TPE Plastic Injection Moulding Mold Manufacturer
In the dynamic world of polymer engineering, Thermoplastic Elastomers (TPE) have emerged as a revolutionary material, offering a unique combination of properties that bridge the gap between traditional plastics and rubbers. As a leading manufacturer of TPE plastic injection moulding molds, our company is at the forefront of this innovation, specializing in the design and production of high-quality TPE Injection moulds that cater to a diverse range of industries.
Table of Contents
ToggleWhat Is Thermoplastic Elastomers(TPE)
Thermoplastic elastomer(TPE/TPR), also known as artificial rubber or synthetic rubber. Its products not only have the excellent properties of high elasticity, aging resistance and oil resistance of traditional cross-linked vulcanized rubber, but also have the characteristics of convenient processing and wide processing methods of ordinary plastics. It can be produced by injection molding, extrusion, blow molding and other processing methods, and 100% of the edges and corners of the sprue can be directly reused after being crushed. It not only simplifies the processing process, but also reduces the processing cost. Therefore, thermoplastic elastomer TPE/TPR material has become the latest material to replace traditional rubber. It is environmentally friendly, non-toxic, comfortable to the touch, and exquisite in appearance, making the product more creative. Therefore, it is also a more humane and high-grade new synthetic material, and a world-standard environmentally friendly material.
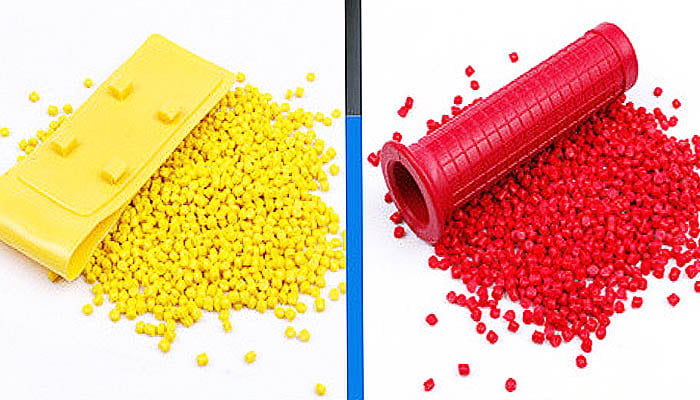
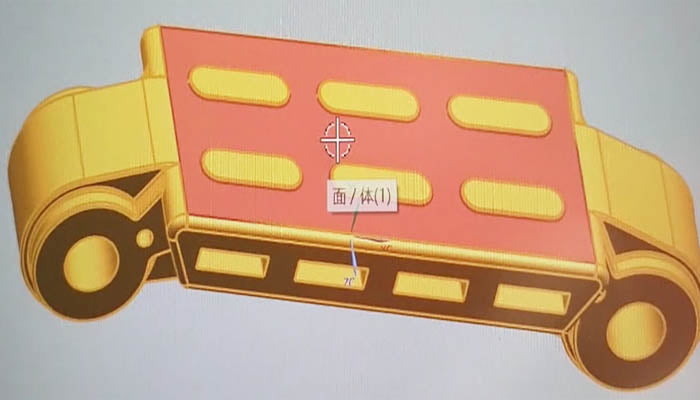
TPE type classification
Thermoplastic elastomers (TPE) are a type of plastic material with rubber elasticity that can be plasticized and molded at high temperatures.TPE’s widespread global acceptance is largely due to its recyclability. Similar to other thermoplastics, TPE can be reshaped and repurposed through the recycling process. This material is capable of being formed into various configurations when heated, utilizing methods such as injection molding, blow molding, extrusion, and rotational molding.
TPE encompasses 6 main types, which include Thermoplastic Vulcanizates (TPV), Thermoplastic Urethanes (TPU), Thermoplastic Olefins (TPO), Styrenic Block Copolymers (SBC), Copolyester Elastomer (COPE), and Polyether Block Amide (PEBA). These categories are distinguished by their unique chemical structures and compositions.
