What is process steps of SMC bathtub mould? Creating an SMC (Sheet Molding Compound) bathtub mould through compression molding is a meticulous and multi-step process. This article will guide you through the key stages involved in producing an SMC compression bathtub mold:
What is process steps of SMC bathtub mould
1. SMC Material Preparation-Cutting SMC material
The SMC material itself is a mixture of chopped glass fibers, thermosetting resin, and various additives. It is prepared by thoroughly mixing these components to create a homogenous compound. The SMC material must meet strict quality standards to ensure consistent product quality.
According to the structure and shape of the product, the feeding position and the process, the shape and size of the sheet cutting are determined, and the sample cutting material is made. The shape of the cut is mostly square or round, and the size is mostly 40%-80% of the projected area of the product surface. In order to prevent the contamination of external impurities, the upper and lower films are peeled off before loading.
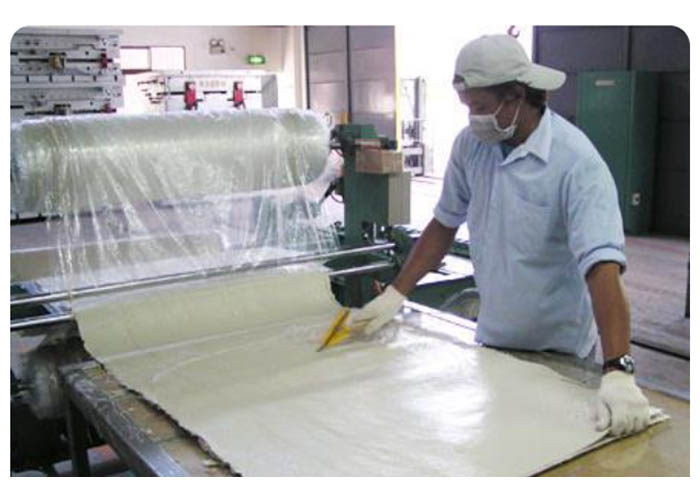
2. Weighing the cutted SMC sheet materials
Weighing the cutted SMC sheet materials

3. Clean the smc bathtub mould
Clean the bathtub mould: Before pressing, thoroughly clean the mould and apply a mold release agent. Before feeding, use clean gauze to wipe the release agent evenly, so as not to affect the appearance quality of the product. For new molds, oil must be removed before use.

4. Place the SMC material into bathtub mould
The position and method of swinging directly affect the appearance, strength and directionality of the product. Under normal circumstances, the feeding position of the material should be in the middle of the cavity. For asymmetric complex products, the feeding position must ensure that the material flow reaches each end of the mold cavity at the same time during molding. The swing method must be conducive to exhaust. When the multi-layer sheets are stacked, it is best to stack the material blocks in a pagoda shape according to the upper and lower ones. In addition, try not to add the material blocks separately, otherwise, air trapping and welding area will occur, resulting in a decrease in the strength of the product.
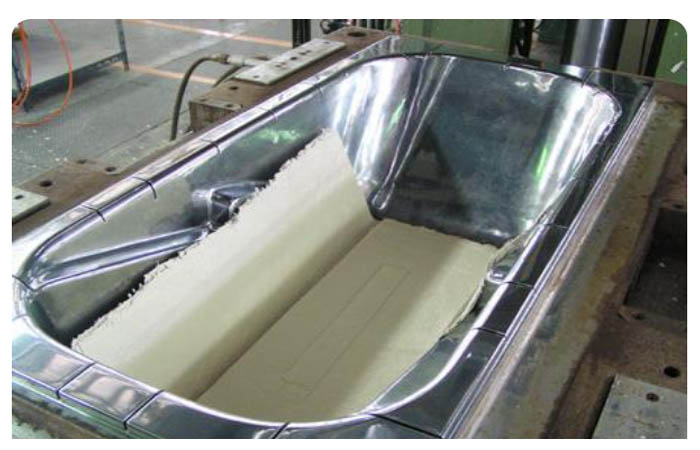
5. Compression molding for SMC bathtub mould
When the material block enters the cavity, the press moves down rapidly. When the upper and lower molds are matched, the required molding pressure is slowly applied, and after a certain curing system, the molding of the product is completed. During the molding process, various molding process parameters and hydraulic press operating conditions should be reasonably selected.
