UHMWPE & Kevlar/Aramid fiber Ballistic Helmet Mold
UHMWPE & Kevlar/Aramid fiber Ballistic Helmet Mold factory in China.In the realm of personal protective equipment, the manufacturing of ballistic helmets is a critical industry that demands precision, innovation, and a deep understanding of advanced materials. At the heart of this industry lies the bulletproof products mold, the foundational tool that shapes the future of safety. This blog post takes you through the intricate process of creating UHMWPE & Kevlar/Aramid fiber ballistic helmet molds, a technology that is now being exported to Russia, showcasing the global reach of our manufacturing expertise.
Table of Contents
ToggleDifference of UHMWPE and Kevlar/Aramid Fiber Material
Ultra-high molecular weight polyethylene (UHMWPE) is a lightweight, high-strength material known for its exceptional impact resistance. When combined with Kevlar or Aramid fibers, a synthetic material renowned for its heat resistance and tenacity, the result is a helmet that offers unparalleled protection against ballistic threats.
Kevlar and Aramid fibers are woven into a fabric that can stop bullets and shrapnel, making them ideal for ballistic helmets. The integration of these fibers with UHMWPE enhances the helmet’s ability to absorb and disperse the energy from an impact, ensuring the wearer’s safety.
The Manufacturing Process: Helmet Mold Design and Production
The production of a ballistic helmet begins with the design of the mold. This aramid helmet mold must be precise to ensure that the helmet’s shape not only provides optimal protection but also fits comfortably on the wearer’s head. The kevlar helmet mold is designed using advanced computer-aided design (CAD) software, which allows engineers to simulate the helmet’s performance under various impact scenarios.
Once the design is finalized, the UHMWPE & Kevlar/Aramid fiber Ballistic Helmet Mold is created using high-precision CNC machines. The mold is then used to shape the UHMWPE and Kevlar/Aramid composite material. The process involves layers of the material being placed into the mold and subjected to high temperatures and pressures to bond the layers together, creating a single, robust helmet shell.
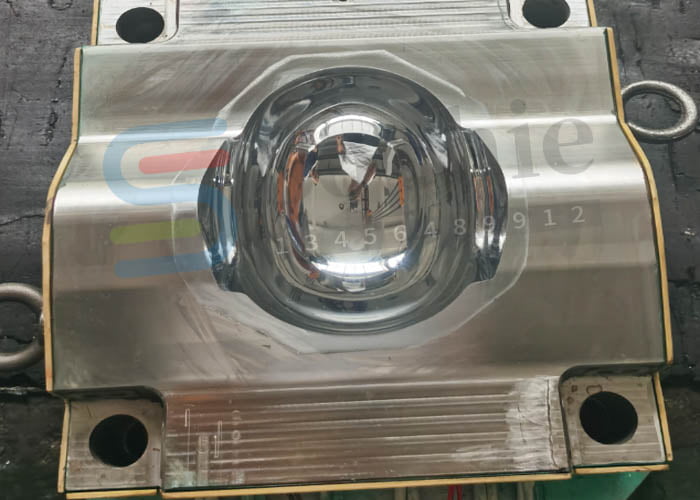
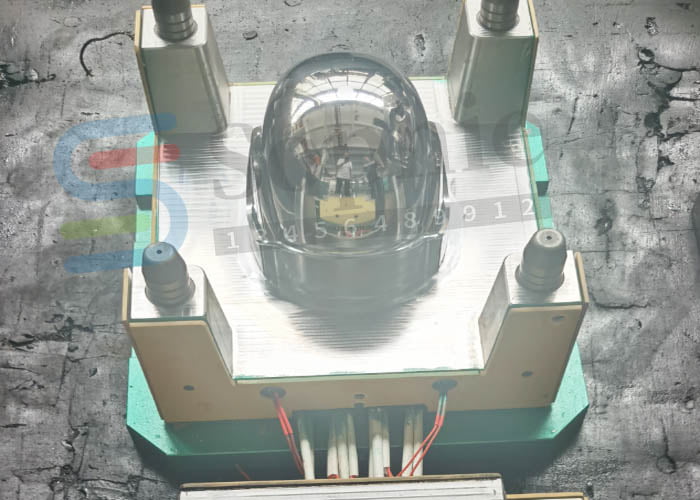
Quality Assurance and Testing
Before any helmet mold leaves our facility, it undergoes a rigorous series of quality assurance tests. These tests include dimensional accuracy checks, surface finish evaluations, and durability tests to simulate the conditions the aramid helmet mold will face in its lifecycle. Our commitment to quality ensures that every helmet produced will meet the stringent requirements of our clients.
Exporting to Russia: A Global Commitment to Safety
The export of our UHMWPE & Kevlar/Aramid fiber ballistic helmet molds to Russia is a testament to our global reach and the recognition of our expertise in the field of protective equipment manufacturing. As these molds cross borders, they carry with them the promise of safety and security for the users who rely on the helmets they produce.
The UHMWPE & Kevlar/Aramid fiber ballistic helmet mold is more than just a tool; it is a testament to the innovation and precision that drive our industry. As these molds find their way into the hands of manufacturers around the world, they represent a global commitment to enhancing the safety and protection of those who serve on the frontlines.
Our dedication to crafting the highest quality molds is a reflection of our commitment to excellence. As we continue to push the boundaries of what is possible in the field of protective equipment, we remain steadfast in our mission to provide the best possible tools for those who protect and serve.