Plastic Bottle Cap and Bottle Mold Manufacturing
In the realm of plastic packaging, two crucial components stand out – the bottle cap and the bottle itself. The production of these seemingly simple items involves complex processes that require precision, expertise, and advanced technology. In this blog, we will delve into the fascinating world of plastic bottle cap mold injection molding and bottle mold blow molding processes.
Table of Contents
TogglePlastic Bottle Cap Injection Molding Process
The Importance of Bottle Cap Molds
A bottle cap mold is the foundation of cap production. It is a custom-designed tool that shapes the molten plastic into the desired cap form. The quality and precision of the mold directly impact the functionality and appearance of the final cap product. A well-designed plastic cap mold ensures a perfect fit with the bottle, provides a secure seal, and meets the aesthetic requirements of the brand.
The Injection Molding Process
Plastic bottle cap injection molding is a highly efficient and precise manufacturing process. It begins with the selection of the appropriate plastic material, such as polypropylene or high-density polyethylene, known for their durability and compatibility with various liquids.
The process starts with the plastic material being fed into a hopper. It is then heated and melted in the barrel of the injection molding machine. Once the plastic reaches the ideal temperature and consistency, it is injected at high pressure into the bottle cap mold. The mold is designed with intricate details to create features like threads, ridges, and any brand-specific designs.
The molten plastic fills the mold cavity, taking on the exact shape of the mold. It is then allowed to cool and solidify. After the cooling process, the mold opens, and the newly formed plastic bottle cap is ejected. This process is repeated rapidly, with modern injection molding machines capable of producing thousands of caps per hour.
Quality Control in Injection Molding
Quality control is a critical aspect of the plastic bottle cap injection molding process. Each cap is inspected for defects such as imperfections in the threads, which could affect the seal, or blemishes that might impact the cap’s appearance. Advanced inspection systems, including automated vision inspection, are often used to ensure that every cap meets the stringent quality standards.
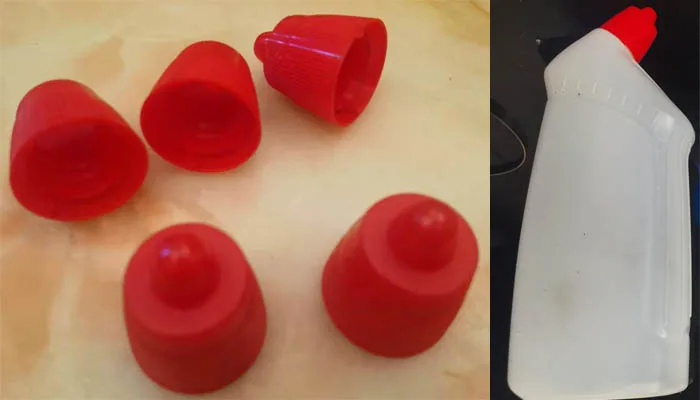
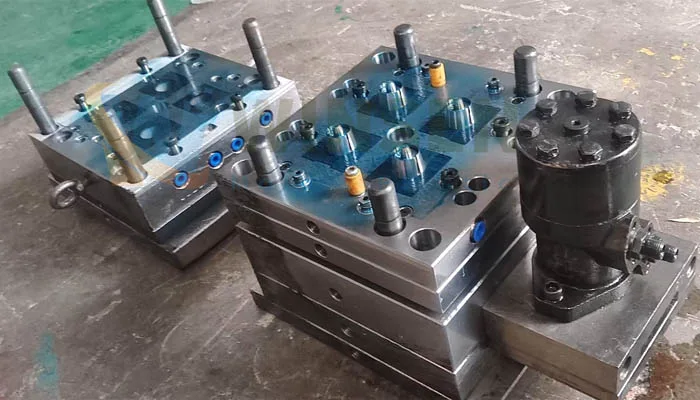
The Bottle Mold Blow Molding Process
Understanding Bottle Molds
Just as the bottle cap mold is essential for cap production, the bottle mold plays a pivotal role in shaping the bottle. A bottle mold, also known as a blow mold, is designed to create the body of the bottle. It determines the bottle’s size, shape, and capacity. The design of the bottle mold must consider factors such as ergonomics, ease of handling, and the ability to withstand the pressure of the liquid inside.
The Blow Molding Process
Plastic bottle blow molding is a process used to create hollow plastic parts, such as bottles. It begins with the production of a preform, which is a small, thick-walled tube of plastic. The preform is typically produced using injection molding and is designed to have the necessary features for the final bottle, such as the screw threads at the neck.
