Mold Quality Standard
Mold quality standards are one of the key factors to ensure that the design, manufacturing and use of molds in the manufacturing process comply with certain specifications and requirements. These standards are designed to guarantee the performance, durability and production efficiency of the mold, thereby ensuring that the quality of the final product reaches the expected level. Mold quality standards cover many aspects, including material selection, dimensional accuracy, surface treatment and other key elements to meet the needs of various industries for product consistency and reliability. In the modern manufacturing environment, following mold quality standards not only helps improve production efficiency, but also reduces the defective rate during the manufacturing process, giving companies a competitive advantage in the market. Therefore, setting and adhering to mold quality standards is a key step to ensure the sustainable development of the manufacturing industry and excellent product quality. In this article we will explain in detail the quality standards of injection molds.
Producing high-quality molds necessitates not only a high level of mold design proficiency and precision in processing technology but also demands strict adherence to established “standards” without any tolerance for the notion of “almost.” This article outlines various acceptance criteria for ensuring the excellence of a mold .
Injection Mold Quality Standard
Mold Appearance
Mold Appearance stands as a pivotal dimension within the spectrum of mold quality standards, encapsulating the visual and aesthetic aspects that contribute to the overall excellence of a mold.
- Utilize plastic block-inserting water nozzles for the cooling system, unless otherwise specified by the customer.
- Ensure that the cooling water nozzles do not protrude beyond the surface of the mold base.
- Machine the cooling water nozzles with countersinks of diameters 25mm, 30mm, and 35mm, ensuring consistent chamfering of the orifices.
- Clearly mark the cooling water nozzles with “in” and “out” indications.
- Ensure that the marked English characters and numbers are larger than 5/6, positioned 10mm directly below the faucet, and exhibit clear, neat, and evenly spaced handwriting.
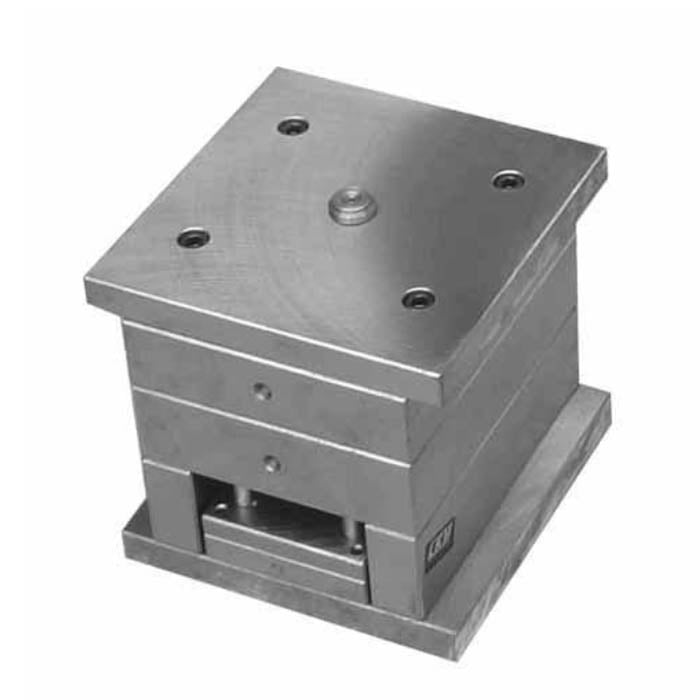
- Mold accessories should not impede the lifting and storage of the mold. Protect exposed components such as oil cylinders, faucets, and re-reset mechanisms during installation with supporting legs.
- Size the ejection hole of the mold in accordance with the specified injection molding machine requirements.
- Secure and position the positioning ring reliably, with diameters of 100mm and 250mm. The positioning ring should be 10-20mm higher than the bottom plate, unless otherwise specified by the customer.
- Ensure that the dimensions of the mold meet the specified requirements of the injection molding machine.
- Clearly mark the installation direction of molds with directional requirements using arrows on the front or rear formwork. Place the word “UP” next to the arrow, both in yellow, with a word height of 50mm.
- Eliminate surface defects such as pits, rust, excess rings, water vapor inlets and outlets, oil holes, etc., that affect the appearance of the mold base.
- Facilitate easy hoisting and transportation of the mold. Avoid disassembling mold parts during hoisting, and ensure that the lifting ring does not interfere with faucets, oil cylinders, pre-reset rods, etc.
This facet scrutinizes the surface characteristics, finishing details, and visual integrity of the mold, playing a crucial role in ensuring not only functional efficiency but also an impeccable and professional presentation.