Thermoplastic vulcanizate (TPV)
TPV is prepared by a dynamic vulcanization process, in which the rubber phase forms cross-linked rubber domains in the plastic matrix.It combines the elasticity of rubber with the processing convenience of plastic.Commonly used in automotive seals, gaskets, medical products, etc.
Thermoplastic polyurethane (TPU)
TPU is formed by the reaction of polyester or polyether polyols with diisocyanates.It has good wear resistance, oil resistance and flexibility.Applied to footwear, hoses, cable sheathing, medical equipment, etc.
Thermoplastic olefin (TPO)
TPO is a blend of polyolefin plastic and rubber, usually composed of polypropylene (PP) and ethylene-propylene rubber (EPDM).It provides good weather resistance and chemical resistance.Commonly used in automotive interiors, exteriors, building materials, etc.
Styrenic block copolymer (SBC)
SBC includes styrene-butadiene-styrene (SBS) and styrene-isoprene-styrene (SIS), etc.They have good elasticity and low temperature properties.Used in adhesives, sealing materials, asphalt modifiers, etc.
Copolyester elastomer (COPE)
COPE is a polyester block copolymer formed by aromatic diols and aromatic diacids or their esters.It has excellent heat resistance, chemical resistance and mechanical properties.Used in high temperature applications such as automotive engine parts, electronic equipment, etc.
Polyether block amide (PEBA)
PEBA is a block copolymer formed by the reaction of polyether diols and diisocyanates.It has extremely high elasticity, flexibility and low temperature performance.Used in sports equipment, medical equipment, films and fibers, etc.
Each type of TPE has its own unique performance characteristics and is suitable for different applications. Choosing the right TPE type usually depends on the application needs and performance requirements of the final product.
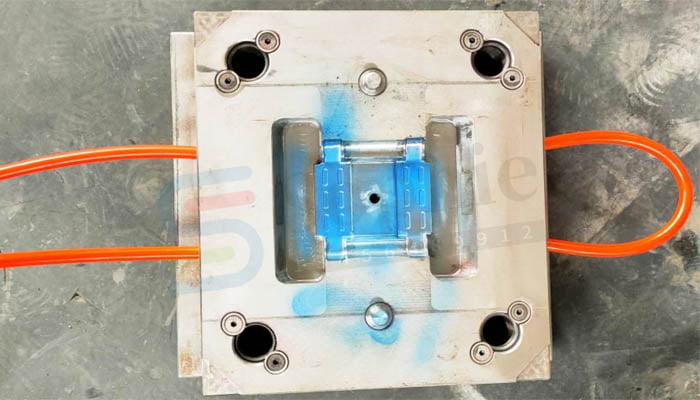
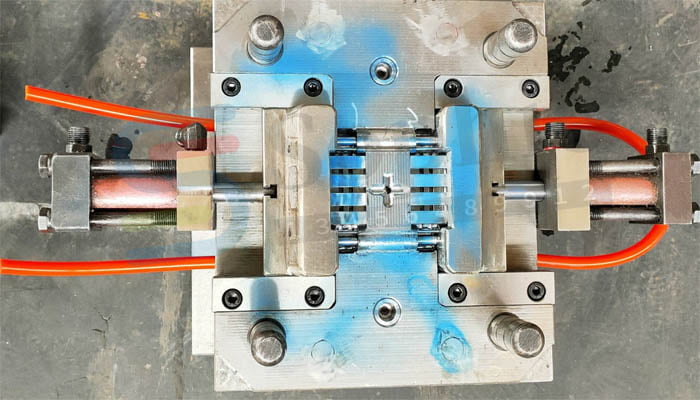
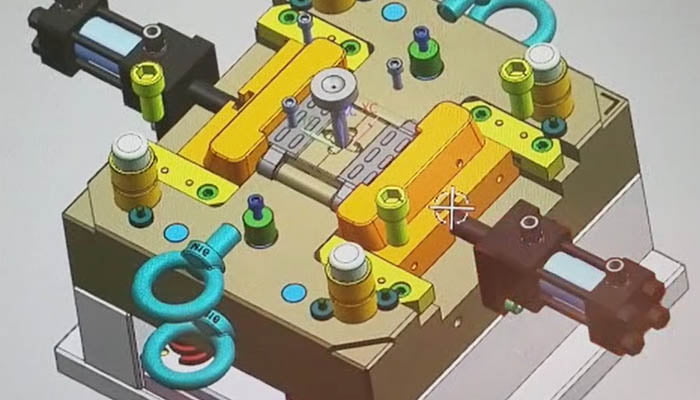
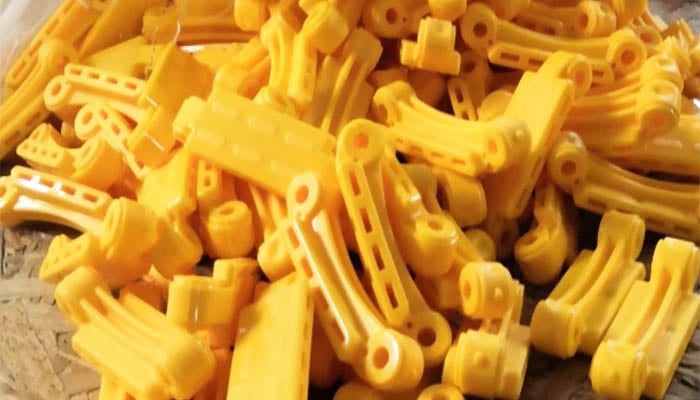
Key Factors Designing TPE Plastic Injection Moulding Mold
When designing TPE injection molds, in order to improve production efficiency and reduce costs, the following key factors need to be considered:
Mold design
Reasonable mold design is crucial to improving production efficiency. The flow channel design should be ensured to be optimized to reduce material flow resistance, speed up filling, and reduce material waste. At the same time, choosing mold materials with good wear resistance and thermal conductivity can reduce mold wear and heat loss and improve molding efficiency. The design of the cooling system of the mold is also very important. Effective cooling can shorten the molding cycle and improve production efficiency.
Injection molding machine selection
