SMC molding process and its advantages,SMC, which stands for Sheet Molding Compound, is a composite material used in manufacturing processes to produce high-strength, lightweight, and complex-shaped parts and components. The SMC compression molding process involves several steps, and it offers various advantages:
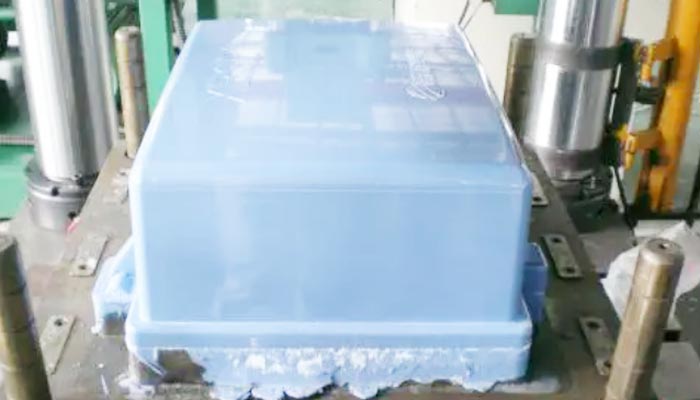
SMC molding process and its advantages
1. Material Composition
SMC is typically composed of a mixture of thermosetting resins (such as polyester or vinyl ester), chopped glass fibers, mineral fillers, and additives. This composition gives SMC its strength, rigidity, and excellent corrosion resistance.
2. Preparation of SMC
The SMC material is prepared by blending the various components into a thick, dough-like compound. This compound is then formed into sheets or rolls, which are used as feedstock for the molding process.
3. Molding Process
The SMC molding process involves the following steps:
a. Cutting and Layering: The SMC sheets or rolls are cut into the desired shape and size, depending on the part being produced.
b. Placing in the Mold: These cut pieces are placed in a mold cavity, either manually or using automated equipment.
c. Molding Press: The mold, with the SMC inside, is placed in a hydraulic press. The press applies heat and pressure to the SMC material, causing it to flow and fill the mold cavity completely.
d. Curing: The heat from the press causes the thermosetting resin to cure and harden. This step is critical for the final strength and integrity of the part.
4. Advantages of SMC Molding
a. High Strength: SMC parts have excellent tensile and flexural strength, making them suitable for applications where structural integrity is crucial.
b. Complex Shapes: SMC can be molded into complex shapes and intricate geometries with high precision. This capability reduces the need for secondary machining operations.
c. Lightweight: Despite their high strength, SMC parts are lightweight compared to many metals, making them ideal for applications where weight reduction is essential.
d. Corrosion Resistance: SMC is highly resistant to corrosion, making it suitable for outdoor and harsh environmental conditions.
e. Excellent Electrical Insulation: SMC has excellent electrical insulation properties, making it suitable for electrical and electronic enclosures.
f. Low Tooling Costs: While the initial cost of molds can be relatively high, they are durable and can produce a large number of parts, making the per-part tooling cost lower over time.
g. Design Flexibility: SMC allows for a high degree of design flexibility, including the incorporation of ribs, bosses, and other structural features.
h. Good Surface Finish: SMC parts typically have a smooth, paintable surface finish, reducing the need for post-production finishing.
i. Recyclability: SMC scrap material can often be recycled and reused, reducing waste.
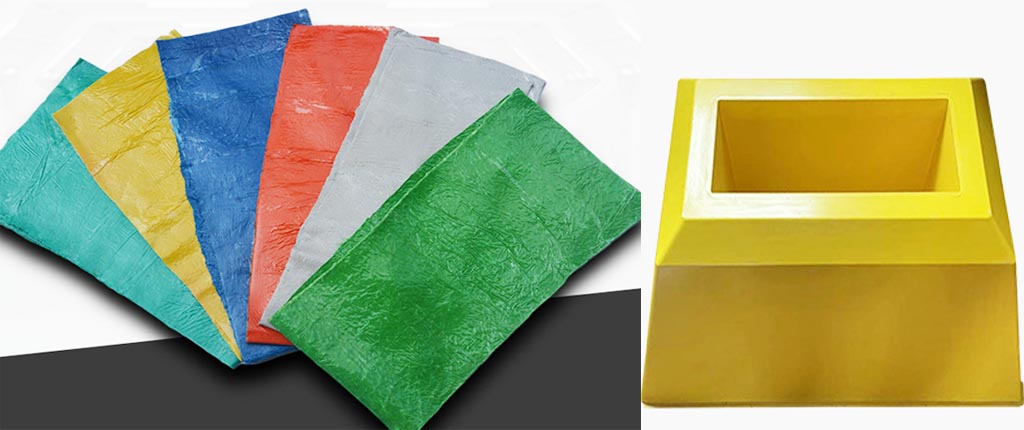
The CF-SMC compression molding process is to process continuous carbon fibers and chopped fibers through different forms of hybrid processing and then prepare composite parts with complex shapes and high dimensional accuracy requirements. Here, continuous fibers are used as reinforcements to make up for chopped fibers. The mechanical weakness of the SMC has played a part of the purpose of reinforcement, and its mechanical function is much higher than that of the traditional SMC preparation technology.
The SMC molding process has many advantages, such as its simple operation, easy automation, short production cycle (3-5min), and the ability to form products with a smooth surface and a complex structure. Good: Excellent electrical insulating properties, mechanical properties, thermal stability, chemical resistance.
The SMC process is not a composite material molding process. After more than half a century of development and continuous optimization, it has now been used in the automotive industry, construction industry, communication engineering, electronics, electrical and other industries.
SMC molding is commonly used in various industries, including automotive, aerospace, electrical, and construction, to manufacture components such as automotive body panels, electrical enclosures, and structural parts. Its combination of strength, versatility, and cost-effectiveness makes it a popular choice for producing a wide range of parts and products.