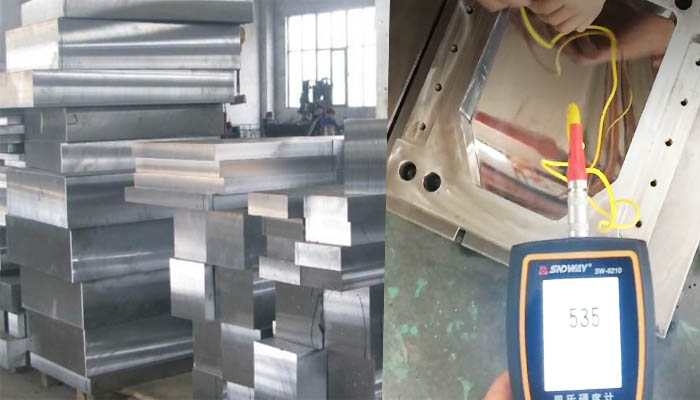
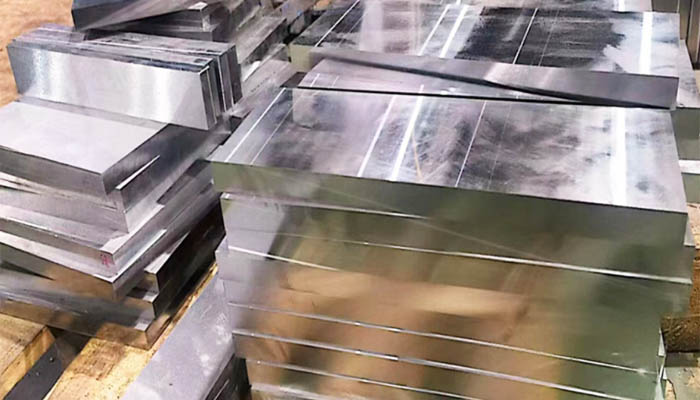
Mold Material And Hardness
In the realm of mold quality standards, Mold Material and Hardness emerge as critical benchmarks, wielding significant influence over the durability, performance, and precision of the molding process.
- Utilize a mold base that adheres to established standards and specifications.
- Employ materials of superior performance, surpassing 40Cr, for the mold-forming components and gating system (including core, movable and fixed die inserts, movable inserts, shunt cone, push rod, and gate sleeve).
- In cases where molded plastics are prone to corrosion, opt for corrosion-resistant materials for the molding parts or implement anti-corrosion measures on the molding surface.
- Ensure that the hardness of molded parts is not less than 50HRC, or achieve a surface hardening hardness exceeding 600HV.
This dimension encompasses meticulous scrutiny of the materials employed and their corresponding hardness levels, constituting a foundational element in the pursuit of ensuring resilient, high-performing molds for diverse industrial applications.
Ejection, Reset, Ferrule Extraction, Take Out
Ejection, Reset, Ferrule Extraction, and Take Out collectively constitute a vital facet within the framework of mold quality standards, focusing on the intricate mechanisms that govern the seamless ejection and extraction processes in mold operations.
- Ensure a seamless ejection process characterized by smooth operation, absence of sticking, and no abnormal noise.
- Polish the sloped top surface, positioning it below the core surface for enhanced functionality.
- Incorporate oil grooves on sliding parts, subjecting their surfaces to nitriding with a post-treatment hardness exceeding HV700.
- Implement anti-rotation positioning for all rams, assigning unique numbering to each ram for clear identification.
- Utilize limit blocks to control the ejection distance effectively.
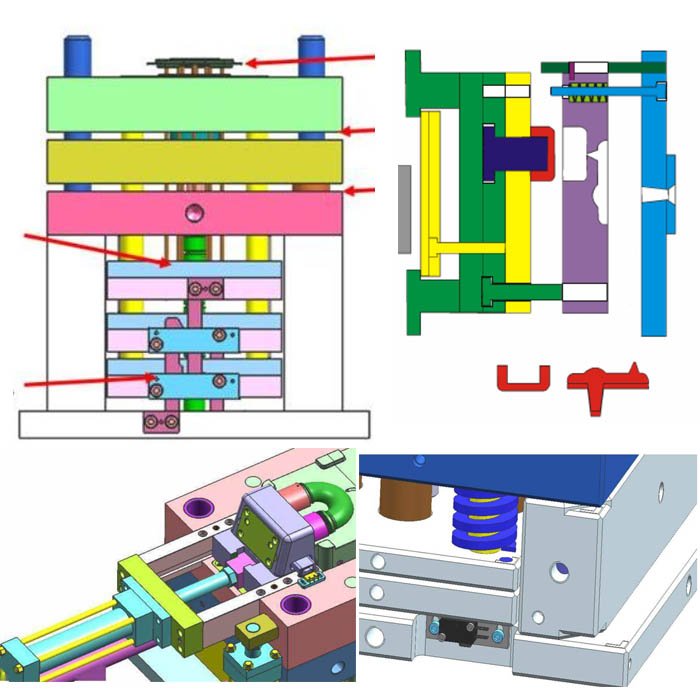
- Use inclined guide columns for slider core pulling, ensuring a slight angle difference with the slider’s locking surface. Employ a cylinder for extraction with extended slider strokes.