Choose an injection molding machine suitable for the characteristics of TPE materials. Modern injection molding machines have accurate control systems and fast processing speeds, which can significantly improve production efficiency. The stability and durability of equipment are also key to ensuring long-term production.
Processing parameters
Controlling the processing temperature is the key to ensuring full plasticization and flow of TPE materials. Appropriate processing temperature can reduce processing defects and improve product quality. Adjusting the injection speed and pressure can speed up the filling and flow of materials in the mold and shorten the molding cycle while ensuring product quality.
Raw material formula
Choosing appropriate TPE materials and adding appropriate amounts of processing aids can improve the fluidity and processing performance of TPE plastics, reduce processing difficulty, and improve processing efficiency. For example, adding lubricants can reduce material friction during machining.
Quality control
Establishing a complete quality control system is of great significance to ensure the quality of TPE injection molded parts. Through strict quality control processes, we ensure that every process meets quality requirements to produce high-quality injection molded parts.
Cost control
Injection molding cost control involves many aspects such as mold manufacturing, material selection, equipment costs, labor costs, etc. Injection molding costs can be effectively reduced by optimizing design, selecting appropriate materials, improving equipment usage efficiency, and reducing labor costs.
Preventive maintenance
Regular maintenance of injection molding machines and molds to ensure stable and reliable performance can reduce equipment failures and production delays, thereby reducing costs.
Through the above measures, we can improve TPE injection molding production efficiency, reduce production costs and create greater economic benefits for the enterprise while ensuring product quality.
As a Thermoplastic Elastomers (TPE) Plastic Injection Moulding Mold Manufacturer, we are proud of our role in shaping the future of polymer engineering. Our commitment to innovation, quality, and sustainability drives us to continuously improve our processes and technologies. We look forward to continuing our journey at the forefront of TPE moulding, working with our clients to create products that are not only high-performing but also responsible and sustainable.
In conclusion, the world of TPE moulding is an exciting and rapidly evolving field, with new applications and advancements emerging all the time. As a leading manufacturer of TPE injection moulds, we are dedicated to staying at the cutting edge of this technology, providing our clients with the highest quality moulds and supporting them in their quest for innovation and excellence. Together, we are shaping a brighter, more sustainable future for the manufacturing industry.