The completion of a plastic injection mold is achieved through a series of processing steps. The processing procedure of the injection mold is relatively complicated. Let’s learn more about the specific steps of the complete injection mold production.
Table of Contents
Toggle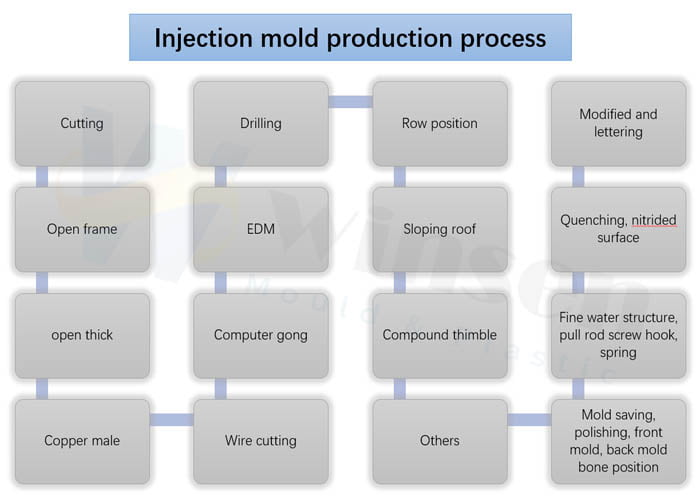
Injection Mold Production Process
1. Cutting: front mold material, rear mold material, insert material, row material, inclined roof material;
2. Process frame: front frame mold and rear frame mold;
3. Thickening: the front cavity is thickened, the rear cavity is thickened, and the parting line is thickened;
4. Copper male: front mold copper male, rear mold copper male, parting line clear angle copper male;
5. Wire cutting: insert parting line, copper male, inclined top pillow;
6. Computer gong: fine gong parting line, after fine gong mold core;
7. EDM: thick front mold, copper male, clear angle of male mold line, back mold bone position, pillow position;
8. Drilling, pinhole, thimble;
9. row position, row position voltage pole;
10. sloping roof
11. Compound thimble, with thimble;
12. Others: ① chirp, mold pit, garbage nails (limiting nails); ② flying die; ③ nozzle, support, spring, water transport;
13. Mold saving, polishing, front mold, back mold bone position;
14. Fine water structure, pull rod screw hook, spring.
15. Quenching, nitrided surface;
16. Modified and lettering.
Plastic Injection Mold design knowledge
Design basis
Dimensional accuracy and the correctness of its relative dimensions.
According to the specific requirements and functions of entire product of the plastic product, determine its external mass and size:
Plastic products, such as toys, require high appearance quality and low dimensional accuracy;
Functional plastic products with strict size requirements;
Plastic products with strict appearance and size requirements, such as cameras.
Is the draft angle reasonable?
The demolding slope is directly related to the demoulding and quality of plastic products, that is, whether the injection can be carried out smoothly:
The demoulding slope is sufficient;
The slope should be suitable for the molding parting or parting surface of plastic products; whether it will affect the appearance and the accuracy of wall thickness dimensions;
Whether it will affect the strength of a certain part of the plastic product
Design Flow
Analysis and digestion of plastic product drawings and solids (actual samples):
A. Product geometry;
B. dimensions, tolerances and design basis;
C. technical requirements;
D. plastic name, trademark, surface requirements.
Number and arrangement of cavities
A.The weight of the product and the injection volume of the injection machine;
B. the output volume of the product and the injection volume of the injection machine;
C. The outer dimensions of the mold and the effective area of the injection molding machine assembly mold (or the inner clearance of the tie rod of the injection machine)
D. Product accuracy and color;
E. The product has an infinite axis and its processing method;
F. mass production of products;
G. Economic benefits (production value per mold)
After the number of cavities is determined, the layout is carried out, that is, the layout of the cavities. The layout method is related to the size of the mold, the casting system, casting and other aspects.
System balance, design of core pulling (slider) mechanism, design of inserts and cores, and design of heat exchange system, all of which are about parting and pouring.
The choice of the mouth position is related, so in the specific design process, necessary adjustments must be made to achieve a more perfect design.
WS MOLD customized production and processing of various plastic injection molds, plastic products. Provide one-stop service of design, mold development, product production and processing, and transportation to the door. It can process a variety of plastic materials and molds, including wood plastic molds, PVC, ABS, PC, PMMA, PP, PE, POM, PA and other products. Welcome to consult and customize the injection moulding molds and products you need.