- Equip covered cylinder end faces with a self-locking mechanism.
- Place a T8A wear-resistant plate under large sliders, ensuring a slight elevation for efficient oil drainage.
- Stabilize the ejector rod, preventing vertical movement.
- Incorporate consistent, easily removable barbs on the ejector rod for streamlined product extraction.
- Align matching clearances and surface specifications with enterprise standards for ejector pin components.
- Facilitate operator-friendly product removal.
- Enhance product ejection along the inclined top with grooves or etching on the ejector rod.
- Securely fix the top block, processing non-molded parts with a sloped design for efficient functionality.
- Ensure no iron filings in the die base oil passage holes.
- Maintain a flat end face on the return rod without spot welding or shims.
- Ensure smooth sliding and easy opening of the gate plate for three-plate molds.
- Arrange limit pull rods to prevent interference with the operator in three-plate molds.
- Ensure smooth oil and air passages for effective hydraulic ejector reset.
- Open an exhaust port at the bottom of the guide bush.
- Avoid installing positioning pins without proper clearance.
This dimension delves into the precision, reliability, and efficiency of ejection systems, reset mechanisms, ferrule extraction, and overall take-out procedures, essential for ensuring optimal functionality and longevity of molds across diverse manufacturing applications.
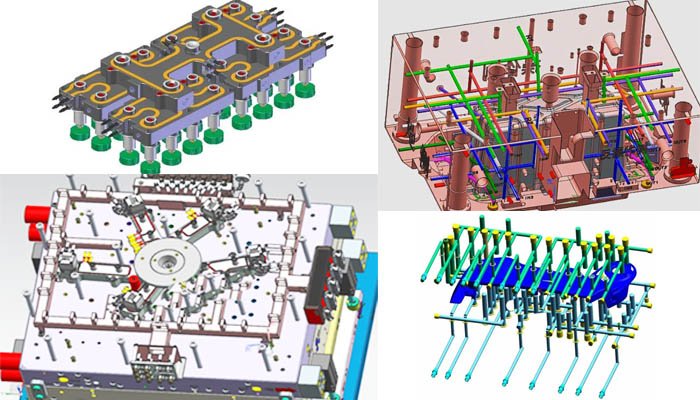
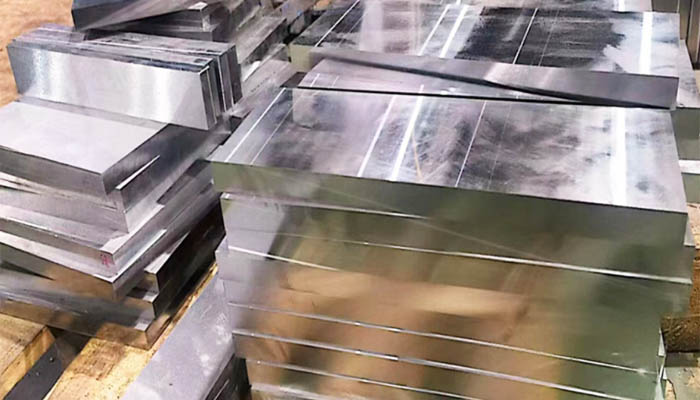
Cooling And Heating System
Cooling and Heating System stands as a fundamental pillar within the framework of mold quality standards, addressing the pivotal role played by temperature regulation in optimizing the molding process.
- Ensure the unobstructed functionality of the cooling and heating system.
- Guarantee a reliable seal, preventing system leakage under 0.5MPa pressure, and ensuring ease of repair.
- Align the size and shape of sealing grooves on the mold base with relevant standards.
- Apply butter to the sealing ring during placement, positioning it higher than the mold base surface.
- Construct water and oil channel spacers from corrosion-resistant materials.
- Implement a centralized water supply method for both the front and rear molds.
This dimension encompasses meticulous considerations for both cooling and heating systems, crucial for achieving consistent and precise manufacturing outcomes. Effective thermal management not only ensures material integrity but also influences cycle times, dimensional stability, and overall production efficiency, making it an indispensable aspect of mold quality assessment.
Gating System
Gating System serves as a cornerstone in the realm of mold quality standards, underscoring the critical significance of an efficient and well-designed system for directing molten material into the mold cavity.
- Ensure the gate setting enhances product appearance and aligns with product assembly requirements.
- Design the runner’s cross-section and length optimally, minimizing plastic loss by reducing cross-sectional area while maintaining forming quality and shortening the filling and cooling time.
- Adopt a trapezoidal or semi-circular configuration for the partial section of the three-plate die runner on the back of the front formwork.
- In a three-plate mold, incorporate a cut-off handle on the sprue plate with a sprue entrance diameter less than 3mm. Create a 3mm-deep step recess at the ball head on the sprue plate.
