successful mold polishing requires a combination of skill, precision, and attention to detail. By identifying common problems and implementing the suggested solutions, manufacturers can ensure that their molds receive the necessary treatment to produce high-quality products with the desired surface finish and functionality. Regular training, proper tool selection, and a commitment to continuous improvement are key factors in mastering the art of mold polishing.
There are often some problems in the process of injection and compression mold polishing, so how to solve these problems?
Table of Contents
ToggleTroubleshooting Tips for Common Mold Polishing Issues
1. Uneven Surface Finish
One of the most prevalent issues in mold polishing is achieving an uneven surface finish. This can result from inconsistent pressure, improper tooling, or inadequate polishing techniques.
To address this problem, ensure uniform pressure throughout the polishing process. Use specialized polishing tools appropriate for the material and intricacies of the mold. Implement proper polishing techniques, such as alternating the polishing direction and progressively using finer abrasives.
2. Excessive polishing
The biggest problem in the polishing process is “overpolishing”, which means that the longer of polishing time, the worse the quality of mold surface. it often occurs mostly in mechanical polishing.
Exercise caution when removing material from the mold’s surface. Utilize finer grit abrasives and lighter pressure as you approach the final stages of polishing. Regularly inspect the mold’s details and stop polishing as soon as the desired finish is achieved.
3. Scratches and Blemishes
Scratches and blemishes can appear on the mold surface due to the use of incorrect abrasives, aggressive polishing, or inadequate cleaning between polishing stages.
Select the right abrasives based on the material being polished. Begin with coarser abrasives and gradually move to finer ones. Use controlled pressure and consistent strokes while polishing to avoid over-aggressiveness. Clean the mold thoroughly between each stage to prevent coarse particles from causing scratches.
4. Inconsistent Shine
nconsistent shine or glossiness across the mold surface can occur due to variations in pressure, tooling, or polishing compounds.
Maintain a consistent polishing technique, including pressure and tooling, throughout the process. Choose appropriate polishing compounds or slurries for the material. Perform a final polishing stage with a high-quality compound to ensure uniform shine.
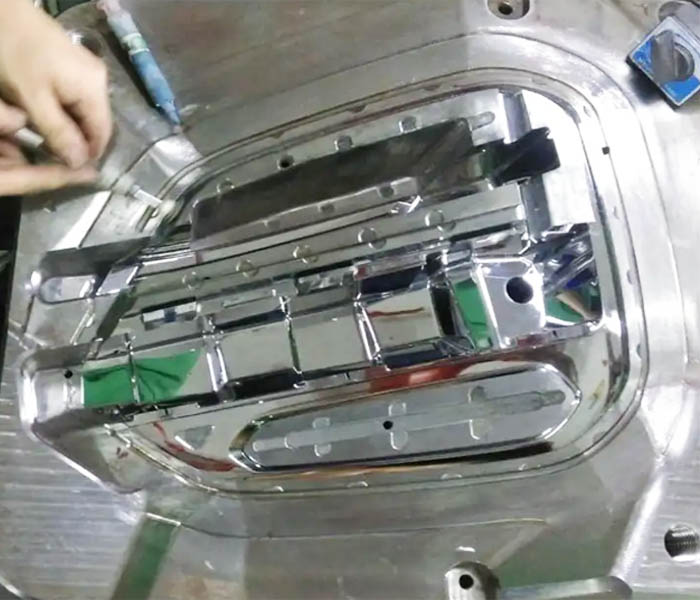
Reasons for "orange peel" in the workpiece
The irregular rough surface is called “orange peel”. There are many reasons for “orange peel”. The most common reason is due to overheating of the mold surface or excessive carburization, excessive polishing pressure and excessive polishing time. The main cause of “orange peel”. For example: polishing the polishing wheel, the heat generated by the polishing wheel can easily cause “orange peel”. Harder steel can withstand greater polishing pressure, while relatively soft steel is prone to over-polishing. Studies have shown that the time for over-polishing varies depending on the hardness of the steel.
Measures to eliminate the "orange peel" of the workpiece
When it is found that the surface quality is not good, many people increase the polishing pressure and prolong the polishing time, which tends to make the surface quality worse.
The following methods can be used to remedy the above problems:
(1) Remove the defective surface, grind the particle size a little coarser than the previous one, and then grind it, and the polishing force is lower than the previous one.
(2) Stress relief is carried out at a temperature 25°C lower than the tempering temperature. Before polishing, use the finest grit size for grinding until a satisfactory effect is achieved, and finally polish with a lighter force.
The reason for formation of "pitting" on the surface of workpiece
Due to some non-metallic impurities in the steel, usually hard and brittle oxides, they are pulled out from the steel surface during the polishing process to form micro-pits or pitting corrosion. The main factors for “pitting corrosion” are as follows:
(1) The polishing pressure is too large and the polishing time is too long.
(2) The purity of the steel is not enough, and the content of hard impurities is high.
(3) The mold surface is rusted.
(4) The black leather is not removed.
Measures to Eliminate Pitting Corrosion of Workpieces
(1) Carefully re-grind the surface, the grit size is a little coarser than the one used previously, and use a soft and sharp whetstone for the final step of grinding before proceeding with the polishing procedure.
(2) When the grit size is less than 1 mm, the softest polishing tool should be avoided.
(3) Use the shortest polishing time and minimum polishing force as possible.
The polishing of the cavity in the mold manufacturing process is a very important process, which is related to the quality and life of the mold, and also determines the quality of the product. Mastering the working principle and process of polishing and choosing a reasonable polishing method can improve the quality and life of the mold, and then improve the quality of the product.