Family Mould
A plastic family mould is a design that contains multiple cavities in a single mould, allowing multiple parts of the same material to be produced in one injection moulding cycle. This design usually results in a different part number for each cavity. This article will explore the appearance characteristics, advantages and disadvantages of family moulds, and their layout in DFM (Design and Manufacturing Feasibility) reports.
Table of Contents
ToggleAppearance characteristics of family moulds
The design of plastic family moulds usually contains multiple cavities, which are distributed on the surface of the mould, and each cavity corresponds to a specific part. This design allows the mold to produce multiple parts at the same time in one operation, improving production efficiency. For example, a family mould may contain 5 different cavities, each cavity produces a different part, thus manufacturing 5 different parts in one moulding process.
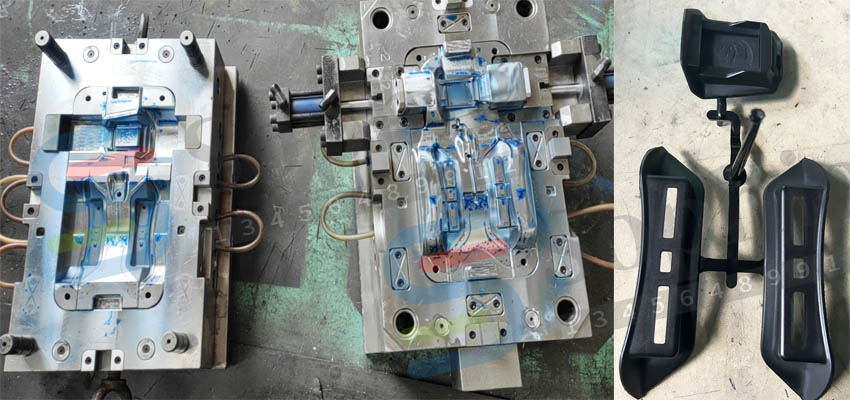
Advantages and Disadvantages of Family Moulds
Advantage
- Save on tooling costs: Because family mould can produce multiple parts in one moulding, the overall cost of moulding can be significantly reduced relative to making moulds for each part individually.
- Rapid prototyping cycle: The design of the family mould allows multiple parts to be molded at the same time, which can reduce the moulding cycle and increase production speed.
- Suitable for prototype molds: In the early stages of product development, family moulds can quickly produce multiple parts for easy prototype testing and design verification.
Disadvantages
- Unbalanced filling: When the shape of the parts in the mould is greatly different, it may cause unbalanced filling and affect product quality.
- Increased risk of molding defects: Since multiple parts are molded simultaneously, the risk of defects during the moulding process increases.
- Not easy to change orders or materials: Once the family mould design is complete, it can be difficult to change the order or materials of production parts, which limits production flexibility.
Layout in DFM Report
At WS MOULD, our design team will lay out the design of the family mould in detail in the DFM report. This includes the distribution of cavities, the design of the cooling system, the layout of the gate system, etc. Experienced injection molding experts can use the DFM report to evaluate the rationality of the mould design and the feasibility of the production process.
The layout of the DFM report should take into account the following key points:
- Cavity distribution: Ensure that the distribution of cavities can maximize the efficiency of the mould while avoiding filling imbalance caused by differences in part shapes.
- Cooling system: Design an effective cooling system to ensure that the mould can be evenly cooled during the production process and reduce moulding defects.
- Gating system: Reasonably design the gate system to ensure that the molten material can be evenly filled into each cavity.
- Material flow: Analyze the flow path of the material in the mould to ensure that there are no dead corners or flow obstructions to reduce bubbles and material waste.
- Mold disassembly: Consider the disassembly and assembly of the mould to ensure that damaged parts can be quickly replaced or maintained during the production process.
By comprehensively considering these factors in the DFM report, it can be ensured that the design of the family mould is economical and efficient while reducing risks in the production process.
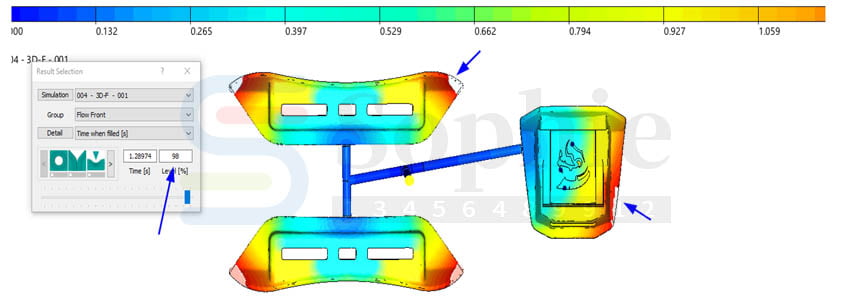
Family moulds offer a cost-effective and productive solution in injection moulding, especially for prototype development and small batch production. However, designers need to carefully consider the layout of the mould and possible problems during production to ensure the quality of the final product. Through detailed analysis and evaluation of DFM reports, the design of family moulds can be optimized to achieve a more efficient and reliable production process.