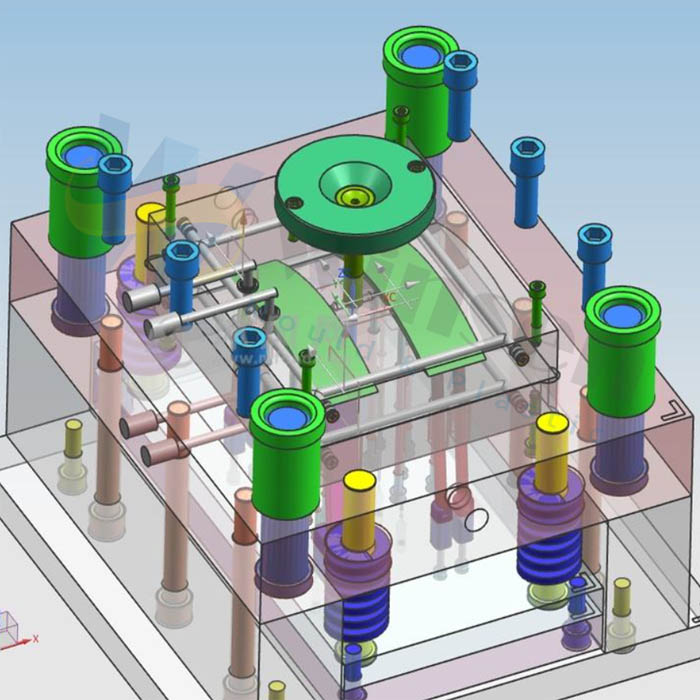
- Use inclined guide columns for slider core pulling, ensuring a slight angle difference with the slider’s locking surface. Employ a cylinder for extraction with extended slider strokes.
- Equip covered cylinder end faces with a self-locking mechanism.
- Place a T8A wear-resistant plate under large sliders, ensuring a slight elevation for efficient oil drainage.
- Stabilize the ejector rod, preventing vertical movement.
- Incorporate consistent, easily removable barbs on the ejector rod for streamlined product extraction.
- Align matching clearances and surface specifications with enterprise standards for ejector pin components.
- Facilitate operator-friendly product removal.
- Enhance product ejection along the inclined top with grooves or etching on the ejector rod.
- Securely fix the top block, processing non-molded parts with a sloped design for efficient functionality.
- Ensure no iron filings in the die base oil passage holes.
- Maintain a flat end face on the return rod without spot welding or shims.
- Ensure smooth sliding and easy opening of the gate plate for three-plate molds.
- Arrange limit pull rods to prevent interference with the operator in three-plate molds.
- Ensure smooth oil and air passages for effective hydraulic ejector reset.
- Open an exhaust port at the bottom of the guide bush.
- Avoid installing positioning pins without proper clearance.
This dimension delves into the intricacies of gate design, runner systems, and sprue configurations, emphasizing their pivotal role in influencing the flow, distribution, and overall quality of the injected material. A meticulously crafted gating system is essential for achieving optimal mold fill, minimizing defects, and ensuring the production of high-quality molded components across diverse manufacturing applications.
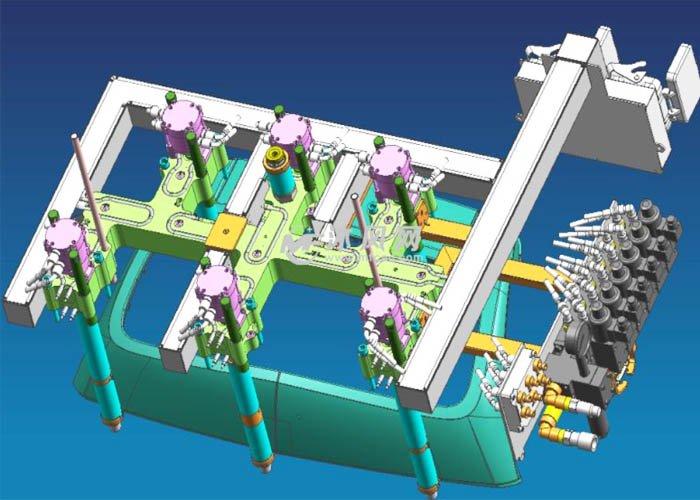
Hot Runner System
Hot Runner System emerges as a pivotal dimension within mold quality standards, spotlighting the transformative impact of advanced technology on optimizing plastic injection molding processes.
- Ensure the unobstructed functionality of the cooling and heating system.
- Guarantee a reliable seal, preventing system leakage under 0.5MPa pressure, and ensuring ease of repair.
- Align the size and shape of sealing grooves on the mold base with relevant standards.
- Apply butter to the sealing ring during placement, positioning it higher than the mold base surface.
- Construct water and oil channel spacers from corrosion-resistant materials.
- Implement a centralized water supply method for both the front and rear molds.
- Utilize J-type thermocouples that seamlessly integrate with the temperature control meter.
- Implement individual thermocouple control for each group of heating elements, strategically arranging thermocouple positions.
