Compression molding is the process of molding that put a preheated polymer(Powder, granular or fibrous plastic) is placed into heated mold cavity,and then closes the mold to compressed so that have the material contact all areas of the mould for shape and solidify it. The compression molding process can be used for the production of thermoset plastic products, thermoplastic products and rubber material products.
This Production can be produce parts with a wide lengths,thicknesses and complexities products. Compression forming products has a high strength,making it an attractive process for a number of different industries.
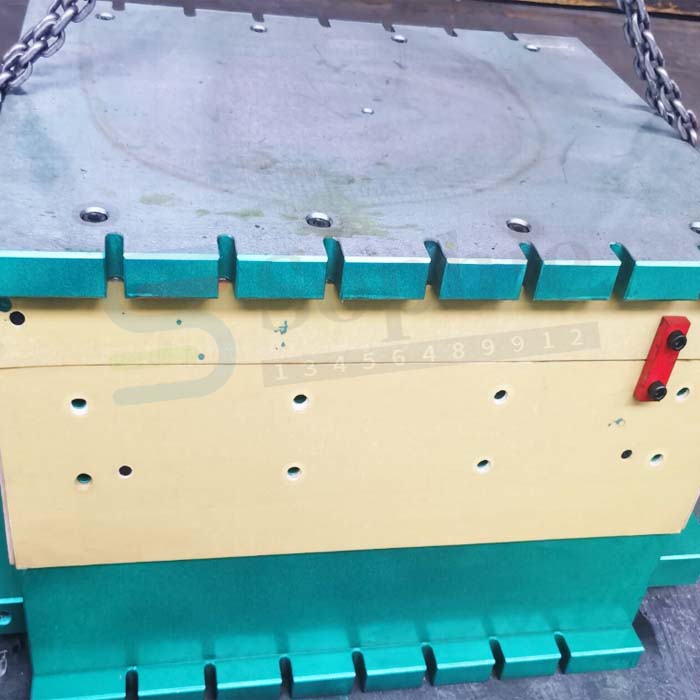
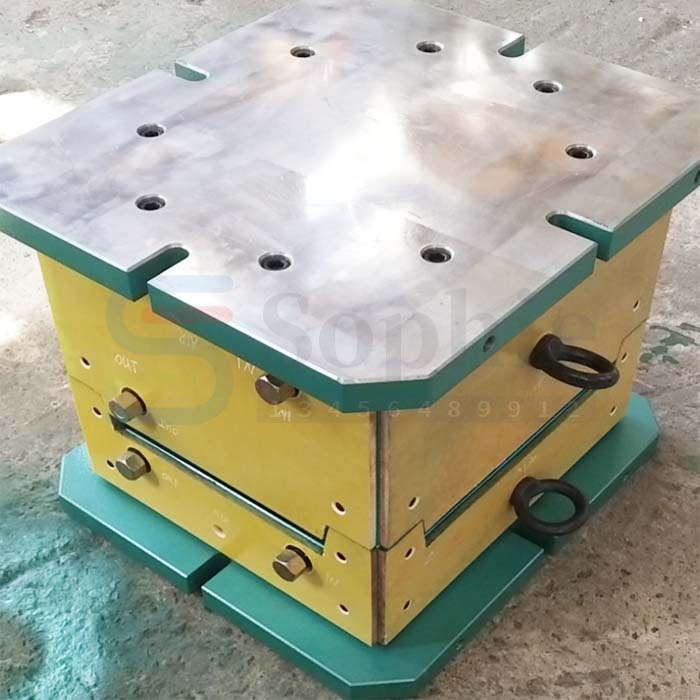
What is compression molding
Thermoset composites are the most commonly used material type in compression molding.
Compression Molded bulletproof helmet is a great example of made by compression molding.If you have any questions or would like to order any of compression ballistic helmet mould, please contact us by free ! We will ensure you get the perfect mold to produce your military helmets.
Composite materials can be successfully applied to the manufacturing process in the Military field .We are constantly optimizing for the prepreg compression molding technology and achieved good results.
Table of Contents
ToggleApplications of compression molding
Mainly used as structural parts, connectors, protective parts and electrical insulation parts. Widely used in industry, agriculture, transportation, electrical, chemical, construction, machinery and other fields. Due to the reliable quality of molded products, they have also been used in weapons, aircraft, missiles, and satellites.