The preform is then heated until it becomes pliable. It is then placed into the bottle blowing mold. High-pressure air is blown into the preform, causing it to expand and take on the shape of the mold. The plastic cools and solidifies against the mold, forming the final bottle shape. Once the bottle has cooled, it is removed from the mold and is ready for further processing, such as labeling and filling.
Advantages of Blow Molding
Blow molding offers several advantages in bottle production. It allows for the creation of lightweight yet strong bottles, which is crucial for reducing transportation costs and environmental impact. The process is also highly efficient, with the ability to produce large quantities of bottles in a short amount of time. Additionally, blow molding enables the production of bottles with complex shapes and designs, providing brands with the flexibility to create unique packaging that stands out on the shelves.
The Symbiotic Relationship Between Cap and Bottle Molds
The bottle cap mold and the bottle mold are intrinsically linked. The cap must fit perfectly onto the bottle to ensure a secure seal and prevent leaks. This requires precise coordination between the design of the bottle mold and the cap mold. Manufacturers often work closely with designers and engineers to ensure that the threads on the cap and the bottle neck are perfectly matched.
Moreover, the materials used in both molds must be compatible. For example, if the bottle is made from a certain type of plastic, the cap must also be made from a compatible material to ensure a proper seal and to prevent any chemical reactions that could affect the quality of the contents.
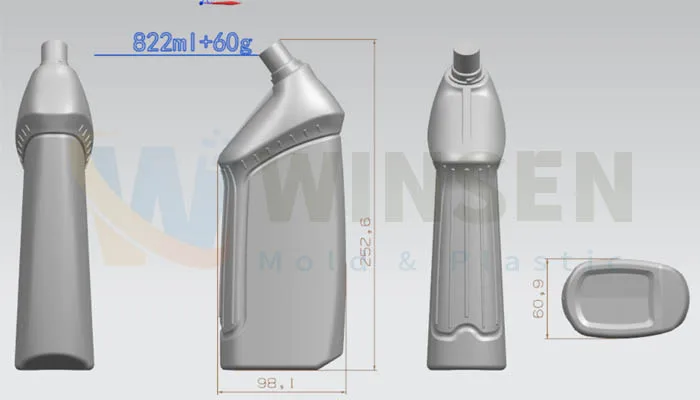
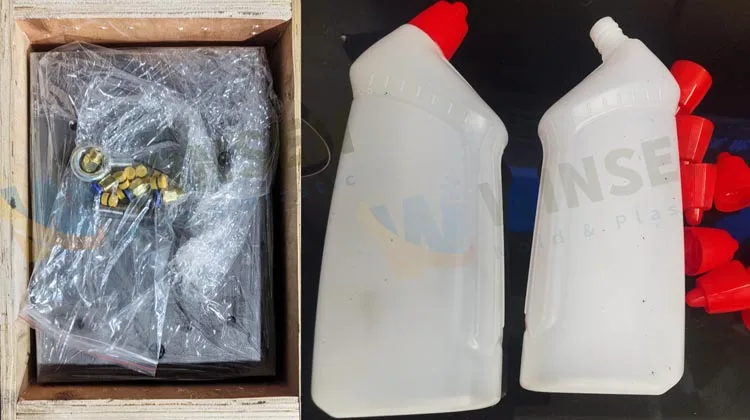
Innovations in Mold Technology
Smart Molds
In recent years, there have been significant innovations in mold technology. Smart molds, equipped with sensors and connected to the Internet of Things (IoT), are revolutionizing the manufacturing process. These molds can provide real-time data on the molding process, such as temperature, pressure, and cycle times. This data can be used to optimize the production process, reduce waste, and improve product quality.
Sustainable Molds
With increasing environmental concerns, there is a growing focus on sustainable mold materials and processes. Manufacturers are exploring the use of bio-based plastics and recycled materials in both bottle cap molds and bottle molds. Additionally, energy-efficient molding machines and processes are being developed to reduce the carbon footprint of plastic bottle production.
Conclusion
The processes of plastic bottle cap injection molding and bottle mold blow molding are intricate and vital to the packaging industry. From the precision of the molds to the efficiency of the molding processes, every step is crucial in ensuring the production of high-quality, functional, and aesthetically pleasing packaging. As technology continues to advance, we can expect even greater innovations in mold design and manufacturing processes, further enhancing the capabilities and sustainability of plastic bottle and cap production. Whether it’s the perfect fit of a cap on a bottle or the unique shape of a bottle that catches the eye, the world of plastic bottle cap and bottle mold manufacturing is a testament to human ingenuity and the pursuit of excellence in everyday products.