- Ensure the nozzle conforms to the specified design requirements.
- Position the hot runner securely, employing at least two positioning pins or fixing it with screws.
- Introduce a thermal pad between the hot runner and the template.
- Maintain a temperature control meter error within ±5°C, ensuring sensitive temperature control.
- Ensure that the cavity and nozzle mounting hole are seamlessly integrated.
- Bundle and cover hot runner wiring using a pressure plate.
- Clearly mark sockets of the same size.
- Sheath the control wire without any damage.
- Guarantee a reliable structure for the temperature control cabinet with securely tightened screws.
- Install the socket on bakelite, ensuring it does not exceed the maximum size of the formwork.
- Prohibit exposed wires outside the mold.
- Provide rounded transitions in all areas where the hot runner or stencil contacts the wires.
- Prior to template assembly, verify the absence of open circuits or short circuits in all lines.
- Ensure proper connections and good insulation for all wiring.
- After template mounting and clamping, conduct a thorough multimeter recheck of all circuits.
This dimension revolves around the intricate design and precise control of heated channels, nozzles, and manifold systems, fostering a paradigm shift in molding efficiency, reduced material waste, and enhanced product quality. A meticulously engineered Hot Runner System not only ensures superior temperature regulation but also contributes significantly to streamlining production, minimizing cycle times, and elevating the overall performance of molds across diverse industrial applications.
Mold Forming Part, Parting Surface, Exhaust Groove
Mold Forming Part, Parting Surface, and Exhaust Groove collectively stand as integral dimensions within mold quality standards, shaping the foundation for precision molding processes.
- Ensure a smooth and defect-free surface on both front and rear molds, free from uniformity issues, pits, rust, and other factors affecting appearance.
- Match the insert with the mold frame, maintaining a gap of less than 1 mm around the rounded corners.
- Keep the parting surface clean and well-maintained, avoiding the use of handheld grinding wheels to prevent air entrapment and ensuring a seamless seal without depressions.
- Set the depth of the exhaust groove below the plastic overflow value.
- Execute thorough research and precision matching of inserts, ensuring smooth placement and reliable positioning.
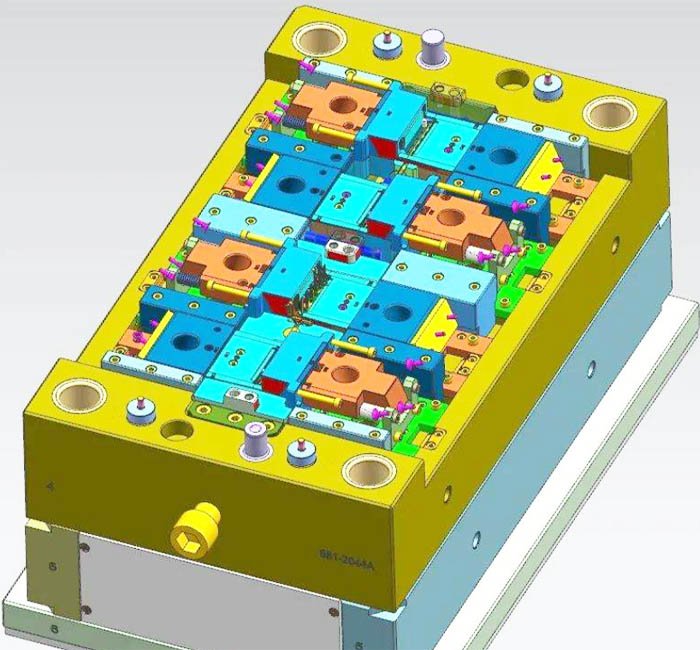
- Ensure reliable positioning and fixation of inserts, insert cores, and related components.
- Maintain consistency between the end face of the ejector pin and the core.
- Eliminate undercuts and chamfer defects on the forming parts of the front and rear molds.
- Ensure smooth rib ejection.
- In multi-cavity molds, guarantee symmetry between left and right parts, marking them appropriately as L or R according to customer requirements. Add markings as needed, ensuring they do not affect appearance and assembly, with a font size of 1/8.
- Ensure the locking surface of the mold base is comprehensive, with more than 75% of the area in contact.
- Arrange ejector rods near side walls, ribs, and bosses, utilizing larger ejector rods.
- Mark identical parts with numbers 1, 2, 3, etc.
- Thoroughly research and match touch-through surfaces, penetration surfaces, and parting surfaces.
- Adhere to design standards for the part of the parting surface sealant, with dimensions ranging from 1020mm for medium-sized molds, 3050mm for large molds, and machining for the rest to avoid voids.
- Ensure uniform skin texture and sandblasting to meet customer requirements.
- Implement anti-shrinkage measures for screws on products with specific appearance requirements.
- Utilize jacking pipes for screw columns deeper than 20mm.
- Maintain uniform product wall thickness with a deviation controlled below ±0.15mm.