Raw materials for compression molding
Materials commonly used in compression molding manufacturing include: polyester fiberglass resin systems (SMC/BMC/DCM), polyurethane honeycomb and fiber composites (PHC), long fiber reinforced thermoplastics (LFT) and glass fiber mat reinforced thermoplastics ( GMT).

Features of Compression Molding
High Volume Program
Short (2-4 minutes) cycle times and the use of machined tool steel dies support program volumes in excess of 500,000 units per year.

Optimum tolerances in process kits
The high dimensional stability of the SMC formulation and the use of precision-matched mold tooling produces highly stable and predictable part dimensions, which in turn can produce tight tolerance assemblies.
Class A surface
Automotive-grade Class A surfaces that support topcoat finishes can be achieved using precision-matched tooling that can be polished to a mirror finish.
Wide range of material properties
SMC can achieve a wide range of material properties by varying fiber content, filler materials and performance additives. Materials can be optimized for weight, strength, environmental resistance, economy, and many other properties.
Advantages of Compression Molding
(1) The loss of raw materials is small and will not cause too much loss (usually 2% to 5% of the product quality).
(2) The internal stress of the product is very low, and the warping deformation is also small, and the mechanical properties are relatively stable.
(3) The wear of the mold cavity is very small, and the maintenance cost of the mold is low.
(4) The cost of molding equipment is low, the mold structure is relatively simple, and the manufacturing cost is usually lower than that of injection molds or transfer molding molds.
(5) Large flat products can be formed, and the size of the products that can be formed by molding is only determined by the clamping force of the existing molding machine and the size of the template.
(6) The shrinkage rate of the product is small and the repeatability is good.
(7) A mold with a large number of mold cavities can be placed on a given template, and the productivity is high.
(8) It can adapt to automatic feeding and automatic taking out of products.
(9) The production efficiency is high, and it is convenient to realize specialized and automatic production.
(10) The product has high dimensional accuracy and good repeatability.
(11) The surface is smooth and clean without secondary modification.
(12) Products with complex structures can be formed at one time.
(13) Mass production, the price is relatively low.
Disadvantages of compression molding
(1) The molding cycle in the whole production process is long, the efficiency is low, and the staff has a large physical exertion.
(2) It is not suitable for compression molding of complex products with depressions, side slopes or small holes.
(3) In the manufacturing process, it is difficult to completely fill the mold, and there are certain technical requirements.
(4) After the curing stage is over, different products have different stiffnesses, which affect product performance.
(5) For products with high dimensional accuracy requirements (especially for multi-cavity molds), this process is somewhat short-handed.
(6) The flash of the final product is thick, and the workload of removing the flash is large.
(7) The disadvantage of compression molding is that the mold manufacturing is complicated, the investment is large, and it is limited by the press, so it is most suitable for mass production of small and medium-sized composite products.
Compression Mold
When designing a compression mold, it is necessary to design the cavity according to the size and molding method of the product. In addition, it is necessary to select the appropriate steel according to the quality requirements and needs of the product surface. Molding dies should be made of die steel with easy cutting, compact structure and good polishing performance. Such as P20, 718, 1.273, etc. In addition, it is necessary to consider the related issues of machining accuracy, control the dimensional tolerance, shape tolerance and surface roughness
In order to improve the wear resistance and corrosion resistance of the die surface, surface treatment is usually carried out. Chrome plating is one of the most commonly used methods. Chromium plating can maintain metallic luster for a long time, is stable in various acidic media, and does not undergo chemical reactions. Chrome plating has excellent wear resistance and high heat resistance. When the temperature reaches 500C, there is no obvious change in its appearance and hardness. In addition, nitriding treatment can greatly improve wear resistance.
The parting line design of the molding die should be easy to demould, and the method of simplifying the ejection mechanism can be adopted. When the radial dimensional accuracy of the product is required to be high, the influence of the flash thickness on the dimensional accuracy of m molded products should be considered, and the vertical parting line can easily guarantee the dimensional accuracy of the product.
The temperature of the molding die directly affects the product quality and production efficiency, and the temperature design is usually between 140°C and 160°C. The heating system includes electric heating, steam heating and oil heating. When designing the temperature system of the mold, choose an appropriate heating method to ensure that the surface temperature of the mold is uniform, which can reduce deformation and improve dimensional stability.
In the design stage, use new mold software (CAD/CAM, etc.) to master the whole process of die design, manufacturing, assembly, inspection, testing and production, including mold design and manufacturing cost estimation, mold assembly evaluation, mold parts manufacturing process evaluation , mold structure and formability evaluation.