Tips for choosing the right steel of plastic molds.When choosing the right steel for your plastic mold, you need to consider several key factors that will directly impact the mold’s performance, lifespan, and ultimately production cost. In this blog, we’ll share some practical tips on how to choose the right steel.
The working conditions of plastic injection molds are different from cold stamping dies. In generally, they are work at 150 to 200 degrees Celsius. In addition to a certain pressure, they must also be affected by temperature. According to the different use conditions and processing methods of plastic molds, the basic performance requirements of steel for plastic moulds are roughly summarized as follows:
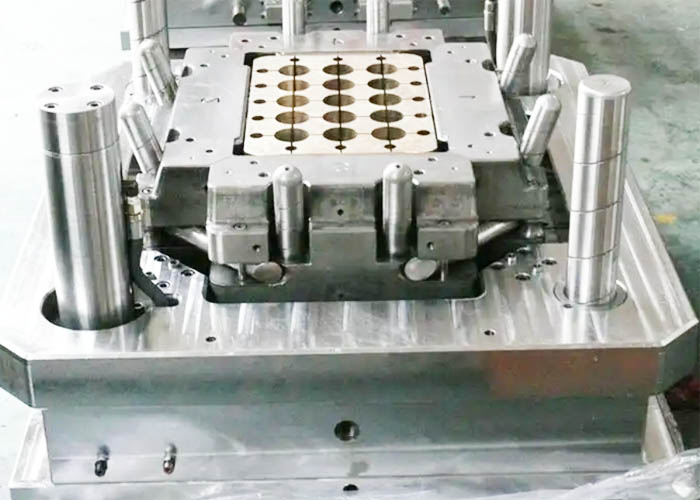
Tips for choosing the right steel of plastic molds
1. Determine the purpose of the mold
First, you need to figure out what type of plastic product the mold will be used for. Different types of plastics have different requirements for molds. Some plastics may be more abrasive to molds and require more wear-resistant steel, while other plastics may require greater corrosion resistance. Clear purpose objectives will help guide your steel selection.
2. Consider production volume
Production volume is one of the key factors in selecting steel. High-volume production often requires the use of more wear-resistant, longer-lasting steel because the molds will be used frequently. Conversely, low-volume molds can use lower-cost steels because they are not subject to as much wear and tear.
3. Determine required hardness
The surface hardness of the mold is critical to its performance. Typically, harder steels are more resistant to wear, but can also be brittle. Therefore, you need to balance hardness and toughness to ensure that the mold is not prone to wear or breakage during production.
Good thermal stability,the shape of the parts of the plastic injection mold is often complex, and it is difficult to process after quenching. Therefore, it should be selected as far as possible with good thermal stability. The change rate is small, the metallographic structure and the mold size are stable, and the processing can be reduced or no longer required to ensure the mold size accuracy and surface roughness requirements.
Sufficient surface hardness,hardness of the plastic mold is usually below 50-60HRC, and the heat-treated mold should have sufficient surface hardness to ensure that the mold has sufficient rigidity.
4. Consider corrosion resistance and wear resistance
If the mold will be in contact with corrosive plastics or chemicals, then you need to choose steel with good corrosion resistance to extend the life of the mold and ensure production quality.
Due to the filling and flow of plastic, the mold is required to withstand large compressive stress and friction during work, and the mold is required to maintain the stability of shape accuracy and dimensional accuracy to ensure that the mold has a sufficient service life. The wear resistance of the mold depends on the chemical composition of the steel and the hardness of the heat treatment, so enhancing the hardness of the mold is beneficial to enhance its wear resistance.
Carbon steel of grade 50 has certain strength and wear resistance, and is mostly used for mold base material after quenching and tempering. High carbon tool steel and low alloy tool steel have high strength and wear resistance after heat treatment, and are mostly used for forming parts. However, high carbon tool steel is only suitable for the manufacture of formed parts with small size and simple shape due to its large deformation during heat treatment.
5. Importance of thermal conductivity
The thermal conductivity of steel affects how quickly the plastic cools. For molds that require rapid cooling, it may be more appropriate to choose a steel with good thermal conductivity, as it helps increase production efficiency.
6. Cost factors
The cost of steel is also a key factor. High-performance, wear-resistant steel typically costs more but can extend the life of the mold. When selecting steel, there is a trade-off between production costs and tool life.
7. Consider mold manufacturing technology
The manufacturing technology of the mold will also affect the choice of steel. Certain manufacturing techniques may require specific types of steel, so it’s important to work with mold designers and manufacturers to make informed choices.
8. Maintenance and Lubrication
Last but not least, ensure proper maintenance and lubrication of the mold surface. This can extend the life of the mold and improve production efficiency. Make sure molds are kept clean at all times and undergo regular maintenance.
9. Excellent machinability
In addition to EMD processing, plastic molding moulds also require certain cutting processing and fitter repair. In order to prolong the service life of cutting tools, enhance cutting performance, and reduce surface roughness, the hardness of plastic mould steel must be appropriate.
10.Good polishing performance
For high quality 2 color injection plastic products, the roughness value of the cavity surface is required to be small. For example, the surface roughness value of the injection mould cavity is required to be less than Ra0.1~0.25, and the optical surface requires Ra<0.01nm, and the cavity must be polished to reduce the surface roughness value. The steel selected for this purpose requires less material impurities, fine and uniform structure, no fiber orientation, and no pitting or orange peel defects during polishing.
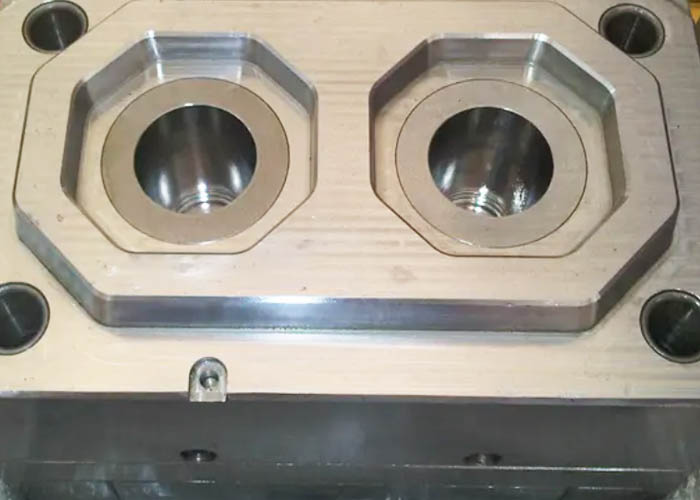
With the development of the plastics industry, the requirements for the complexity and precision of plastic products are getting higher and higher, and higher requirements are also placed on the two-color injection mold materials. For the manufacture of complex, precise and corrosion-resistant plastic molds, pre-hardened steel (such as PMS), corrosion-resistant steel (such as PCR) and low-carbon maraging steel (such as 18Ni-250) can be used, all of which have better performance,Machining, heat treatment and polishing properties and high strength.
In addition, when selecting materials, it is necessary to consider preventing scratches and gluing. If there is relative movement between the two surfaces, try to avoid selecting materials with the same structure. In special cases, one side can be plated or nitrided to make the two sides different. surface structure.
To summarize, choosing the right steel for a plastic mold requires careful consideration of several factors to ensure the mold performs well in production. Working with experienced mold designers and manufacturers and making informed decisions based on the needs of your specific project will help ensure optimal mold performance, longevity and profitability.