- Limit the width of ribs to less than 60% of the appearance surface wall thickness.
- Apply reliable fixing methods for inserts on inclined tops and sliders.
- When inserting the front mold into the rear mold or vice versa, incorporate inclined surfaces for locking and machining to prevent voids.
These aspects intricately define the structural and functional characteristics of molds, influencing the final product’s quality, dimensional accuracy, and overall manufacturing efficiency. From the meticulous design of forming parts to the strategic configuration of parting surfaces and the incorporation of efficient exhaust grooves, this dimension plays a critical role in achieving seamless mold operation and delivering consistently superior molded components across diverse industrial applications.
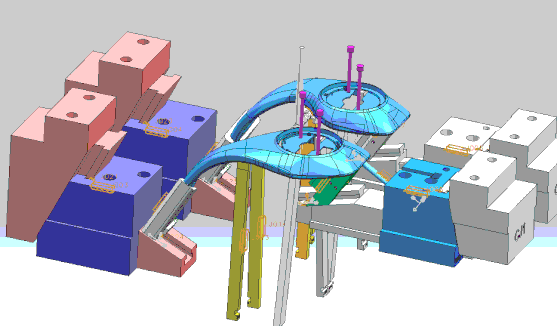
Injection Production Process
The Injection Production Process stands as a pivotal dimension within mold quality standards, encompassing the intricate stages of injecting molten material into molds to shape complex components.
- Ensuring the stability of injection molding production and the repeatability of process parameter adjustments represents fundamental quality within standard injection molding conditions.
- Maintain the injection pressure during production below 85% of the maximum rated injection pressure of the injection molding machine.
- For injection production, regulate the injection speed of the mold within the range of 10% to 90% of the rated maximum injection speed, specifically avoiding values below 10% or exceeding 90% during the three-quarter stroke.
- Limit the holding pressure during injection molding production to generally not exceed 85% of the actual maximum injection pressure.
- Ensure that the clamping force applied to the mold during injection molding production remains below 90% of the rated clamping force for the specific model.
- Facilitate easy and safe removal of the product and nozzle material during the injection molding production process, with a recommended removal time of generally not exceeding 2 seconds.
- Simplify the installation of inserts for molds, ensuring reliable fixation of inserts during production.
This dimension addresses the meticulous orchestration of parameters, precision control, and seamless coordination required for optimizing the molding process. From material preparation to injection, cooling, and demolding, the injection production process plays a central role in determining the final product’s quality, dimensional accuracy, and overall manufacturing efficiency across diverse industrial applications.
Packing And Shipping
Packing and Shipping emerge as crucial dimensions within mold quality standards, marking the final stages of a meticulous journey from design to production.
- Conduct a thorough cleaning of the mold cavity, applying anti-rust oil for protection.
- Ensure lubrication of sliding parts for smooth operation.
- Seal the sprue sleeve inlet with grease.
- Install a clamping plate on the mold, adhering to design specification requirements.
- Provide a comprehensive set of spare parts and wearing parts, accompanied by a detailed list including supplier names.
- Seal the inlet and outlet of mold water, liquid, gas, and electricity to prevent the entry of foreign matter.
- Apply spray paint to the outer surface of the mold, adhering to customer requirements.
- Package the mold meticulously with moisture-proof, waterproof, and shock-resistant materials, meeting customer specifications.
This dimension encapsulates the protocols and practices employed in packaging molded components and orchestrating their safe transport to end-users or assembly facilities. The effectiveness of packing methods, protective measures, and adherence to shipping standards not only safeguard the integrity of the molded products but also play a pivotal role in ensuring customer satisfaction and the successful deployment of molds across diverse industrial applications.