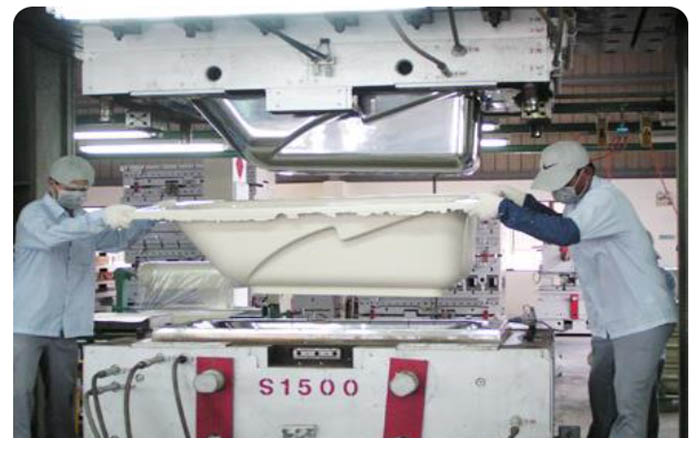
6. Demoulding and Cooling
The curing time (also called holding time) of SMC at the molding temperature is related to its properties and curing system, molding temperature, product thickness and color and other factors.
After the curing process is complete, the mold is opened, and the newly formed SMC bathtub is carefully removed. The bathtub is then allowed to cool and further cure, ensuring its structural integrity and strength.
7. Removal SMC bathtub from bathub mould
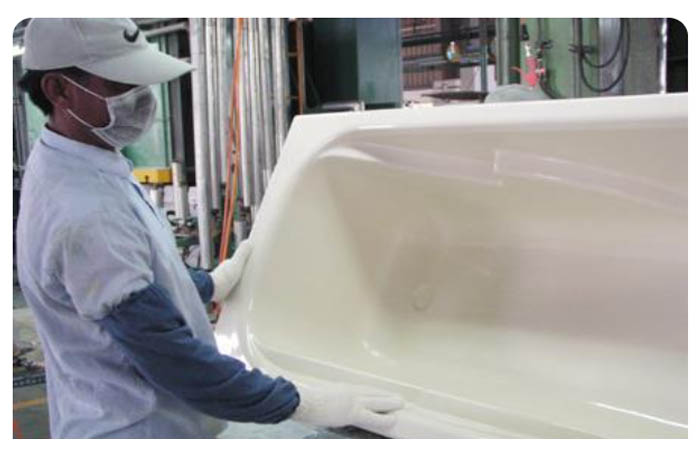
8. Quality Control Checking and Finishing
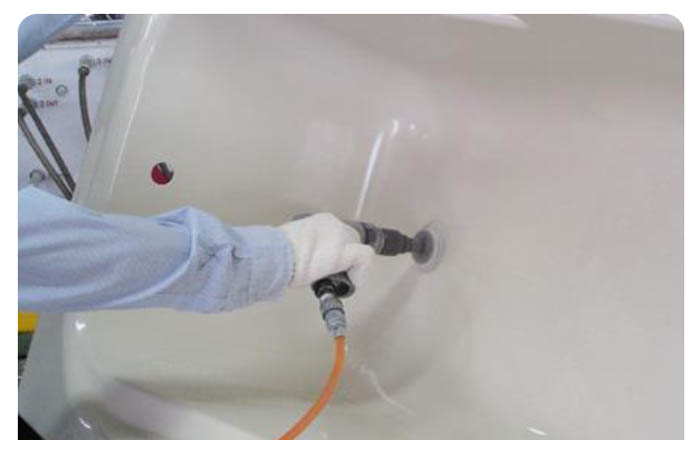
9. Packaging and Shipping
Once the SMC bathtub passes all quality checks, it is ready for packaging. It is carefully packaged to prevent damage during transportation and shipped to its destination, where it can be further processed, assembled, and installed as needed.
In conclusion, the production process of an SMC bathtub mold involves several critical steps, from initial design to mold fabrication, material preparation, compression molding, and quality control. Each step requires precision and expertise to ensure the final product meets the desired specifications and quality standards. SMC bathtubs are known for their durability and aesthetic appeal, making the mold production process a vital part of the overall manufacturing process.