
1. Filling performance
Fluidity determines whether the SMC material can fully fill various parts of the mold. If the fluidity is poor, it may cause voids or uneven filling inside the mold, affecting the quality of molded parts.
2. Fiber distribution
SMC contains glass fibers, and poor fluidity may cause these fibers to be unevenly distributed during the molding process. Uneven fiber distribution affects the strength and stiffness of formed parts.
3. Surface quality
Fluidity has an important impact on the surface quality of molded parts. Insufficient fluidity may result in blemishes, ripples or bubbles on the surface of the part, affecting appearance and performance.
4. Molding time
The time required for fluidity to affect the molding process. If flow is poor, it may take longer to fill the mold, thereby increasing production cycle times.
5. Scrap rate
Poor fluidity may cause the SMC material to overflow at the edges or seams of the mold, forming scrap or remaining material that requires subsequent processing.
6. Process parameter adjustment
To optimize the flow of SMC materials, process parameters such as temperature, pressure, and mold design may need to be adjusted to ensure that the material can flow and fill the mold appropriately.
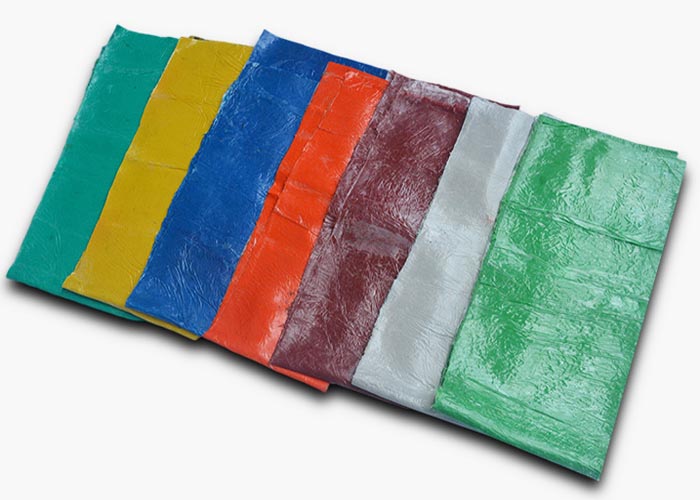
The fluidity of the molding material refers to the ability of the material to fill the mold cavity under temperature and pressure during compression. Because the short fiber molding compound has longer fibers and higher fiber content and no powder filler, it has poor flow properties. There are many factors that affect the fluidity of short fiber molding materials, including the thermosetting properties of the resin resin itself, the composition and ratio of materials, product structure and mold structure, as well as the quality indicators of molding materials and the shape of materials, fiber length and molding process. manipulation of conditions, etc. The quality index of the molding compound not only affects its fluidity, but also is closely related to the quality of the product.
Which good practice for SMC composite materials indicates that in the quality index of the central molding material, its volatile content should be strictly controlled. Volatile content is added, and material fluidity is added. However, when the volatile content is too high, it is easy to cause a lot of loss of resin during molding, the shrinkage of the product is increased, and even warpage occurs, and the surface of the product has defects such as bubbles, ripples, flow marks, sticking, and surface finish. When the volatile content is too low, the fluidity of the material will be significantly reduced, resulting in difficulty in forming the product and easy to lack of material.
The shape of the molding compound also has a great influence on its fluidity and product function. Premixes have better flow properties than prepregs. When the premix is in a “flaky” or loose state, the flow resistance is large, the mutual solubility between the materials is poor, and the function of the joint is easily formed.
Therefore, optimizing and controlling the mobility of SMC material is critical for achieving consistent and high-quality molded products. This involves careful selection of resin formulations, processing parameters, and mold design to ensure that the material flows properly and conforms to the desired shape during the molding process.