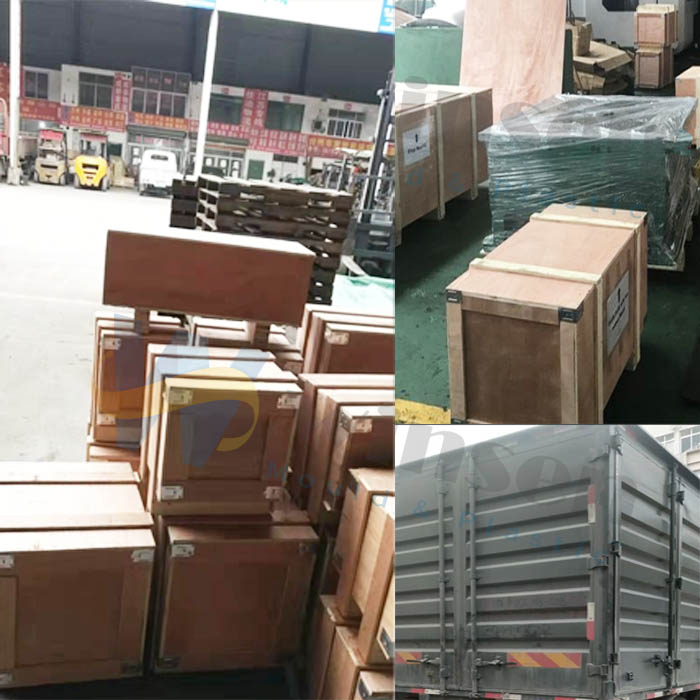
WS MOLD strictly follow quality standards of plastic injection moulds,so we can ensure the smoothness of the production process, complete the mold production tasks safely and quickly
Injection Mold Quality Management Mold Assembly Workshop
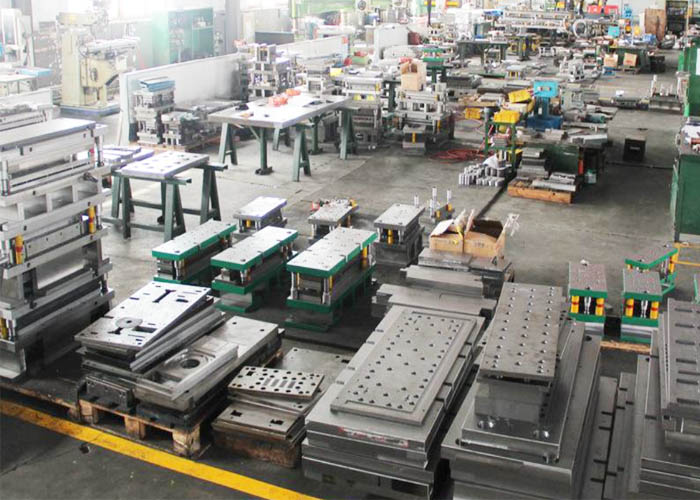
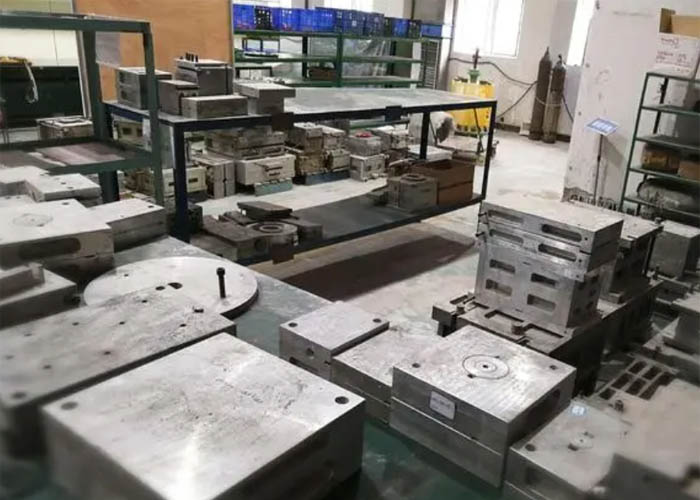
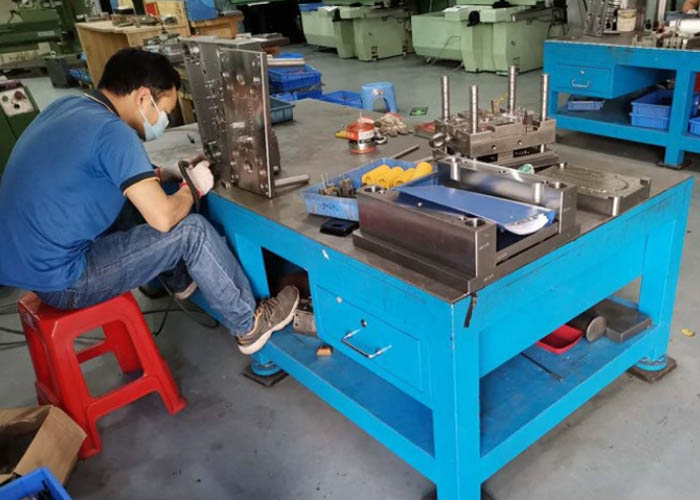
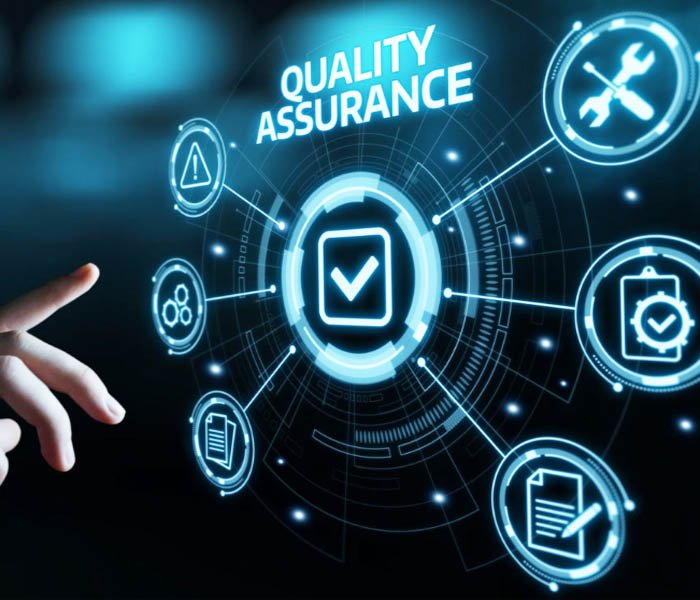
Seven Key Principles for Effective Management Injection Mold Quality
In the world of injection molding, effective quality management is the keystone for success. Seven Key Principles govern this process, shaping the essence of superior injection mold quality. From customer-centric focus to strategic leadership involvement and shared responsibility for quality, these principles form a concise roadmap for achieving excellence in injection mold management. Let’s explore these principles to understand how they collectively elevate the standards of quality in the injection molding realm.
- Centering on customer satisfaction, a customer-oriented approach serves as the benchmark for quality standards.
- The strategic significance of quality management throughout project management is underscored by the emphasis placed by organizational leaders. It can be asserted that the project’s quality is heavily reliant on the priority given by top executives.
- Taking ownership of elucidating quality issues is not confined to quality inspectors alone; rather, it is a shared responsibility that extends to every individual in the organization.
- Process management shifts the focus of quality management from result inspection to continuous process monitoring, encompassing two key aspects.
A. Temporally, the entire project implementation is viewed as a process of interconnecting tasks. Analyzing the work process enables the identification and streamlining of ineffective links, optimizing division of labor interfaces, fostering goal synergy, and minimizing time wastage.
B. Spatially, the project is seen as an integrated activity involving various resources. Through analysis, functional indicators of elements are identified and optimized, ensuring strict checks and strengthening interfaces for effective communication, information sharing, and utilization of technical resources to uphold final product quality.
- Realistic data emphasizes that effective decisions must rely on facts and quantitative analysis, rather than subjective concepts and assumptions.
- Supplier mutual benefit involves establishing long-term, mutually beneficial partnerships with upstream suppliers.
- Continuous improvement entails treating the pursuit of quality excellence as the organization’s eternal goal. Identifying improvement opportunities, refining quality goals, and implementing continuous improvement measures create a spiral of quality enhancement.
In conclusion, these Seven Key Principles for Effective Management encapsulate the essence of achieving excellence in injection mold quality. By embracing customer-centricity, recognizing the strategic role of leadership, fostering collective responsibility, and emphasizing process management, realistic data, supplier mutual benefit, and continuous improvement, organizations can navigate the intricate landscape of injection molding with precision and success. These principles serve as a comprehensive guide, not only transforming the focus from result inspection to continuous process monitoring but also fostering a culture of perpetual enhancement. As we adhere to these principles, we pave the way for a future where injection mold quality becomes synonymous with unparalleled precision, efficiency, and customer satisfaction.
Components of Injection Mold Quality Management
The entire quality management process seamlessly aligns with the three pivotal stages of project management: planning, implementation, and control. To draw a vivid analogy, consider these components as counterparts to the legislative, law enforcement, and judiciary facets. Quality planning is akin to legislation, setting the standards. Quality assurance operates as law enforcement, striving to promote adherence to these standards, while quality control functions as the judiciary, aiming to ensure justice by suppressing deviations. The quality assurance system acts as the frontline defender, preserving the boundaries of established quality standards.
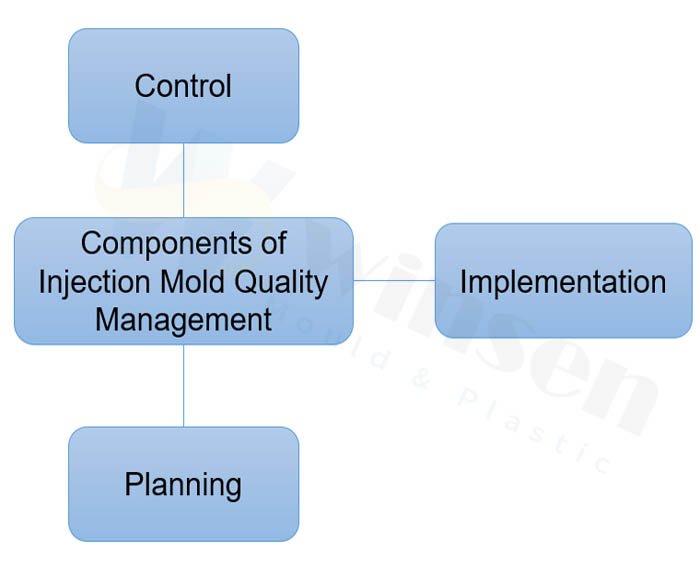
The nucleus of comprehensive quality management lies in the establishment and continual enhancement of the quality management system. This pivotal aspect forms a robust foundation for undertaking quality assurance activities with diligence and effectiveness.